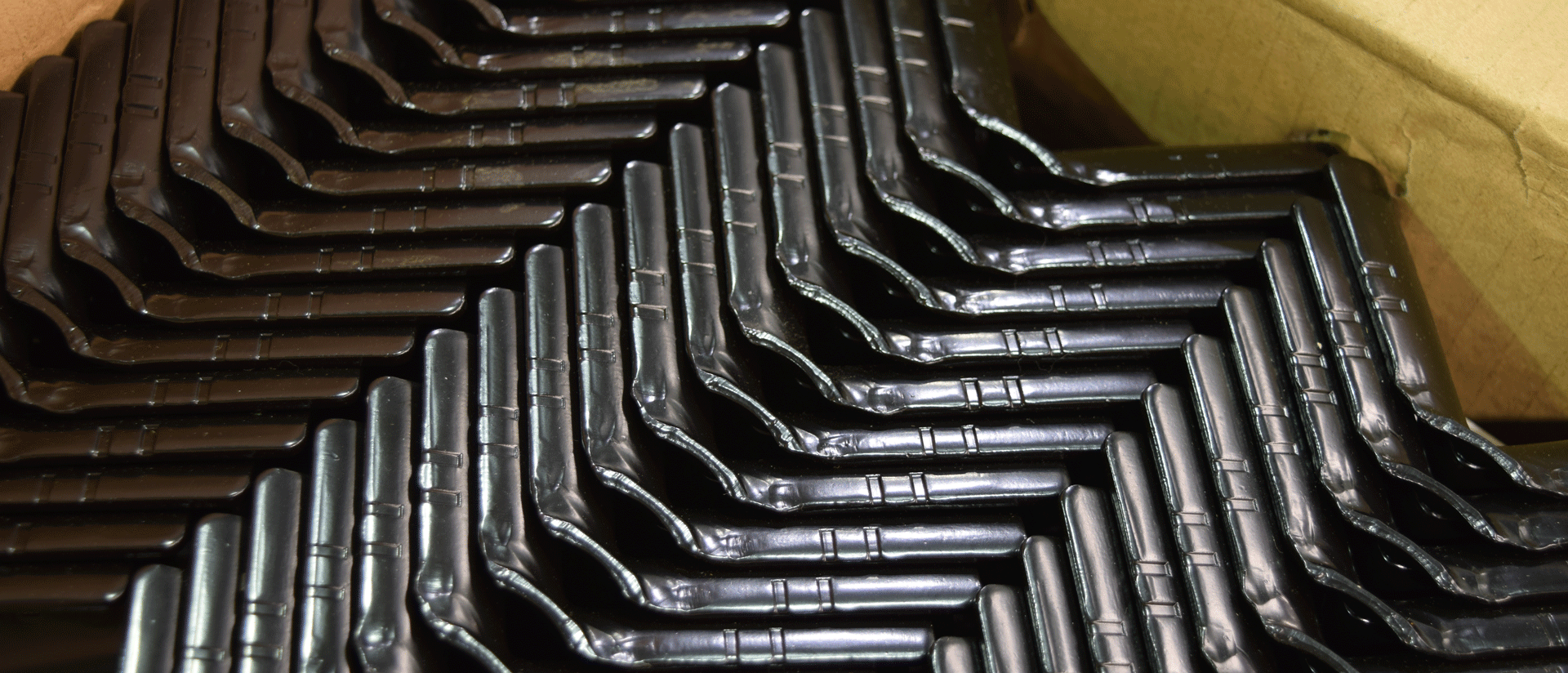
Technical Data
HOW DO WE APPLY E-COATING ON FLEXPIPE PARTS AND WHAT IS E-COATING?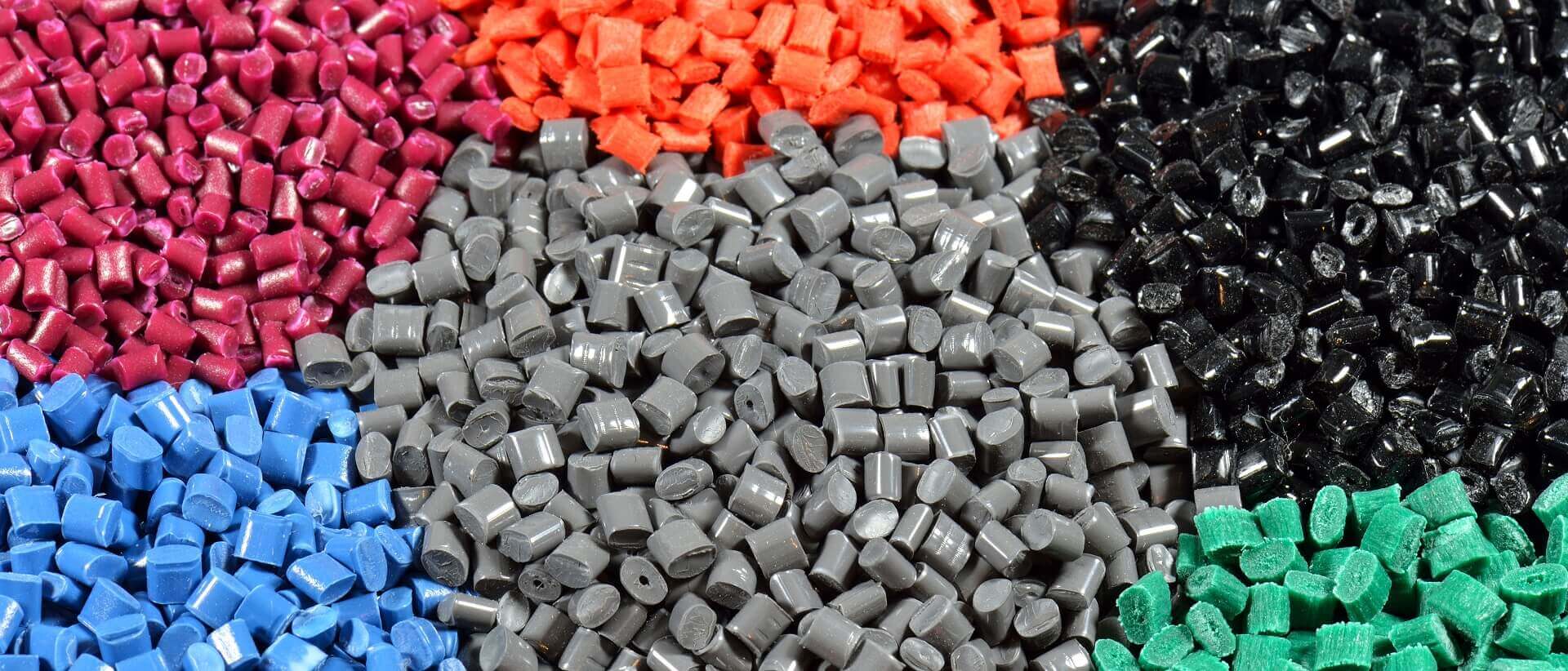
Technical Data
PLASTIC COATING COMPARISON (PE VS. ABS VS. PVC VS. PP)
Technical Data
HOW QUALITY CONTROL IS CONDUCTED ON STAMPING PRODUCTIONThere’s one essential fact that we should begin with: a component’s desaturation will not affect the structural capacity of your structure. Now, is pipe color important for color coding in your business? Do you plan on moving structures outside? If so, then you should be aware that specific Flexpipe colors have better UV resistance than others.
We sent out some Flexpipe tubes and joints to Micom Laboratories to test out the resistance of their coatings to 1000 hours of UV exposition. The test was done in a Weather-Ometer – device measuring controlled ventilation under the influence of light, oxidation, and moisture – with the following conditions: ASTM D2565 cycle 1. Check out the results below to see the Flexpipe parts that have the best resistance to UV. Also, you’ll learn about specific situations where you want to be extra careful when choosing a color.
WARNING! The colors you’re about to see aren’t an exact match of those on Flexpipe pipes and joints. They were selected from images sent to us by Micom Laboratories in the same conditions as those mentioned previously. The purpose of these images is to show you the change in color rather than the colors themselves.
Both the black and nickel-plated joints we got back from the test showed no apparent change in color, which is why there is no image provided. It’s worth mentioning, though, that the black coating joints did lose some of their glossy finish. Since we performed these tests, we have changed our nickel coating for chrome. Since the chrome plating process is the same as the previous nickel plating, only with an additional chromium-plating step, we can estimate that the result is very similar.
