
Case Study
HOW ALDES CANADA REDUCED THE COST OF ITS NEW WORKSTATION BY 65%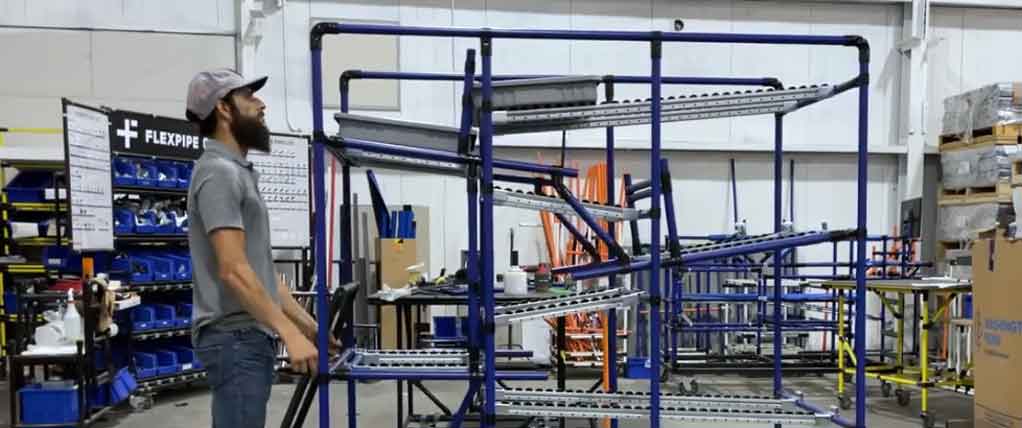
Post
FOUR BENEFITS OF KARAKURI IN LEAN OPERATIONS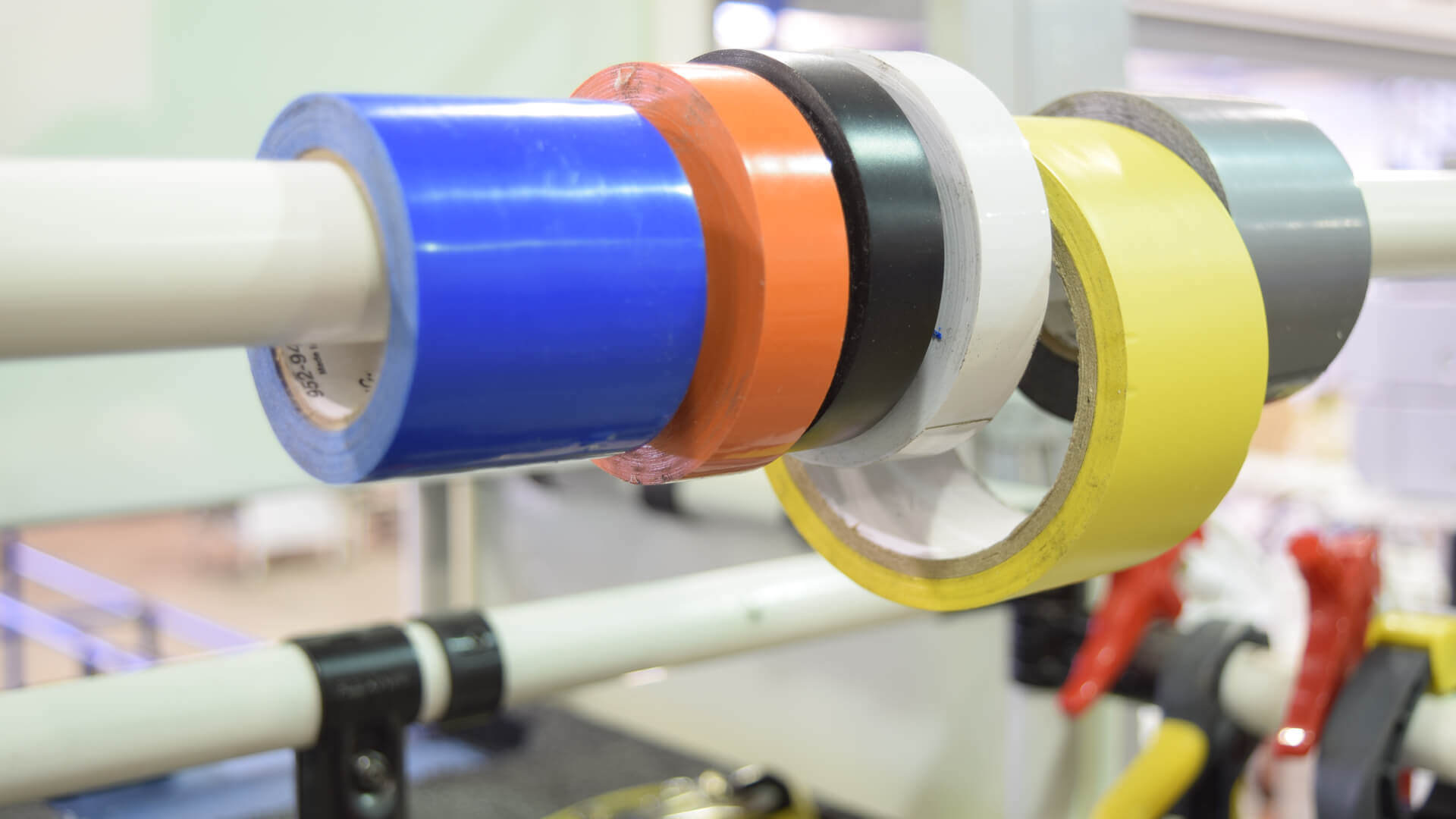
Post
WHAT IS THE 60 SECOND VISUAL WORKFLOW?You’re almost there: 5S principles have been implemented in all workstations and offices throughout the plant, and all employees have all the necessary tools to work efficiently and safely. The last step? Applying the 5th S, Sustain (Shitsuke in Japanese), recurrently. We have tested five applications for you that will help you accomplish this task.
