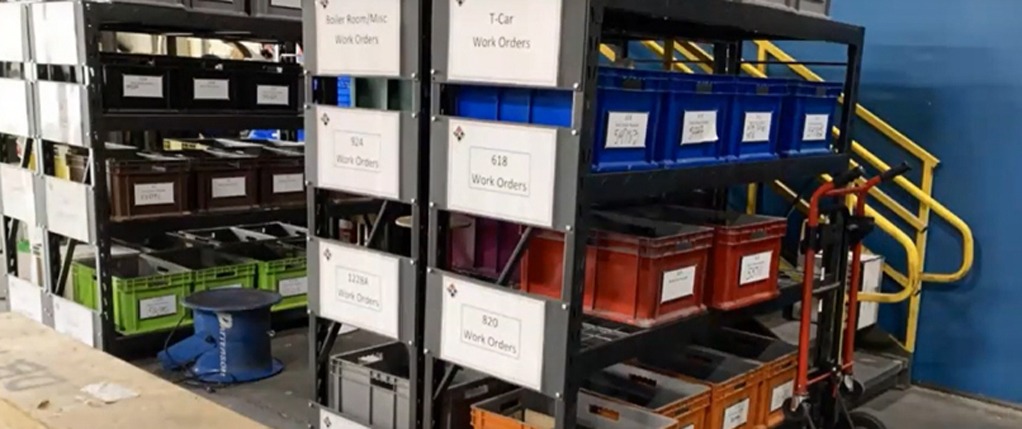
Article
GESTION VISUELLE LEAN POUR MACHINE, MAINTENANCE ET OPéRATIONS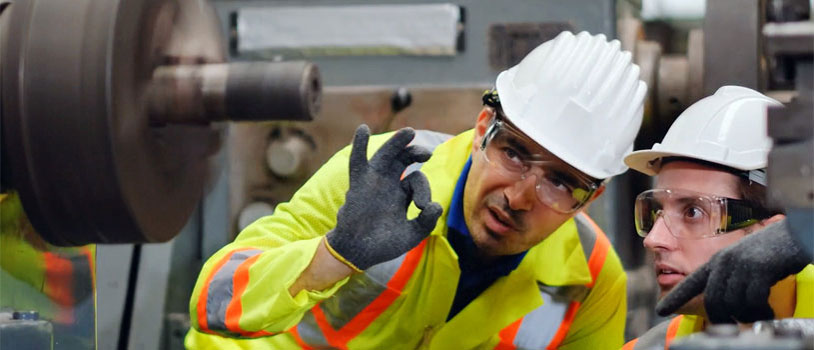
Article
CONSEILS POUR UN éVéNEMENT KAIZEN RéUSSI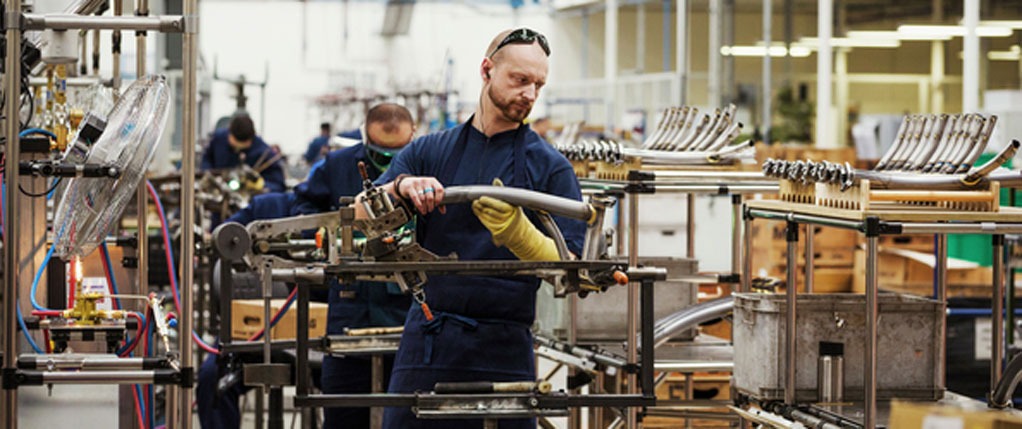
Article
10 TRUCS POUR RéDUIRE LA RéSISTANCE AU CHANGEMENTDéfini comme un des huit types de gaspillage identifiés par la méthodologie lean, le gaspillage de mouvements représente toute action d’un processus de production qui ne procure pas de valeur ajoutée au consommateur. Ce concept comprend des mouvements comme marcher, se pencher, soulever des objets ou s’étirer, qui ralentissent la production et qui compliquent la tâche des opérateurs.
