Comprehensive Guide to Tugger Carts with Flexpipe: Basics, Technical Insights, and Practical Applications
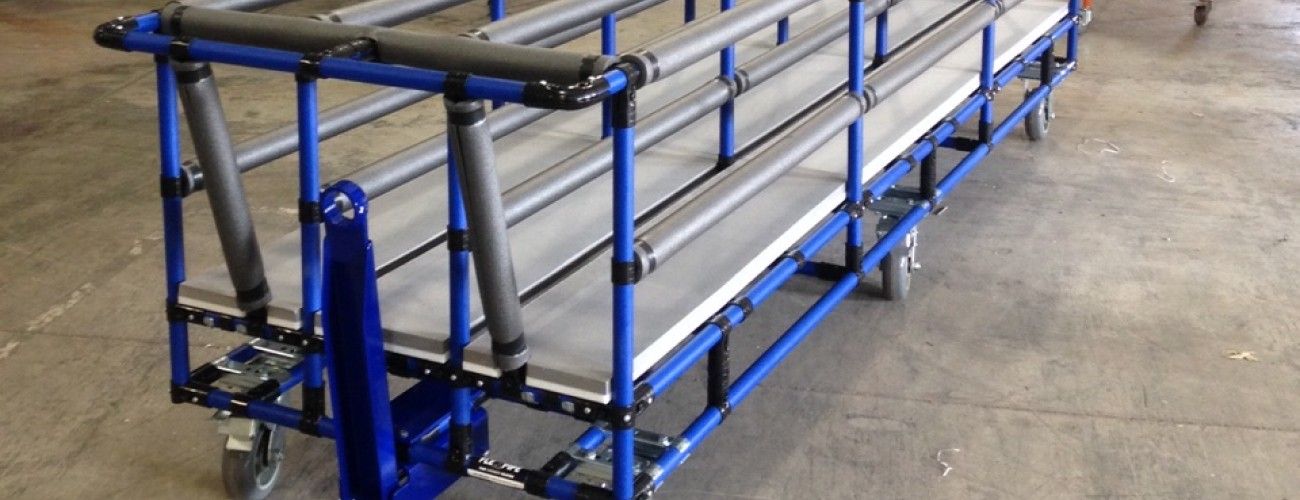
A tugger cart is a material-handling wagon or carriage that holds and transports materials, semi-finished goods, finished goods, and consumables within a warehouse, distribution center, storage area, or manufacturing facility. Depending upon the weight the cart is supporting, a single tugger cart can be manually pulled or pushed.
This tugger carts guide explains the basics of tugger carts. It answers commonly posed questions and explains how building tugger carts with Flexpipe steel tubes and joints is a lean, low-cost, safe, and efficient way to move materials and goods.
Read on to learn more about the importance of tugger carts from this technical guide for tugger carts.
Multiple Carts are Called Tugger Trains
When two or more carts are combined, they form what is commonly referred to as a tugger train. A single operator typically controls these trains using a battery-powered tugger or caddy. These battery-operated tuggers/caddies allow multiple carts to be moved simultaneously, which is a safer and faster alternative to using one-at-a-time, single-load forklifts.
Tugger carts are an indispensable tool in logistics and manufacturing because they allow companies to transport large volumes of material and goods safely and efficiently. They are often viewed as a critical part of lean manufacturing environments where eliminating waste is accomplished with efficient transportation processes.
Tugger Cart Basics
Tugger carts are used in many applications and have no uniform dimension. Carts can be designed in various sizes and configurations to suit any situation where quickly and safely moving parts and goods are critical to saving time and reducing costs. However, there are some commonalities that all carts share.
What are the components that make up a tugger cart?
All tugger carts require a durable, high-strength frame, industrial strength casters (wheels), a robust and sturdy platform where goods and materials are laid or positioned, a hitch or coupling device to mate with other carts or to be pulled/pushed, and a tow arm.
Parts you’ll need to build your next tugger cart

SPRING LOADED TOW BAR FEMALE
CO-SLF
CDN $202.23

SPRING LOADED TOW BAR MALE
CO-SLM
CDN $63.67

LEG WRAPPER TOW BAR FEMALE
CO-LWF
CDN $139.10
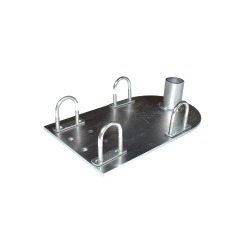
LEG WRAPPER TOW BAR MALE
CO-LWM
CDN $63.67

