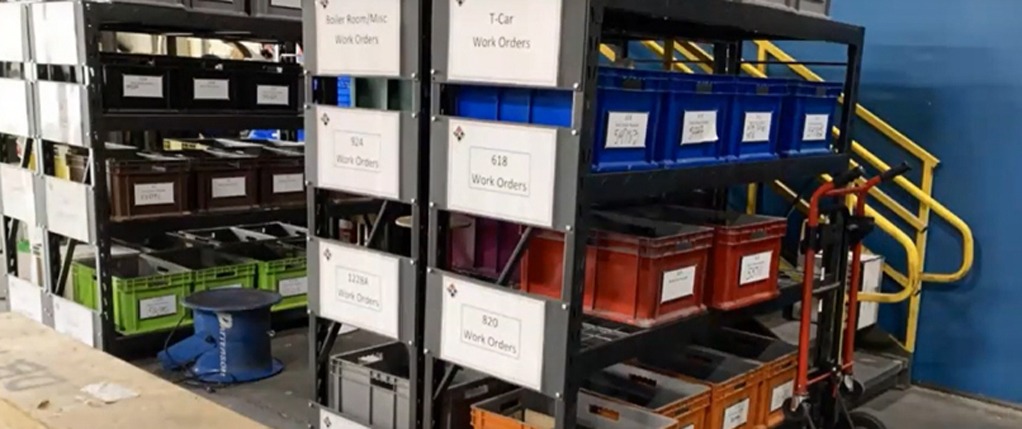
Post
LEAN VISUAL MANAGEMENT FOR MACHINES, MAINTENANCE AND OPERATIONS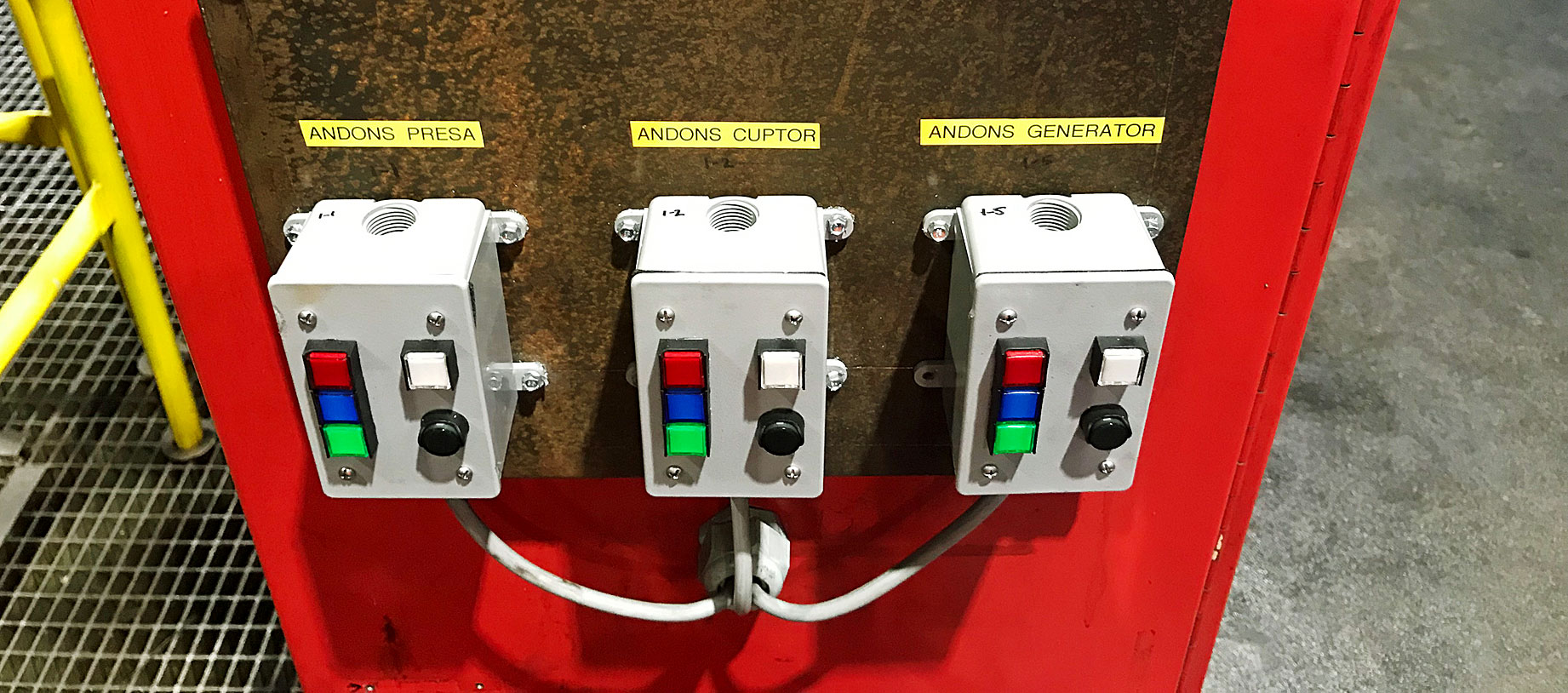
Post
HOW THE ANDON SYSTEM CAN HELP PRODUCTION FLOW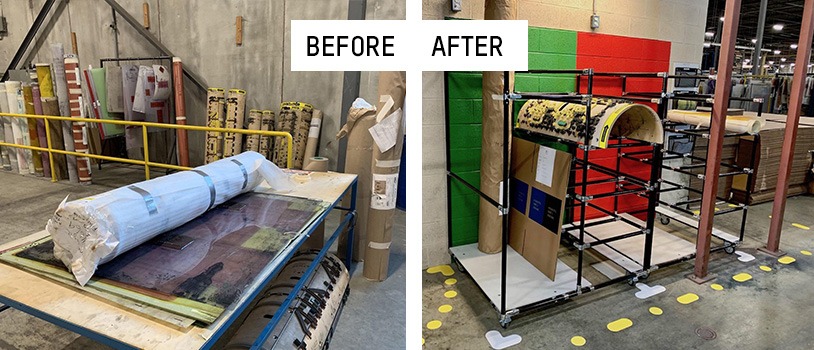
Case Study
DISCOVER THE BENEFITS OF LEAN MANUFACTURING IN THE CORRUGATED AND PACKAGING INDUSTRIESValue stream mapping involves creating a detailed visualization of all the steps in your manufacturing process, allowing you to identify problems and potential improvements. It’s one of the fundamental tools of lean management, as TXM’s Normand Sawyer explains in this video.
The term “value stream” refers to the series of steps an organization takes between the initial order of raw materials and the delivery of the finished product to the customer. This includes both value-added actions (steps that contribute to the product’s value for the customer) and non-value-added actions (steps that bring no value to the customer, such as moving equipment or waiting between tasks).
A value stream map is a detailed flow chart representing every step in your manufacturing process. It shows you how materials and information progress through your workspace and indicates all inventory points and processing and lead times, helping you spot bottlenecks and wasteful activities.
Value stream mapping actually entails creating two maps: one of your value stream as it currently operates, and another representing your ideal future process, with current problems solved.
Creating a detailed map of your workflow’s current state is a crucial first step. To find effective solutions, you’ll need a thorough understanding of your existing process.
The essential function of a value stream map is to help you visualize the following aspects of your production process:
Representing these things visually makes it easier to spot strengths and weaknesses across your entire workflow—not just in specific areas. For instance, you might notice that operators spend the first five minutes of their shift awaiting instructions from a supervisor. You can then figure out how to eliminate that wait time, such as by posting instructions at workstations. Or, you might see that parts tend to pile up at one workstation, causing delays further down the production chain. You can then come up with a strategy to eliminate the bottleneck.
If you’re planning to adopt the principles of continuous improvement in your workplace, it’s best to start with value stream mapping. You’ll find out exactly what needs to be fixed and be better equipped to choose the right solutions.