Comme l’explique Martin Boersema de Shoplogix dans cette vidéo, les mouvements inutiles tendent à être la forme de gaspillage la plus courante en milieu de travail. Toutefois, il s’agit aussi d’un aspect relativement facile à améliorer grâce à des initiatives d’amélioration continue, comme les événements kaizen.
Pour cibler le gaspillage de mouvements, observez attentivement le processus de travail et notez tous les gestes qui semblent ralentir les opérations. Un opérateur traverse peut-être toute l’usine pour consulter une liste de directives ou manipule peut-être une même composante pendant plusieurs secondes.
Posez aussi des questions pour découvrir la cause de ces gestes inutiles afin d’être en mesure de cerner des pistes de solutions. La tenue d’une étude de temps peut aussi être utile afin de cibler exactement le temps qu’il faut pour exécuter chacune des tâches du processus. Si vous remarquez une fluctuation dans le temps requis pour réaliser une action précise (par exemple, parfois un total de 30 secondes et d’autres fois un total de 60 secondes) le gaspillage de mouvements est probablement à blâmer.
Les types de gestes inutiles varient en fonction du processus de production. Par exemple, dans une zone de moulage par injection, un opérateur pourrait avoir de la difficulté à suivre la cadence de la machine s’il doit s’éloigner et faire plusieurs pas pour accéder aux composantes dont il a besoin.
De plus, même si l’opérateur réussit à suivre la cadence de la machine, les secondes passées à se déplacer seraient tout de même mieux investies dans une tâche qui ajoute une valeur ajoutée, comme une inspection par exemple.
Dans une zone d’assemblage où le travail est exécuté manuellement, l’efficacité du processus dépend de la facilité avec laquelle l’opérateur peut réaliser chaque tâche. Même les plus petits pépins peuvent ralentir le travail. Par exemple, un opérateur forcé de manier longuement une composante pour qu’elle s’imbrique ou forcé de faire pivoter son corps pour atteindre les outils dont il a besoin.
Une des causes principales du gaspillage de mouvements est le temps passé à chercher ce dont on a besoin. Si l’organisation de l’espace de travail n’est pas adéquate, les employés devront se déplacer pour accéder aux composantes, à l’information ou aux outils manquants.
Souvent, le gaspillage de mouvements peut être réduit en rendant l’équipement requis plus facilement accessible aux opérateurs. Vous pourriez par exemple remplacer une grande armoire par un chariot à roulette qui peut être approché de l’espace de travail ou opter pour plusieurs petits bacs de rangement plutôt qu’un grand bac pour éviter que les employés doivent fouiller pour trouver la composante dont ils ont besoin.
De plus, pour réduire le temps perdu à chercher les outils nécessaires, il est important d’assurer que tout l’équipement pertinent est rangé au bon endroit et qu’il est correctement identifié. Pour ce faire, un système de communication efficace doit aussi être mis en œuvre. La gestion visuelle est une technique de l’approche lean qui peut faciliter cette amélioration.
D’autres types d’embouteillages au niveau de la production pourraient nécessiter leur propre solution ciblée. Si un opérateur peine à imbriquer une composante, la base pourrait devoir être redessinée pour assurer un mouvement plus fluide. Autrement, si un opérateur doit insérer manuellement une composante à une extrémité d’une machine pour la retirer à l’autre extrémité, il pourrait être pertinent d’étudier la possibilité d’automatiser un de ces gestes.
Les employés qui sont forcés de faire plusieurs gestes inutiles en exécutant une tâche sont souvent confrontés à de la fatigue, des courbatures, et parfois même des blessures. Certaines personnes pourraient sous-estimer l’ampleur de l’impact qu’ont les mouvements superflus sur le bien-être des employés, pensant qu’une seconde ou deux passées à se pencher ou à soulever une charge n’auront pas vraiment d’effet.
Toutefois, lorsque des solutions de réduction du gaspillage de mouvements sont implantées, la plupart des employés remarquent une hausse d’énergie, surtout à la fin de la semaine de travail.
La formation des employés quant à la réduction des gestes inutiles et quant à l’importance du travail d’équipe pour la résolution de problèmes, représente un aspect essentiel de l’amélioration continue. Par ailleurs, il est tout aussi essentiel d’éduquer les responsables au sujet de ces enjeux.
Ultimement, ils seront à la tête de l’instauration de ces améliorations qui exerceront une influence positive sur la qualité de vie des employés.
Grâce à sa plateforme manufacturière intelligente à la fine pointe de l’industrie, Shoplogix aide les acteurs du secteur manufacturier à réduire leurs coûts d’exploitation et à maximiser leur rendement en révélant des occasions d’améliorations de la productivité. Basée à Oakville en Ontario, l’entreprise fait sa marque à l’international grâce à ses bureaux aux quatre coins du monde.