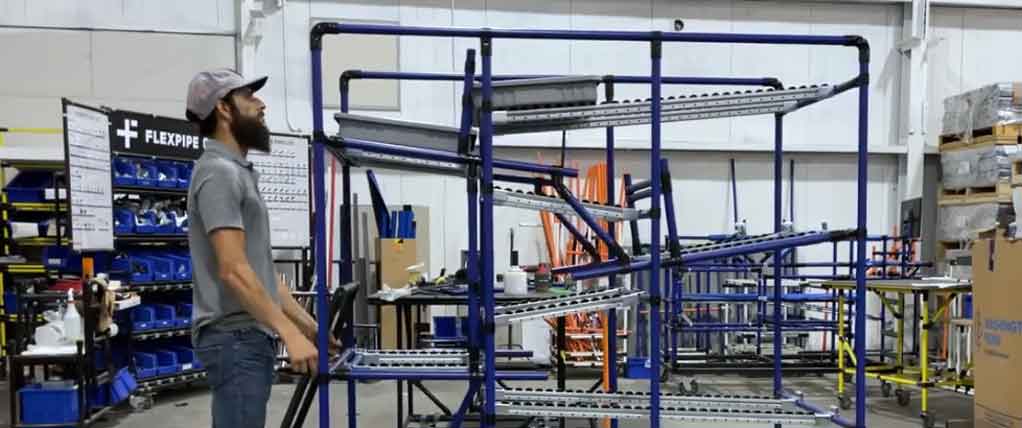
Article
QUATRE AVANTAGES DU KARAKURI DANS LES OPÉRATIONS LEAN
Étude de cas
UN GRAND FABRICANT DE BOîTES EN CARTON ONDULé PASSE EN «MODE LEAN » AVEC FLEXPIPE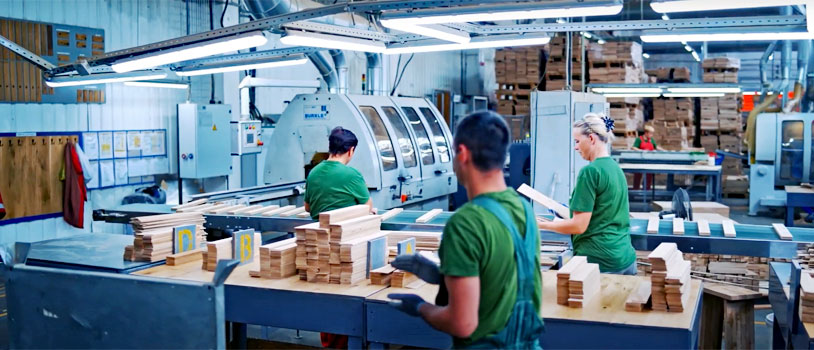
Article
CIRCULAR MANUFACTURING : LES CODES DE LA PRODUCTION CIRCULAIREJerry Collins, ingénieur mécanique riche de 28 années d’expérience dans l’industrie automobile, traite l’étape de pré-production comme la première étape critique pour gérer coûts éventuels de production. C’est au cours de cette étape que Jerry utilise des systèmes tubulaires modulaires pour aménager son espace de production et concevoir ses systèmes de manutention. Cette méthode réduit les coûts et facilite la modification des systèmes lorsque nécessaire, une fois la production à grande échelle lancée.
Découvrez comment toutes les entreprises, peu importe leur secteur, peuvent utiliser les systèmes de tubes et de connecteurs au stade de la pré-production pour mieux gérer leurs coûts.
La fabrication Lean trouve ses racines dans la célèbre chaîne de montage du modèle T d’Henry Ford et dans le système de production Toyota (TPS) du début du XXe siècle. Parfois appelée « production Lean » ou « méthode juste-à-temps », la fabrication Lean se concentre sur l’augmentation du débit de production, tout en contrôlant les coûts et en minimisant les déchets.
Avec la fabrication Lean, les entreprises peuvent augmenter le débit de production, sans sacrifier leur trésorerie ni acheter une quantité excessive de stocks. Malheureusement, malgré le fait qu’un grand nombre de compagnies utilise certains concepts Lean, plusieurs n’implantent jamais l’entièreté de ses méthodes.
Au lieu d’utiliser les principes de fabrication Lean pendant la phase de pré-production, plusieurs entreprises n’adoptent ces concepts qu’une fois la production démarrée. Malheureusement, cela les place dans une position où des changements imprévus dans la conception des produits les obligent à effectuer des ajustements aléatoires et extrêmement coûteux. Jerry a quant à lui adopté une approche totalement différente.
