G&W Canada manufactures electrical products specializing in power lines, electrical boxes for skyscrapers, etc. Their production cart was not suitable for their needs in terms of ergonomics and capacity, so they called on Flexpipe to help them manufacture lean carts that would meet their needs. Estimated reading time: 3 min.
Located in Brampton, Ontario, G&W Canada is an electrical products manufacturer specializing in switchgear, distribution reclosers and overhead switches.
About 90% of its production is destined for the American market. The company recently used Flexpipe to improve manufacturing processes for its electrical modules designed for high-rise electrical boxes.
The challenge
The carts used by G&W Canada to store electrical modules were not suitable for the plant’s production cycle:
1- Because of their low-profile wheels, the carts were difficult to push. Even when empty, they did not push well, wasting valuable employee time.

2- The carts could accommodate only 18 modules manufactured per production cycle. Workers therefore had to use two carts at the same time. Often there were half-full carts in the factory.
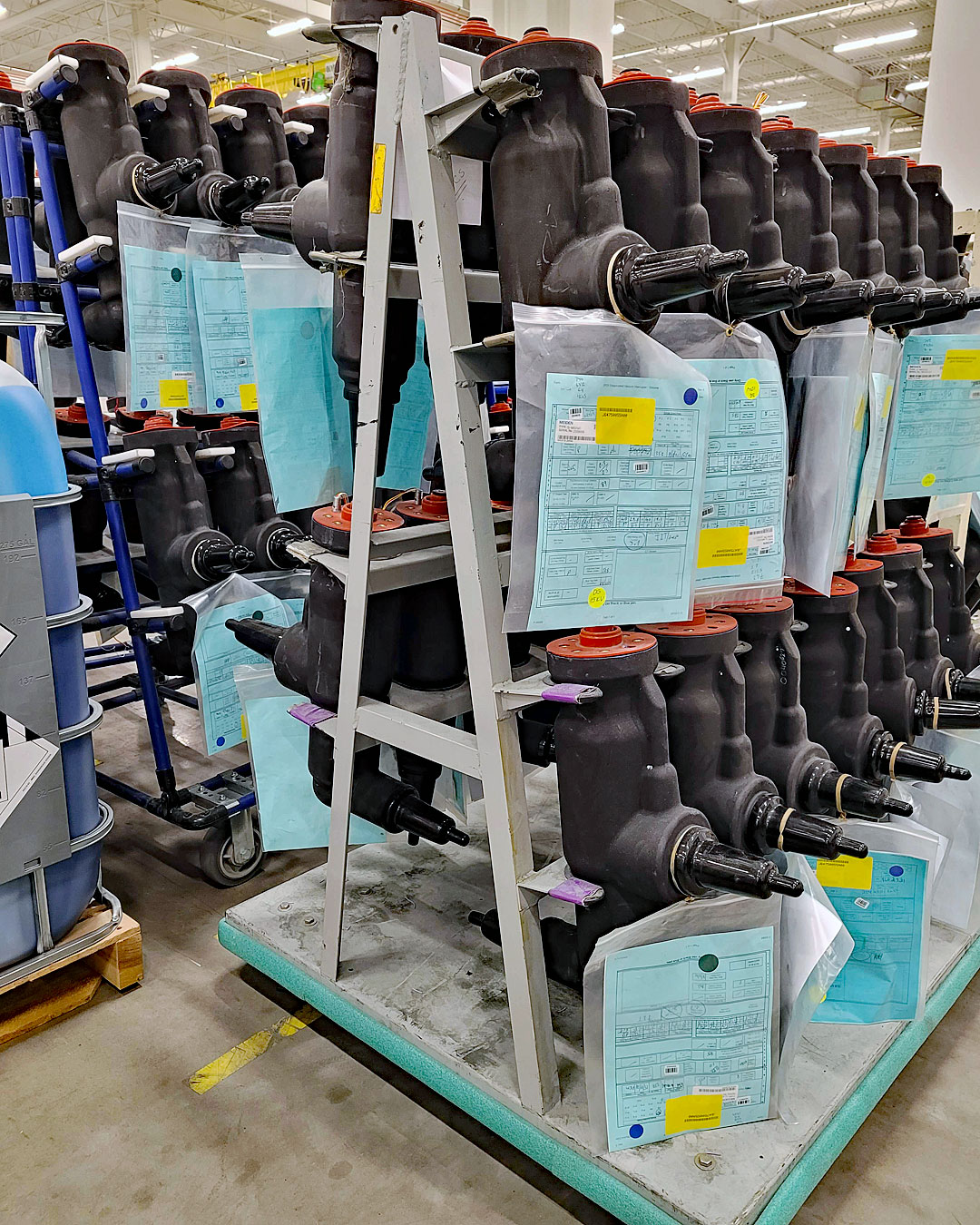
In addition, there were not enough carts in which to store all of the modules produced on a daily basis. When the carts were full, the remaining modules had to be stored in wooden crates placed on the floor.