SQUARE BLACK 8′ STEEL PIPE
SQP-96-BK
CDN $48.15

CORNER STEEL PLATE FOR SQUARE PIPE
SQS-CORNERP
CDN $34.83

4” PLATE SWIVEL CASTER WITH BRAKE
W-4PSB
CDN $14.28
Why are tugger carts used, and what advantages do they offer?
Companies use tugger carts because they offer a safe and efficient way to transport large amounts of materials, consumables, and finished goods. Without tugger carts, companies would have to move large loads one at a time using a forklift.
It takes longer with a single-load forklift, and the risk of injury loading and unloading materials and goods increases when using a forklift. Tugger trains can provide critical parts and materials to multiple locations and lean work cells in a single run/trip, whereas a forklift would have to make multiple trips to accomplish the same task.
How does a tugger cart differ from other types of industrial carts?
Industrial carts are typically single-carriage, all-purpose carts that move small-volume consumables, tools, and materials over relatively short distances. In manufacturing environments, an industrial cart would typically be used by a technician or operator to manually move materials and goods between adjacent lean work cells. This differs from a tugger cart designed and manufactured to carry heavy loads and be pulled by a battery-powered caddy over long distances.
What industries commonly use tugger carts?
There is no shortage of industries that rely upon tugger carts. Any large-scale manufacturing or fabrication environment will likely have a tugger cart or train. The larger the manufacturing facility, the more critical it is to have tugger trains.
Tugger carts are also used in warehousing, wholesale, retail, and distribution outlets in a wide range of commercial, industrial, and consumer markets. Automotive, aerospace, plastic injection molding, hydraulics, medical, and pharmaceutical are just some of the types of industries that need tugger carts.

