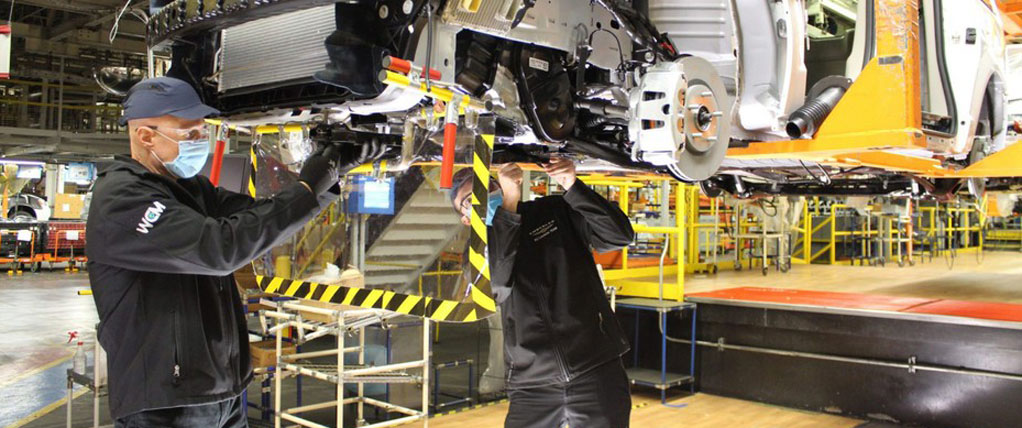
Post
BORROWING LEAN MANUFACTURING CONCEPTS FROM THE AUTOMOTIVE INDUSTRY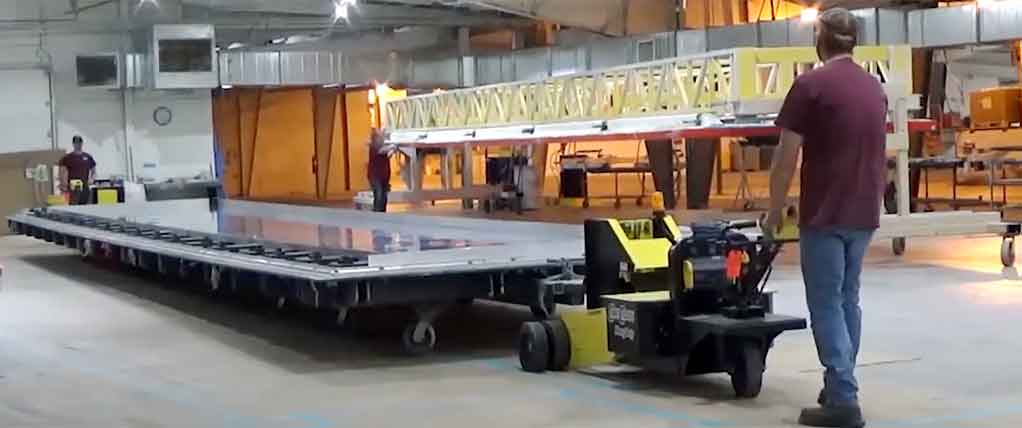
Post
HOW TO OPTIMISE MATERIAL FLOW WITH A TUGGER CART SYSTEM?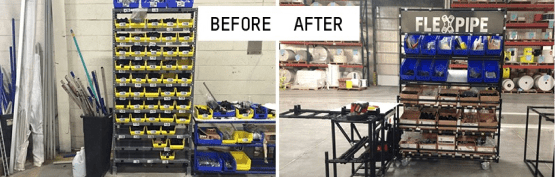
Post
5S GUIDE - A LEAN MANUFACTURING TOOLConstruction Innovations – a well-established and successful enterprise with approximately 700 employees – is a leading provider of fully-integrated electrical solutions for the construction and energy industries.
Construction Innovations , turned to Mark Zeilinger of DPMG Corporation and Flexpipe’s tube and joint system to optimize their 320,000-square-foot facility’s to lean manufacturing operation.
Read on to learn how the Manufacturing Engineering team at Construction Innovations used Flexpipe’s steel piping solution to streamline work cells, increase production and improve ergonomics throughout the facility.
Despite Construction Innovations’ success, there were some issues regarding their existing production processes. The company had increased its volume rapidly year over year and needed to increase both throughput and capacity within a limited footprint. Iitially, workstations and material handling structures were made of wood, which made them bulky, hard to maneuver and took up excess space on the production floor. Additionally, they were beginning to show signs of wear and tear.
As stated by a member of the manufacturing Engineering team,
“We encountered some instances where materials and semi-finished goods weren’t in their proper place. It impacted production. Our workflow needed improving, and our wood structures were becoming outdated.”
As an active Continuous Improvement Network (CIN) member, Construction Innovations is always looking for ways to improve its processes. The company’s continuous improvement mindset pushed the team to rethink its batch production process and replace its outdated wooden workstations and material handling structures with Flexpipe’s lean, robust, modular, and scalable solution.
By the end of their full adoption of Flexpipe’s tube and joint solution (for just one work area), the company shifted from its batch production process to a pull system predicated on a one-piece-flow production process.
Resistance to change is common when employees have a vested interest and buy-in to the existing methods.
However, once you take the time to explain what those changes are and how they’ll help the employees, they begin to embrace the change fully.
In most cases, concerns about change are rooted in how the proposed changes will impact the company and impede the employee’s workflow. This is why it’s important to anticipate that resistance. It’s often born out of unfamiliarity with the proposed changes. However, once you take the time to explain what those changes are and how they’ll help the employees, they begin to embrace the change fully.