To put yourself in the situation, let’s take a look at this table to get a better idea of what are the 5S and where the follow-up is compared to 4 others. Click on the image to enlarge it and print it as needed.
Download the PDF version of this table
The last S is often perceived as the hardest to apply, as it involves remaining steadfast in keeping up good practices. As such, it’s often the most neglected.
The process is akin to someone who decides to start training to get in shape. The person chooses the best way to reach their objectives, develops a plan, and acts on it. If the initial plan is not followed and the person derails from their goals, the result (getting into shape) is compromised. As such, the “Sustain” step of the 5S calls upon self-discipline to continue good habits. Without this 5th pillar, the efficiency of the other S’s is reduced.
To make the job more comfortable for the manager who will guide each employee in evaluating their workstation, here are a few applications to help carry out the audit and the follow-up after the audit. They can be installed on a smartphone or tablet.
The mobile app is essential for a 5S audit. There are several available for iPhone or Android, and we have reviewed a few of them for you.
Tulip offers a variety of tools that can scan data from your business’ production line. This development platform allows businesses to create specific versions of applications, including quality evaluation, 5S audits, primary cause analysis, and visual management.
(Visit their web site)
Tulip offers a variety of tools that can scan data from your business’ production line. This development platform allows businesses to create specific versions of applications, including quality evaluation, 5S audits, primary cause analysis, and visual management.
Here are the Tulip app’s features:
Source: Tulip (https://tulip.co/app/5s-workspace-audit/
Source Appli Lean 5S: http://www.apilean.com/appli-lean-5s
The Lean 5S app is a question-and-answer based model where the answers are selected from world-renown best practices by lean manufacturing experts. The questions cannot be personalized with the app, contrary to the other apps we reviewed. The only way to do so is by mandating Lean 5S App to do it for you. The app is available in 4 languages: English, French, Spanish, and Portuguese.
Here are the available options:
(Source Appli Lean 5S: http://www.apilean.com/appli-lean-5s/)
The GoCanvas app provides continuity of audits, thereby ensuring consistency with regards to cleanliness, organization, and efficiency in your work environment. GoCanvas audits adapt to all work sectors. This tool can help oversee the quality of your work environment on a sustained and ongoing basis and a way for work teams to adhere to established standards.
The apps for each audit type can be built very intuitively and do not require in-depth programming know-how. All you need to do is drag-and-drop the features you want in the app, and give them the desired shape (calculator, drop-down menu, checkboxes, barcode, calendar, photos, etc.). These features distinguish GoCanvas from the rest of the apps. Its customer service is also noteworthy.
Here are the app’s main features:
(Source: https://www.gocanvas.com/mobile-forms-apps/2983-5S-Audit-Form)
Pricing: https://www.gocanvas.com/show_pricing_plans
At Flexpipe, we use iAuditor, which we consider to be among the best apps on the market. Its intuitive and adaptive interface can manage audits in other sectors, not only 5S audits. iAuditor also focuses on safety and inspections. You can prepare your audit model on the iPad and subsequently use it on your smartphone. Several audit models are suggested in the app’s library.
Bye-bye paper! You can write your notes directly in the app for each item evaluated.
Rémi uses the app to document Gabriel’s workstation and add photos to it.
Pictures of the workstation being evaluated can be taken in the app and linked to the element being evaluated. These pictures act as proof and as a reference to instill discipline. They can also be used as illustrative purposes for the team when posted on information boards.
Here are iAuditor’s features:
Once the audit is finished, the app produces a report which can be quickly sent by email or printed for use at a later date.
Managers have much to gain by promoting a positive image of a 5S audit. It’s not a question of a verification; instead, it’s more about ensuring that existing standards are respected. It must be perceived as a way to make the employee’s work easier.
We sat down with Éric, who is a team leader and assembler at Flexpipe. After receiving training on 5S principles, audits now make perfect sense to him. He actively participated in standardizing workstations. The efficiency he gained following the standardization process translated into a significant reduction of production time. Where he once walked between 5 and 6 km per day on the production floor, that number is now between 3 and 3.5 km. Also, given that there is less handling to do, the risk of injury has decreased. He is convinced that audits are necessary so that the benefits keep paying off following the changes.
Éric concludes by saying: “In the spur of the moment, we tend to choose the easy way out. It’s easy to stray from the standardization that was implemented and revert to old habits. In the end, it’s a losing proposition. Audits are a way of reminding us of this.”
The lack of discipline and rigor comes at a high price for manufacturing companies. Material that is only used occasionally is, ultimately, an unnecessary expense. Furthermore, work-related accidents are insurance costly. One can conclude that the benefits of upholding standards are measured in dollars, energy spent, space occupied, and are, as a result, not negligible.
____________________________________________________________________________
WHAT CAN FLEXPIPE DO TO OPTIMIZE YOUR PLANT EFFICIENCY?
Flexpipe Modular industrial pipe racking system can help you with implementing continuous improvement principles. Your team’s creativity can result in a 10% increase in productivity per year. It has been a proven system for more than 50 years now.