Technical Insights and Tips
There are multiple variables to consider when designing, manufacturing, or assembling tugger carts. The goal is to create a cart that adequately supports a predetermined load without buckling, bending, or breaking. This ultimately means designing a well-constructed, sturdy, and safe cart.
When designed properly, a tugger cart can also act as a fail-safe or error-proofing Poka Yoke by loading only the right-sized parts, goods, and materials onto the cart. This might include having slots for specific bin sizes or material sizes. This would save tremendous loading, unloading, and travel time.
Why are angle calculations crucial in tugger cart design?
Think about how important it is to have a well-designed, safe, stable cart with good maneuverability. A poor cart design that might easily tip over makes moving and transporting the cart risky. Proper angle calculations ensure the cart is not only safe but that it evenly distributes the weight it’s supporting.
Angle calculations also play a critical role in ensuring the cart is stable and easily moved without the operator or technician overexerting themselves. In this case, it’s a question of ergonomics and safety. Improper calculations on the placement of the casters would make moving the cart extremely difficult. Finally, improper calculations will result in undue stress and high loads being applied to portions of the cart, which could lead to premature failure.
Tools or methods to assist with accurate calculations.
Fortunately, the days of relying upon laborious, manual calculations and cumbersome tools like protractors are long gone. Today’s carts can be designed with intuitive computer-aided design (CAD) software solutions like AutoCAD, MicroStation, SolidWorks, Solid Edge, and CATIA, among others. These solutions have made design a much simpler, safer, and error-free exercise.
One solution that helps customers design and assemble their carts is Flexpipe’s Creator Extension, a simple, effective, and intuitive plug-in to SketchUp. Unlike AutoCAD, where users spend significant time manually moving and positioning objects, Flexpipe’s Creator Extension does all those tasks for you. Need a four-foot long, two-foot wide, and five-foot-tall flow rack? Move your mouse to those dimensions on the screen and click a button, and Creator Extension will occupy the entire skeletal structure for you – calculating the length of pipe, number of connectors, and joints.
Wheel Types and Selection
There are several options to choose from when selecting wheels for your cart. Flexpipe provides rigid casters and swivel casters with or without brakes in addition to rigid and swivel electrostatic discharge (ESD) casters with or without brakes.
How do I determine the best wheel type for my tugger cart?
There are several variables to consider when choosing wheel types. First, think about the type of floor the carts will be transported and moved over. Second, decide whether your cart will only travel in a straight line or must swivel to be maneuvered into different areas.
Third, ensure you’ve correctly determined the load capacity for your cart and that your chosen wheel is sturdy, strong, and reliable enough to support that weight. Finally, decide if you’ll need ESD-compliant wheels and whether you’ll need brakes.
Tips for ensuring maneuverability, durability, and optimal space utilization.
Regarding maneuverability and space utilization, swivel casters are the best wheel option. They allow operators and technicians to easily rotate individual carts 360° while making it easy to position carts in tight-fitting spaces. In terms of durability, it becomes a question of material selection. Rubber wheels have excellent shock absorption and good traction. Other materials like polyurethane, steel, and nylon have pros and cons but are often harder to purchase depending upon supply. Ultimately, in a heavy-industrial setting, where a tugger cart or tugger cart train must travel over longer distances, a high-quality, durable, heat-resistant rubber is always the best option.
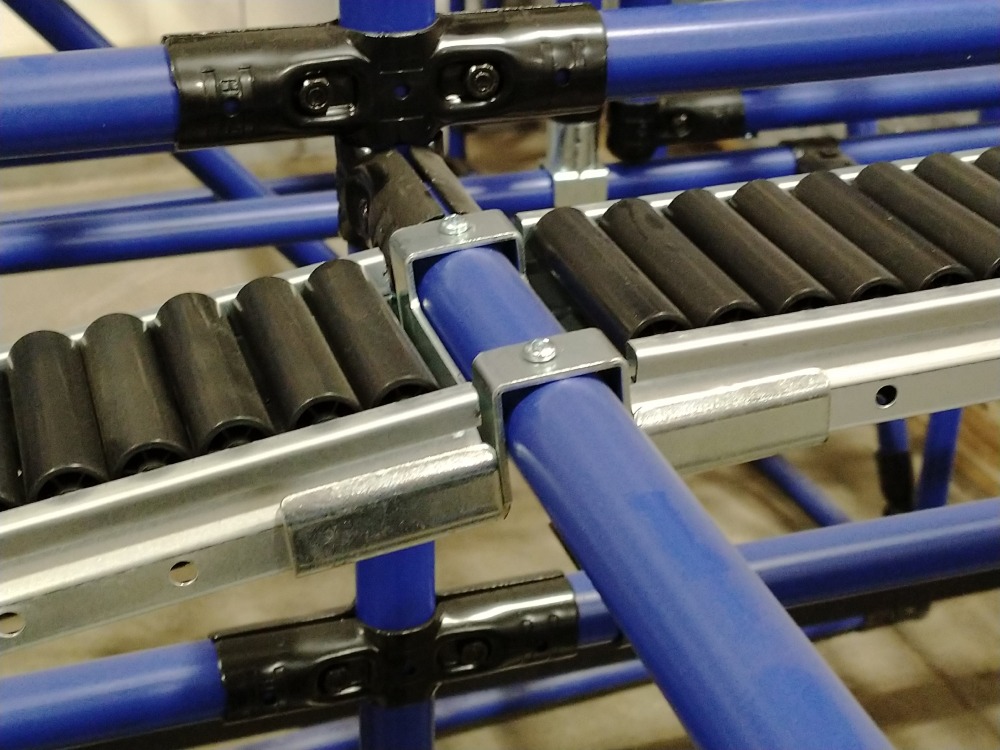
Weight Considerations: What is the weight capacity for a standard tugger cart?
Unfortunately, there is no hard and fast rule regarding how much weight a standard cart can support. Given the wide range of uses for carts – and all the types of materials, tools, parts, consumables, and packaged goods they transport – and all the industries they’re used in, it’s simply impossible to define a standard weight.
Any cart you purchase will come with instructions as to the maximum loading capacity for the cart. Even the caddy used to pull the tugger cart train will have a maximum towing capacity, allowing you to determine how many carts you could push without exceeding the caddy’s capacity. However, one way to customize your cart to carry the weight you want is by building tugger carts with Flexpipe tubes and joints.
Building with Flexpipe: Advantages and Techniques
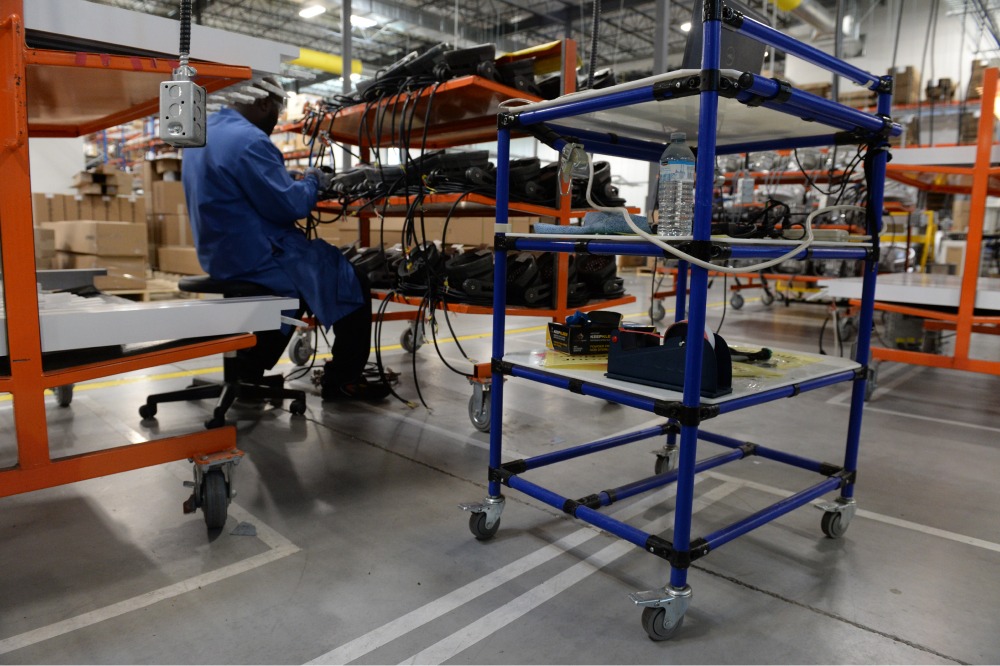
Think of Flexpipe’s tube and joint system as the ultimate erector set. This cut-to-length-and-assemble system originated from the Toyota Production System (TPS). Toyota is the originator of several lean manufacturing and continuous improvement methodologies like 5S and Kaizen. This means the steel tube and joint system has been used for over 70 years, making it the ultimate lean solution.
Flexpipe is a modular and scalable system that allows you to tailor your carts to whatever size or dimension you need. Customization is critical with Flexpipe. Need to make your cart larger? OK, go ahead. Want to add another level to one of your flow racks? No problem. Looking to maximize the square footage of your shop floor with customized work benches? Yes, you can do that as well.
Can I customize a tugger cart to fit specific dimensions or load capacities?
Yes, absolutely. With Flexpipe, you can customize your cart to fit any bin size or load requirement. In fact, the first all-important step to designing any Flexpipe cart is to calculate its loading capacity.
Fortunately, we’ve made this step easier with our Flexpipe loading capacity calculator. This easy-to-use tool calculates the weight each steel pipe can support based on its length and thickness. These results come from in-depth third-party testing where multiple lengths and thicknesses of pipe were compression tested on Instron machines.
Are there specialized tugger carts for unique requirements?
Several specialized tugger carts can be designed and assembled with Flexpipe for various applications and requirements. Flexpipe’s solution includes steel pipes, joints, casters, tracks, decking, kaizen foam, and square pipes. The square pipes are specifically designed for the base of tugger carts. A single 12-inch (1-foot) Flexpipe square pipe can support an astonishing 4,221.7 lbs, making it the ideal solution for the base support structure of all tugger carts.