Employees who needed these modules were forced to bend over to pick them up, increasing the risk of injuries and accidents on the job. In fact, each module weighs approximately 15 kilos.
The solution
We offered to manufacture custom Flexpipe carts for G&W Canada. After making a few prototypes, we managed to design carts that perfectly met the needs of the business.
Each of the Flexpipe carts can store up to 24 modules, two more than the amount from a standard production run of 22 units. The two additional storage spaces can be used as production speed increases. Thus, employees use only one cart, which helps increase overall productivity and frees up plant space.
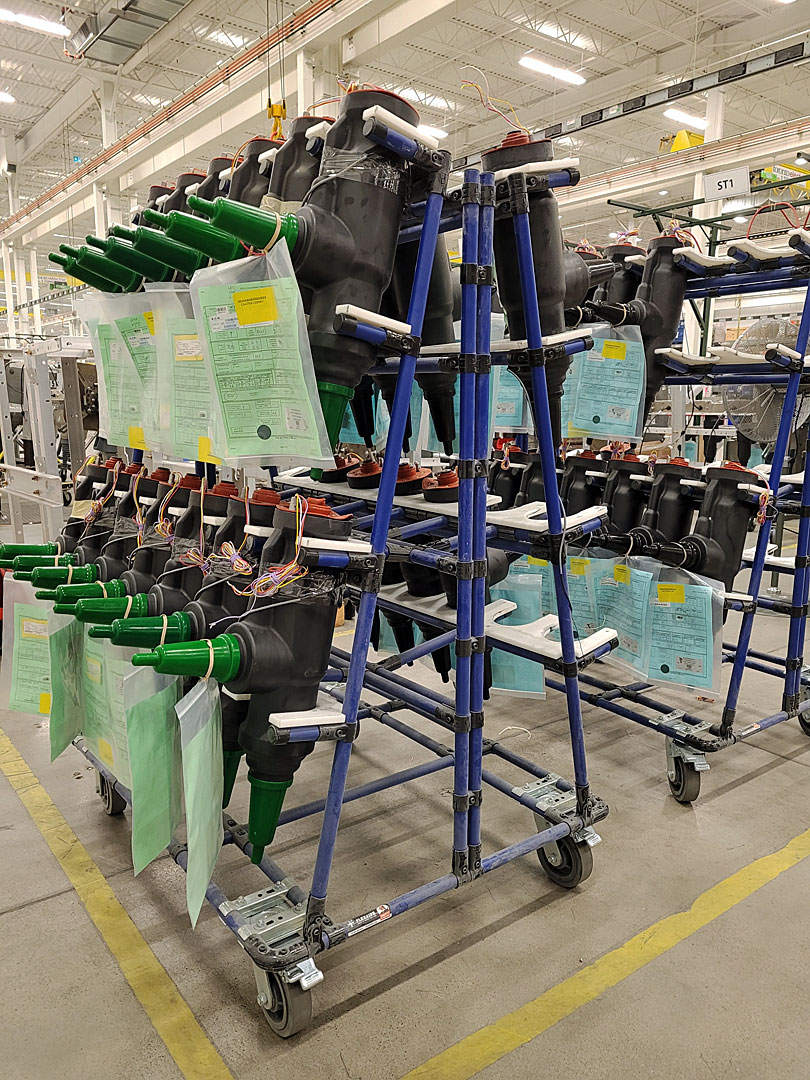
Visual management
The Flexpipe carts also feature three color codes so that workers can quickly identify the status of the modules:
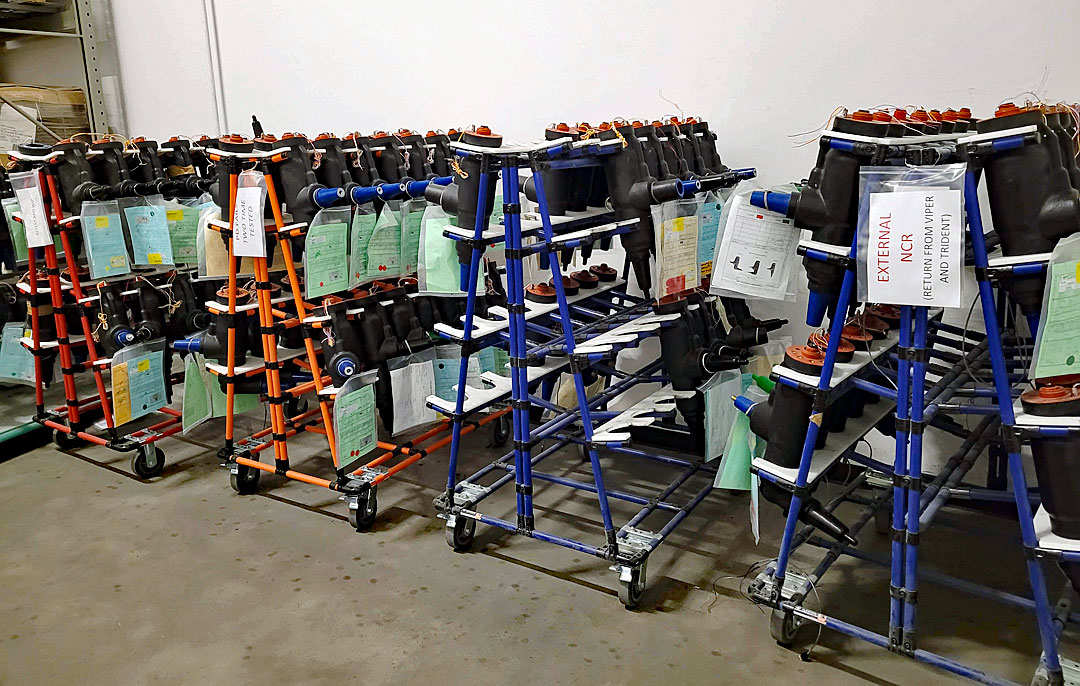
- Orange. The modules must be inspected.
- Red. The modules did not pass inspection, in particular, due to production defects.
- Blue. The modules are ready.
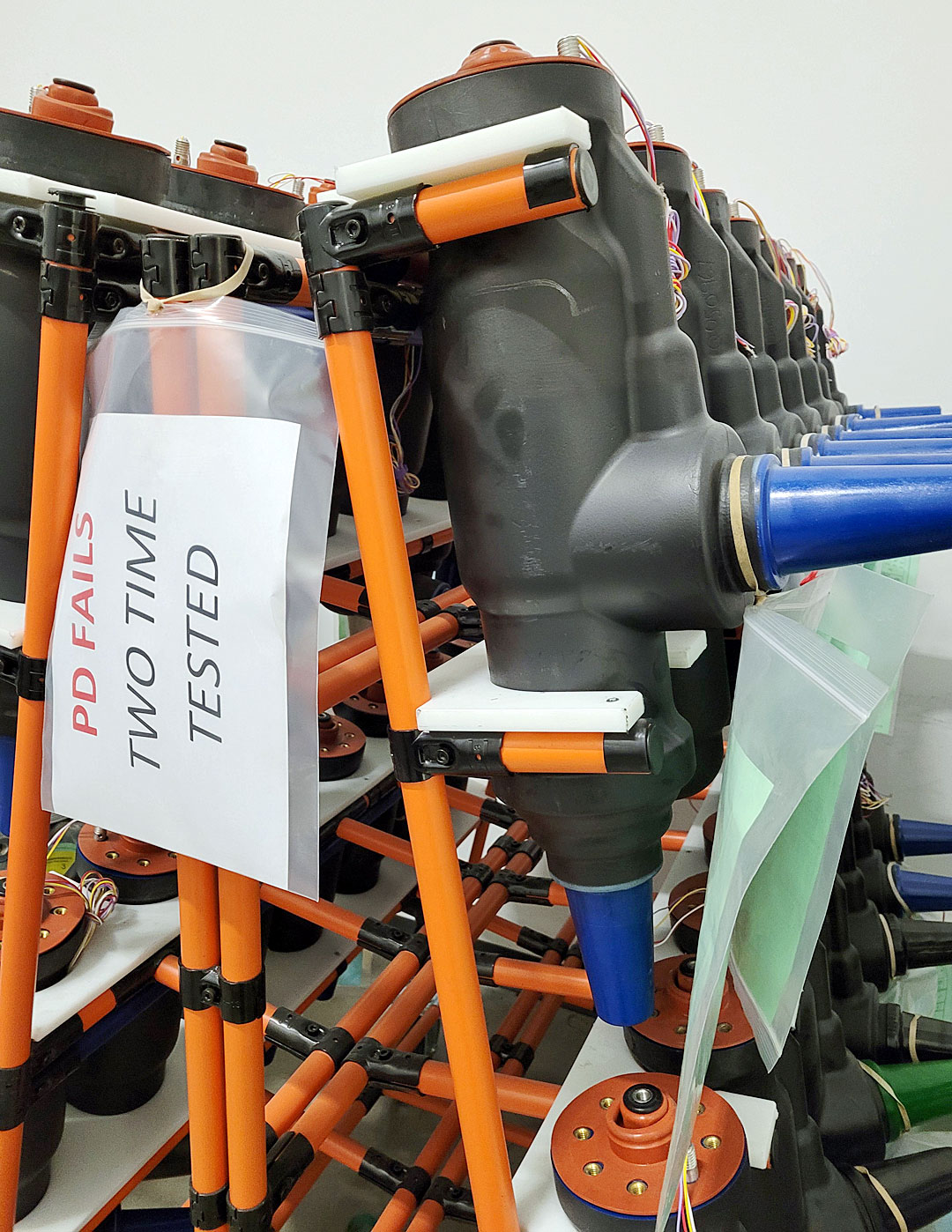
Obviously, the Flexpipe carts are strong enough to support all the modules and are much easier to handle than the old, welded steel carts.
