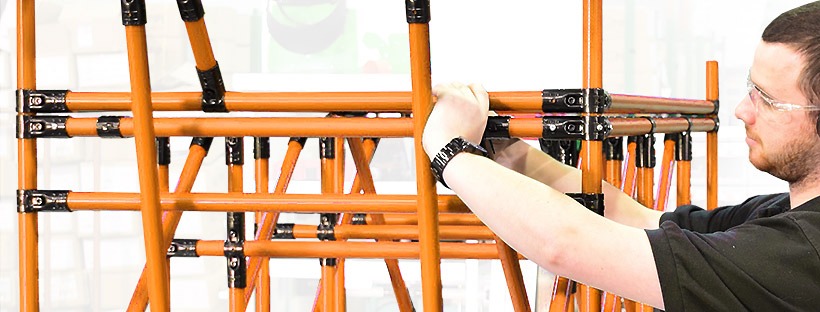
Post
6 ESSENTIAL PERSONALITY TRAITS OF THE IDEAL ASSEMBLER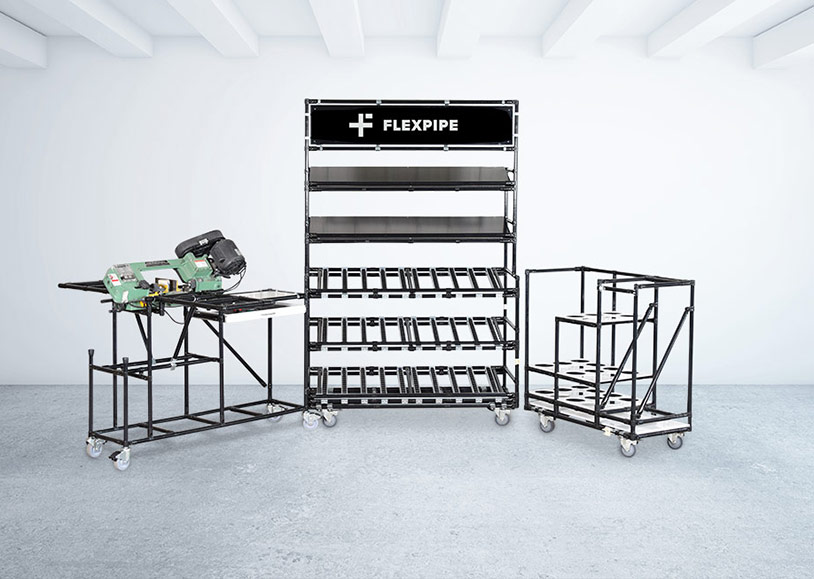
Post
WHY YOUR WORKPLACE REQUIRES A FLEXPIPE CRIB
Page
TRAINING AT FLEXPIPEEstablished in 2006 in Montreal (Canada), Lumenpulse designs, develops, builds, and sells LED lighting solutions intended for commercial, institutional, and urban environments. The exponential growth of the company’s activities brought about the need to move its facilities. As such, a complete overhaul of the production area’s layout was needed as well as the addition of more production lines.
Having used various material handling systems in the past, Lumenpulse opted this time to implement a modular tube and joint system in the new plant. Read on to discover the advantages of a tube and joint system compared to other types of modular material handling systems.
Estimated reading time: 4 minutes
Relocating the plant to a facility built from the ground up provided an opportunity to examine the company’s needs regarding its new facilities carefully. Given that the production line’s layout had been rigorously tested before the impending move, Lumenpulse management was able to design the new plant based on the space required for ergonomic and efficient manufacturing. The result: 80 000 sq. Ft. area dedicated to the assembly of lighting products and by-products.
Having gone from 50 employees in 2011 to over 350 employees in March 2017, the company now has 185 operators who are split mainly into two work shifts (day, evening). Lumenpulse has more than 700 employees internationally, and that the headquarters’ parent company is not the only manufacturing facility.
Initially, workstations consisted of wooden tables and roller conveyors on which flowed trays containing parts for production. However, given the challenge to establish the coming weeks’ output, it became increasingly difficult to tailor the workstations according to the parts to be assembled.
Now, a linear production system divided into four identical workstations allows lighting fixtures up to 8 feet long to be built.
After having evaluated different types of material handling equipment, Lumenpulse equipped the majority of its workstations with a modular tube and joint connector system. This system allowed the staff to design workstations according to the products being manufactured, thus leading to greater optimization of the production line.
The biggest advantage is that we can reuse the parts!
Jonathan Barriault – Lumenpulse Operational Excellence Manager
As a result, when the current structure no longer corresponds to production needs, it can easily be disassembled to build another one. Contrary to other handling systems, the tube and joint connector system offer significant design flexibility, all the while eliminating waste at a lesser cost.
In the beginning, three people were designated and trained to design and build modular structures, but it became increasingly difficult to give them a full-time work schedule each week.
Following the company’s expansion in 2018 and strong sales growth, Lumenpulse had to review the layout of its production lines to introduce new product lines.
“Now, we try to make sure that it’s our group of industrial engineers who design and assemble the structures. These people possess mechanical knowledge, which makes the task easier,” declared Jonathan. “Even though it’s never quite the same people who are the designated assemblers, we’ve never noticed any resistance to change. Also, since the lean manufacturing workstations are tailored to each employee, it’s them who ask for the changes!”
Over the years, Lumenpulse has tested out various material handling systems, i.e., aluminum extrusion, welded steel, tube, and joint connectors, as well as industrial products in catalogs, etc.
Benefits:
The tube and joint modular system provide greater flexibility when it comes to the possibilities of multiple configurations. Given that the parts can be reused, the system generates more savings. Furthermore, when employees are involved in the design process, it fosters a sense of belonging both to the company and its endeavors.
Drawbacks:
Because the production lines’ workstations were designed according to the product currently being built, a production line occasionally had to stop when unneeded.
For comparative purposes, an aluminum extrusion system can be reused—but at a much higher cost. As for a welded steel structure, it becomes cumbersome once loaded with parts, which makes it very difficult to move around. Finally, industrial products ordered by catalog generally cannot be reused.
To conclude, a tube and joint connector modular system can be very versatile when faced with varying production volumes. Furthermore, it offers significant profitability as the parts can be reused endlessly.