Customers in automotive and aerospace have used Flexpipe’s simple solution to design mobile carts that can be loaded and unloaded onto trucks, ensuring safe delivery of integrated assemblies. These customized mobile carts properly secure parts in place and protect the assemblies in transit. They are highly maneuverable carts that are reused constantly.
Mobile-optimized carts can include Kaizen foam for accurate consumables and tool placement. These mobile carts can then be moved between workstations. There is no shortage of ideas for specialized tugger carts that can be designed and assembled using Flexpipe’s steel tube and joint system. Any tugger carts guide should provide plenty of layouts and ideas for tugger carts.
What are the benefits of using Flexpipe for tugger cart construction?
A simple three-level, manual push, welded cart 42L x 24W x 35H goes for approximately USD 700 to USD 900, depending upon the manufacturer. In some cases, freight is extra. This is a cart whose dimensions can’t be changed and can’t be adjusted. It doesn’t fit any specific bin size and often gets overloaded.
A Flexpipe cart with the exact dimensions would typically cost USD 250 to USD 300. Keep in mind that this is simply a manual pushcart. The savings on a tugger cart would be even more impressive.
While saving money is incentive enough, the ultimate benefit of Flexpipe’s steel tube and joints is the flexibility, scalability, and customization it offers companies. The ability to customize a tugger cart to a company’s specific requirements is invaluable. This is largely why the steel tube and joint system is so highly regarded in lean manufacturing environments. That customization would be next to impossible with “me-too” welded cart providers. A customized cart from these vendors would include high non-recurring engineering (NRE) design charges and take months for delivery. Instead, a Flexpipe tugger cart can be assembled within several hours.
How does Flexpipe promote ease of customization and scalability ?
Flexpipe doesn’t just sell the materials and consumables for modular and scalable material handling structures. The company goes a step further by providing an all-encompassing lean solution. What does that mean?
The learning section of Flexpipe’s website is entirely devoted to helping customers every step of the way. The dedicated and committed Flexpipe team offers a free 45-minute Web Training session with a Flexpipe expert instructor to help you understand how to assemble and use the Flexpipe solution.
In addition, Flexpipe offers its customers the Lean maker Academy, a free online Modular System Certified Expert certificate training session. This 8-lesson training program provides everything you’ll need to make customized lean Flexpipe structures.
Flexpipe also offers a free 2-day training program at the Flexpipe facility in Farnham, Quebec, and a 2-day onsite training program at a customer’s facility. Combined with Flexpipe’s design and fabrication services, these extras mean you’ll never be left alone wondering how to assemble a Flexpipe tugger cart.
Examples of Tugger Carts






