
Page
WHY FLEXPIPE
Page
CASE STUDIES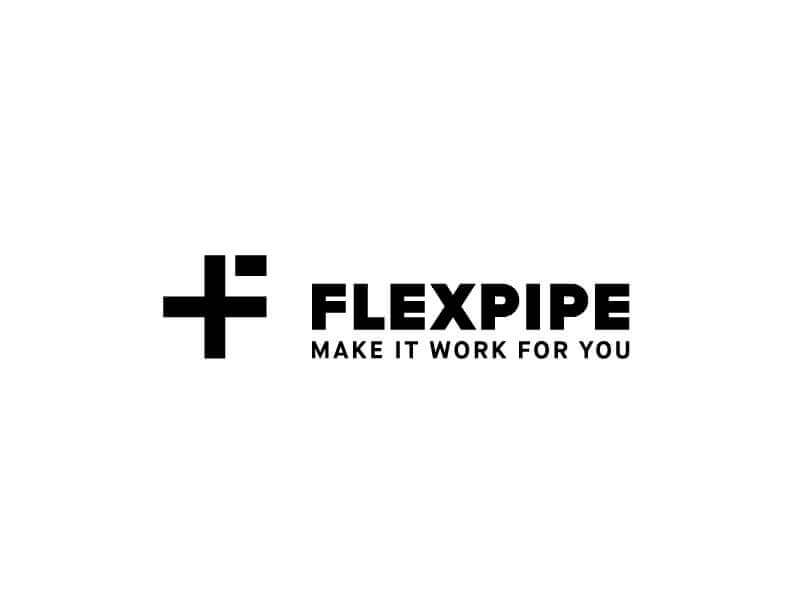
Page
ON-SITE TRAININGModular material handling systems will help you with implementing lean manufacturing and continuous improvement workflows. Your team’s creativity will help reduce the 8 wastes and can result in a 10% increase in productivity per year. Lean manufacturing has been a proven system for more than 50 years now. Here are the 8 reasons why you should consider using a material handling system.
The modular systems allow you to disassemble and reuse the pipes and joints over and over. This reduces the cost of equipment when processes or products change. It also allows the structure to be evolved. For example, a lean manufacturing workstation can be adapted and improved easily and quickly according to employees suggestions. This results in a greater employee satisfaction.
Due to millions of different products in the market, it is important to have many different structure types and designs to accommodate every company’s needs. Modular systems are ideal for creating custom and ergonomic structures according to your exact needs. You no longer need to use a product that does not fit the job well or takes up too much floor space.
Modular handling systems are a perfect tool to help leaders implement lean manufacturing in your business. Because they are adaptive and easy to use, modular tubes and joints help to continuously reduce the 8 wastes associated with lean manufacturing. This tool can help to implement kitting, 5S, points-of–use, one-piece flows, visual management structures, and much more.
Before 2010, Flexpipe was a made-to-order welding factory that made steel racks, carts, and tugger carts. We know first-hand that modular systems can help save 30% to 50% on the equipment budget. This allows a company to do more with the same budget while keeping a small inventory of pipes and joints for prototypes and quick fixes.
According to a Flexpipe survey in March 2016, 74% of Flexpipe users said that the modular systems have helped to improve the factory image. The product helps to standardize working structures with a professional and tailored look that will increase client and supplier confidence when touring a plant.
Because the Flexpipe system is a simple system requiring very minimal tool sets, all employees can create and build one without having to familiarize themselves with new tools. They can participate in designing structures by pitching innovative ideas during a Kaizen, They can also build their stations at the Moonshine Shop. In any case, they should be continuously asked how to improve the structures they are working with.
Even if Flexpipe is made from steel tubing, it is 20% to 30% lighter than a standard steel structure. This is ideal for loading and ergonomic constraints for pushcarts or flow racks. Also, well-designed structures will minimize space on your production floor and maximize piping to reduce hideouts and weight. A linear system means better visibility and more sustainable 5S programming.
From production floors to conference rooms to maintenance departments to packaging lines, modular systems can be introduced in various situations and departments. It is one simple hardware solution, which avoids multiple purchase requests. Using a modular system reduces the need to look around for specialized products and suppliers, saving time for both the person making the request and buyer. Different colors and finishes give different looks to any structure.
We have compared services, parts, technical specs, and prices from our most popular competitor.
Consult the complete Creform alternative comparative study