First, choose which process you wish to map. If you manufacture several types of products, they likely go through different processes and will each require their own map.
Once you’ve decided which value stream to focus on, put together a team. Value stream mapping is not a solo endeavour—to get an accurate picture of your current workflow, you’ll need to consult the people who are performing the tasks.
Next, begin gathering data. To ensure accuracy, it’s essential to observe operators at work and ask questions rather than relying on reports from managers. The goal is to get realistic information about each step, such as turnaround time, quality level, and changeover time, as well as details about any setbacks the operators face. Let people know your goal is to find ways to improve the overall workflow, not to criticize their performance; they’ll be more honest about the challenges they face and may volunteer useful information.
Now it’s time to map out your data on a whiteboard. The finished value stream map should resemble a flow chart, with detailed notes about every step of the workflow. Analyze your map and identify problems that need to be addressed.
Consider what changes could be made to solve these issues. You can start by asking yourself what the customer needs, then work backwards: what should the finished product look like? What steps are involved in creating that product? Can any steps be combined or eliminated? The answers to these questions will allow you to map your ideal workflow and determine how to achieve it.
Above all, remember that value stream mapping is a diagnostic tool, enabling you to assess the health of your production chain as a whole. Once you’ve completed a value stream map, you can implement specific lean manufacturing techniques, such as an Andon system or visual management, to create a more robust workflow.
TXM is a leading international lean consulting company with projects in more than 15 countries. Established in 2004, the company’s scope has since expanded beyond the manufacturing industry, with a team of diverse lean professionals lending their expertise to the resources, services, agriculture, supply chain, and distribution sectors.
____________________________________________________________________________
Flexpipe Modular industrial pipe racking system can help you with implementing continuous improvement principles. Your team’s creativity can result in a 10% increase in productivity per year. It has been a proven system for more than 50 years now.
See how the modular system improve operational efficiency while saving time in manufacturing processes at Waterax.