Flexpipe Tugger Cart Plans

HEAVY-DUTY TRANSPORT CART
Download this plan
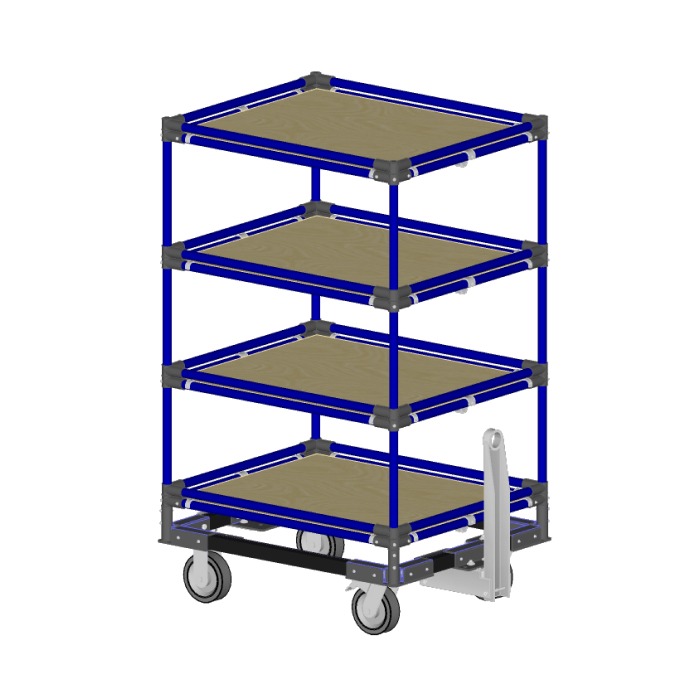
TUGGED CART
Download this plan
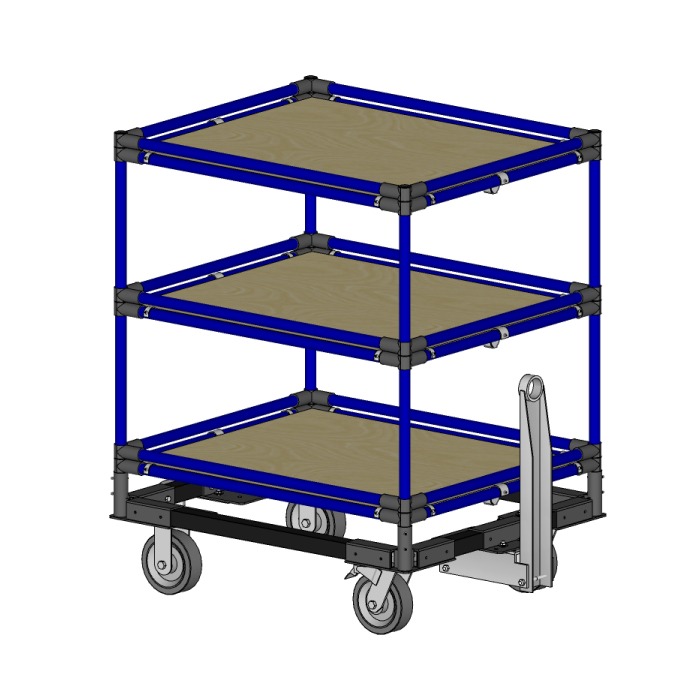
TRANSPORT TUGGER CART
Download this plan