As you can see, the blue pipe color changed slightly during the test. We consider the blue pipes to have good resistance to UV. Furthermore, an experiment with the blue pipe outside Flexpipe’s facility demonstrated no more significant change than what is shown below after multiple years of exposure to outdoor elements.
Black pipes are probably one of the most UV resistant parts of the Flexpipe system. We consider these pipes to be highly resistant to UV exposure.
A small difference can be observed on gray pipes after UV exposition. However, the difference is little enough to consider Flexpipe’s gray to have good resistance to UV rays.
Since these colors were selected from a photo taken without perfect light conditions, the white pipes look a little gray. As you can expect, this shade is desaturated as an absolute white would be the absence of color. In this case, we can see a slight desaturation when exposing the pipes to UV rays. Therefore, we consider white pipes to have good UV resistance.
Yellow pipes have shown little to no change at all during the Weather-Ometer test. We consider the yellow pipe to be highly resistant to UV rays.
You’ll want to avoid using orange pipes if your structure will be used outdoors and if the stability of its color matters. We were surprised to see how close the orange matched the yellow pipe’s tone after the test. We consider this color to have a low resistance to UV exposure.
The red pipes are by far the color that underwent the most drastic change. We recommend avoiding this color when creating structures that are meant to be used outside or located near large windows or doors. As a result, we consider the red pipes to have a meager resistance to UV exposure.
Flexpipe accessories and decking showed no significant change after being exposed to UV rays.
We hope that this information will prove to be helpful in your decision process. If you would like more information about Flexpipe parts’ UV resistance, contact us to get the complete Micom Laboratories to report with all the data.