At the same time, we also built small carts for drying the modules.
The results
G&W Canada has noted productivity gains in the manufacture of electrical modules. Employees no longer have to operate two carts and can quickly locate modules in the plant.
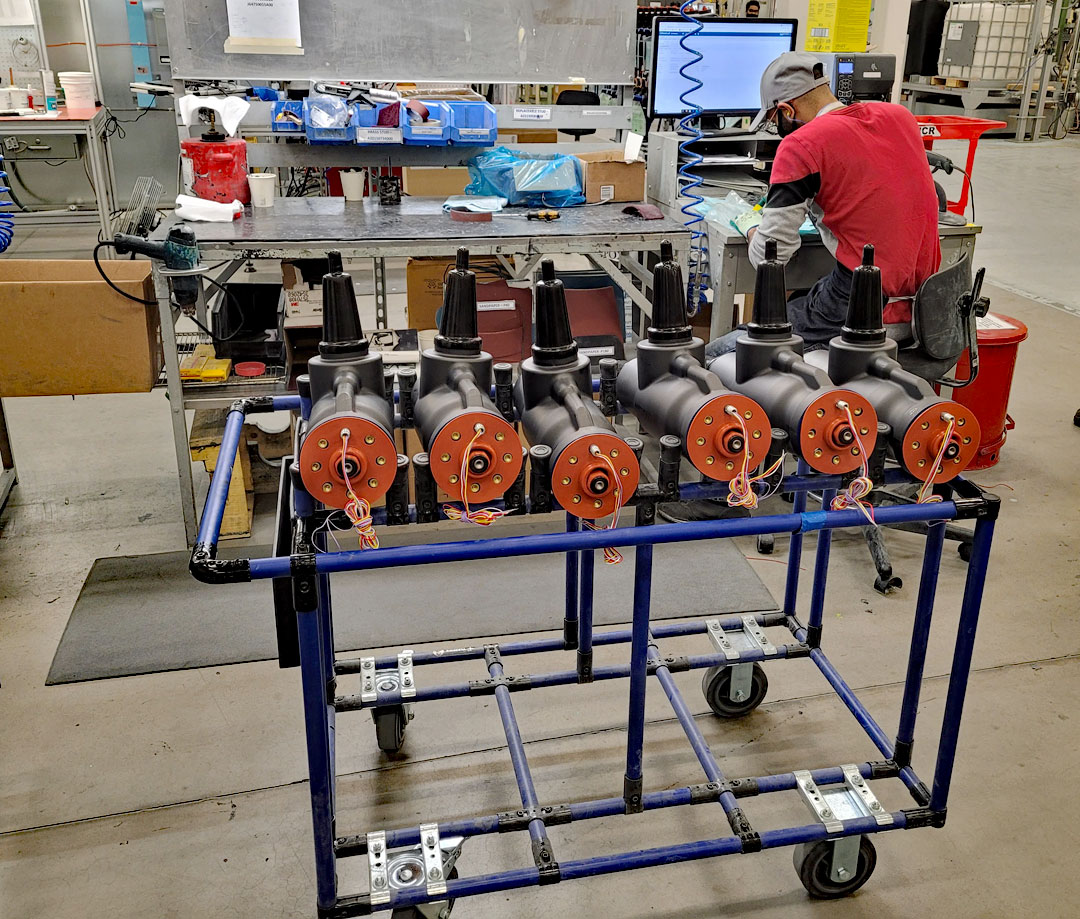
The risk of workplace accidents has also decreased, as the Flexpipe carts are easier to push than the older ones. Workers also no longer have to bend down to pick up heavy parts from the ground as there are now enough carts.
In short, we are happy to support G&W Canada in improving its working methods!