PANEL CART
Download this plan
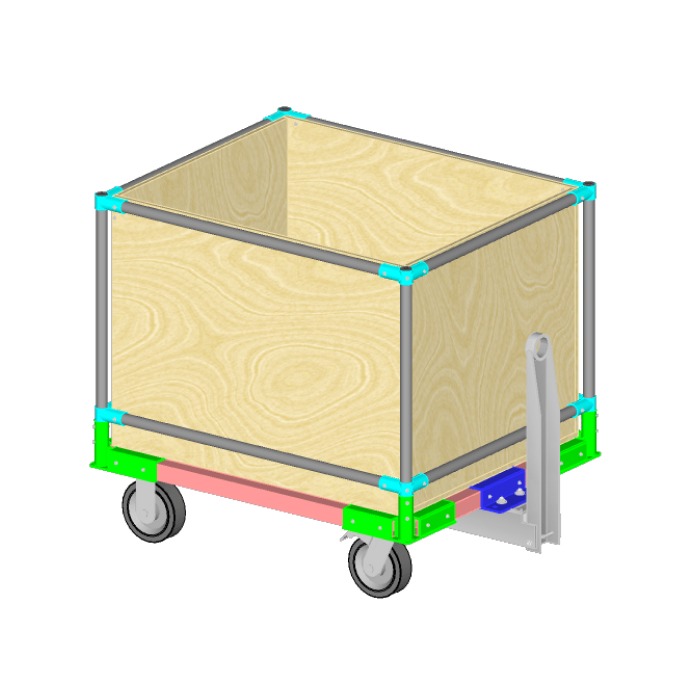
TRANSPORT CART TUGGER
Download this plan

CART PDC
Download this plan
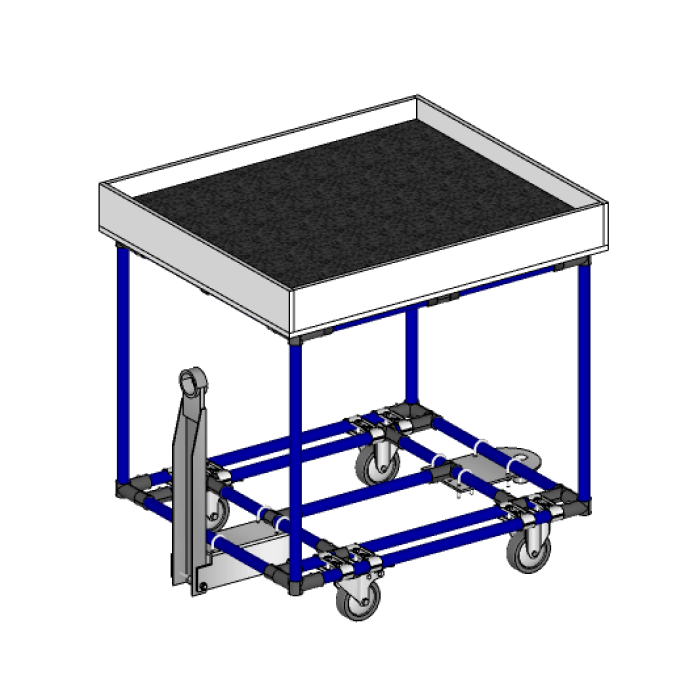
TRANSPORT CART
Download this plan