In the case of Construction Innovations, employees weren’t necessarily frustrated, but they did feel that some improvements needed to be made. As is often the case with continuous improvement initiatives, some employees were more receptive than others. However, over time, the changes initiated started to win employees over.
This is precisely what happened at Construction Innovations; as a Manufacturing Engineering team member explained,
“After the changes, everything now has a clearly-defined space. Workflow improved. Production volumes improved, and employees were no longer as stressed because they knew where things went and what was next.”
The Manufacturing Engineering team wasn’t alone on their journey. Aside from the technicians and employees, they also had the benefit of working with DPMG Corporation, a lean consulting firm and strategic partner of Flexpipe Inc.
Mark and the rest of the highly-experienced consulting team at DPMG Corporation always use Flexpipe on their projects. The ability to quickly create, change and modify material handling structures is an ideal fit for their continuous improvement teachings.
The success of continuous improvement initiatives depends on the entire company’s involvement. It can’t succeed with just one person pushing an initiative. It can’t succeed without management buy-in. Far too many companies make the all-too-common mistake of allocating all the change responsibilities to a single individual who then fights and struggles to implement practical improvements.
Continuous improvement must be part of the company’s culture. It must come from the top down, where senior management fully endorses and pushes lean and continuous improvement methodologies. Without management buy-in, continuous improvement rarely, if ever, succeeds.
Fortunately, this was never a concern for the management team at Construction Innovations. They took a proactive approach and fully endorsed these initiatives. They understood that improving production would ultimately upgrade conditions for employees while benefiting the company’s customer base.
While some employees were initially reluctant, that apprehensive quickly dissipated. As the Manufacturing Engineering team started to build structures, improve the workflow, upgrade the workstations, and adopt 7S principles, they noticed an immediate change.
Employees started coming forward with suggestions. They began envisioning Flexpipe’s potential looked forward to the changes in their work areas. Minor incremental improvements in structures began to build upon themselves. More and more employees had suggestions to improve Flexpipe structures and processes.
Two examples of how Construction Innovation employees requested simple adjustments to make their Flexpipe workstations more user-friendly.
The team used visual queues and markers on the floor to indicate where structures needed to be placed. This helped employees remove the structures, clean the workstation, and quickly put the structures back in place.
In addition to seeing improved workflow and increased employee engagement, they also started to notice that the training time of new employees had dramatically improved.
As stated by a Manufacturing Engineering team member,
“With a better workflow, newer structures, and clearer process, the ability to train new employees also improved. Before the change, new employees might have taken two to three days to learn how to complete an assembly. Mark and I saw new people who could complete the assembly at the end of their first day!”
Replacing wood structures with new Flexpipe structures also opened the space, and employees could better communicate with each other. Before, the wooden structures were so large and closed off that employees and lineside managers couldn’t see one another, let alone speak to each other.
Initiating change is one thing, but seeing those changes empower the employees is something else altogether. It is the ultimate rewarding experience.
The employees felt empowered to improve their process, workflow, Flexpipe material handling structures, and Flexpipe lean work cells. They committed to improving workstations and Flexpipe structures and offered fantastic insight into little things that could be added to those structures.
The goal of any lean work cell is to ensure that the operator or technician rarely has to leave the work cell to retrieve materials, tools, instructions, or semi-finished and work-in-process goods. Everything the employee needs should be readily available in the lean work cell.
Employees’ suggestions included putting small garbage bins, shortening pipes to save space, and adopting 7S principles to ensure every tool and consumable had its place. Their suggested changes started a cascading effect, and other employees soon joined in with their suggestions.
As stated by Manufacturing Engineering Team member,
“An operator would say “I need this” and we would ask why do you need it? Is there a better tool we can provide, or is there a design change we can make to the Flexpipe structure? In each case, the employees had a valid and well-thought-of reason for making a change for the better.”
The benefits of these changes were endless. Employee morale and motivation improved. Training time for new employees drastically improved from three days to a single day. Spaces were more open, and communication between work cells, technicians, employees, and line-side managers became much more accessible.
The entire team fully embraced the continuous improvement mindset. Each incremental improvement helped to make work easier to complete. Employees adopted 7S principles to improve tooling stations so every tool and consumable had a designated place. No more time wasted looking aimlessly for critical tools, materials, or instructions.
Work cells became mobile solutions with floor indicators. Flexpipe structures could easily be rolled out of the workstation while being cleaned. After the cleaning, the mobile Flexpipe structures would be easily moved back into place under their designated floor indicators. These portable structures come with Flexpipe’s 6-inch heavy-duty wheels, which are durable, strong, and ideal for industrial floors.
The results were astounding. Before the changes, Construction Innovations had a production goal of 10 daily units with 25 people. After the changes, the production skyrocketed to 30 units/day, representing a 300% increase with the same number of employees. Training times for new employees decreased by 300% as new employees became more self-sufficient and fully trained at the end of their first day instead of taking three days before.
Change is rarely easy. It takes a committed and dedicated workforce willing to go through the journey of changing things for the better. It takes leaders like Mark and the KE Team. It takes employees who are eager to try new things, and it takes a management team that fully embraces continuous improvement.
The KE Team , and the team at Construction Innovations proved that simple, small, and incremental improvements can dramatically affect employee morale, workflow, and safety while substantially improving production throughput.
If your company adopts similar approaches, there’s no telling what you can accomplish.
To learn more about how Flexpipe’s solution can help your company, book an appointment by contacting us now.