PLANE PIECES CART
Download this plan
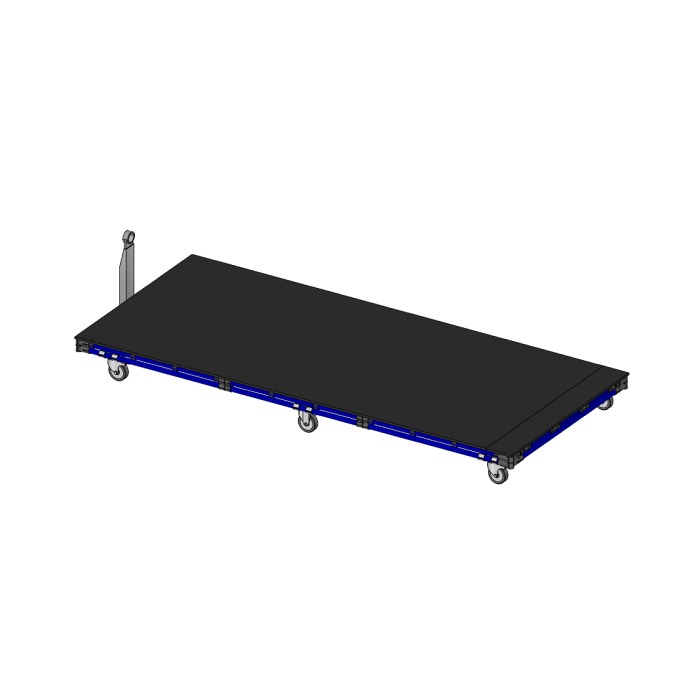
LOW CART
Download this plan
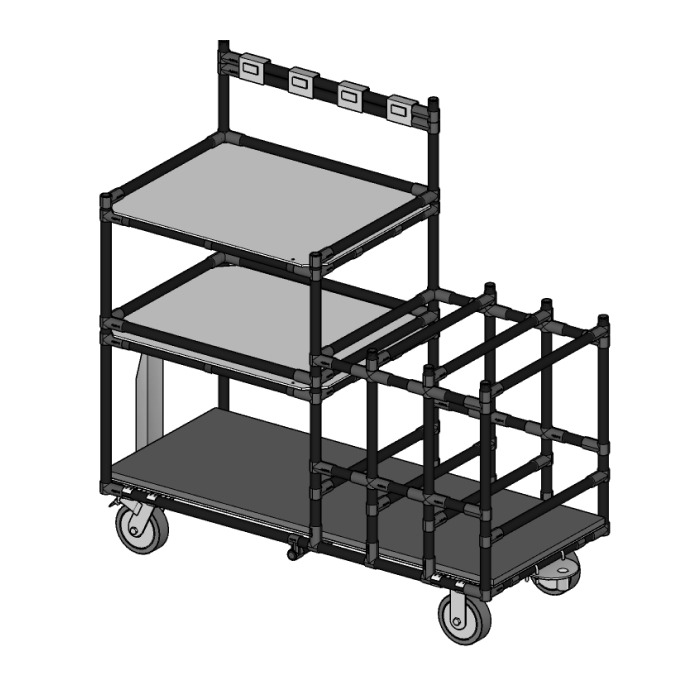
KIT CART
Download this plan
Maintenance and Longevity
Building tugger carts with Flexpipe steel tubes and joints must always coincide with some essential best practices. These are explained in detail below.
How do I maintain and service my tugger cart for prolonged use?
The first step is properly accounting for the weight your structure can support. Exceeding this weight, knowingly or unknowingly, will undo stress on the steel tubes and lead to deformation, bending, or buckling.
Flexpipe’s steel tubes are high-quality, durable, high-strength cold rolled carbon steel. The infusion of carbon and the heat treatment process the steel goes through increases its strength, hardness, durability, and other mechanical properties.
The second step is to periodically inspect the tugger cart as part of your regular preventative maintenance schedule. Given that these carts move across high-traffic areas in industrial manufacturing locations, it’s not uncommon for them to get dinged or scratched. While the polyethylene coating on the pipes is scratch-resistant, inspecting the carts to ensure everything is in good working order is still important.
Manufacturing environments are constantly evolving and never static or stationary. This means you need a material handling solution to adjust to that changing environment. With Flexpipe, you can easily adjust, improve, repair, or refurbish any existing tugger cart. This can be done at a fraction of the costs of conventional welded tugger carts.
To learn more about how Flexpipe’s solutions can help your company with your tugger cart requirements, contact us now.