Jerry et son équipe ont utilisé des solutions conçues en tubes modulaires pour créer une maquette de chaîne de montage d’essieux avant et arrière pour General Motors. Comme l’a déclaré Jerry, «bien avant d’acheter l’équipement, nous avons créé une installation complète avec des structures modulaires en tubes et avons déterminé très tôt la façon dont nos systèmes de manutention seraient organisés«. Cette planification a donc mené à une présentation visuelle des machines et des équipements dans l’atelier à l’aide de tubes et de connecteurs.
Ils ont également utilisé le système modulaire pour créer des chariots afin de tester les temps de transit entre les cellules de travail, à l’affût d’éventuelles obstructions. Ils ont ensuite créé des structures temporaires afin de simuler la façon dont les futurs systèmes de manutention seraient positionnés à côté des cellules de travail, des équipements et des machines.
Jerry et son équipe d’ingénieurs ont choisi les solutions de tubes modulaires lors de la phase de pré-production en raison de la facilité à apporter des modifications simples aux structures créées. Certaines des modifications qu’ils ont apportées à leur maquette n’ont pris que quelques minutes, ce qui est totalement impossible à réaliser avec des systèmes de manutention fixes. Comme l’a déclaré Jerry, «les entreprises doivent planifier leurs systèmes de manutention dès le début afin de pouvoir maintenir et améliorer leurs marges bénéficiaires plus tard«.
En fin de compte, les solutions de tubes et de connecteurs ont remplacé toutes leurs grandes structures de manutention fixe. Selon Jerry, pour apporter un seul ajustement à leurs anciennes structures de manutention, ils devaient envoyer leurs racks à «un sous-traitant pour le soudage et les ajustements, ce qui pouvait prendre des semaines et des mois. Si vous avez plutôt un produit comme Flexpipe, cela peut être fait en un après-midi.’’
Selon Jerry, l’adoption de systèmes modulaires en tubes pendant la phase de pré-production a permis à son équipe d’être déjà à l’aise avec la solution, une fois la production commencée. Alors, quels sont les avantages inhérents à l’utilisation d’un système tubulaire modulaire pendant la phase de pré-production ?
L’adoption de concepts Lean dans la phase de pré-production à l’aide de tubes et de connecteurs présente trois avantages principaux. Tout d’abord, cela permet de regrouper les coûts associés à l’aménagement de l’ensemble du plateau de production pour les équipements et les machines, totalisant les coûts des structures debout, des établis, des étagères, des chariots, des racks à gravité, des planches, etc.
Cela fournit donc aux entreprises un portrait complet de leurs dépenses. Elles peuvent également décider de la superficie réelle dont elles ont besoin pour la fabrication. Elles peuvent ainsi éviter les coûts supplémentaires liés à la location/l’achat d’un espace de production trop important ou, à l’inverse, éviter les coûts et les retards liés au manque d’espace.
Deuxièmement, l’utilisation de solutions en tubes modulaires au stade de pré-production permet de simplifier le flux de travail. Les entreprises ont beaucoup plus de facilité à choisir les solutions tubulaires modulaires nécessaires pour toutes leurs cellules de travail en forme de T, de U et de type S ou Z. Cela leur permet de maximiser les temps de transit entre les cellules de travail, les équipements, les machines et les autres structures érigées. Cela les aide également à choisir les emplacements idéaux pour l’inventaire et le stockage des pièces.
Troisièmement, en adoptant les systèmes tubulaires au stade de pré-production, les employés sont plus en mesure d’apporter des modifications aux structures et aux systèmes de manutention, une fois la production commencée. Plus besoin d’attendre pour souder ou d’envoyer les racks à des fournisseurs externes pour des modifications qui peuvent prendre des semaines ou des mois. Avec les systèmes de tubes et de connecteurs, les employés peuvent effectuer les modifications eux-mêmes.
Les tubes modulaires sont l’incarnation réelle des concepts Lean. Les modifications aux systèmes de manutention modulaires sont apportées plus rapidement, plus simplement et représentent des coûts beaucoup moins importants par rapport aux structures fixes.
Encore une fois, les entreprises de n’importe quel secteur peuvent appliquer cette approche en utilisant les quatre étapes suivantes.
Les diagrammes spaghetti vous permettent de cartographier votre flux de travail afin d’avoir une présentation visuelle de la façon dont les pièces physiques se déplacent. Vous pourrez visualiser les interactions entre le stockage des pièces, les systèmes de manutention, les cellules de travail, les équipements et les machines. L’objectif est d’établir un processus séquentiel où les pièces se déplacent naturellement et les employés n’ont pas à parcourir de très longues distances pour déplacer ces pièces vers la chaîne suivante du processus.
Définir la taille physique des équipements et des machines permettra de maximiser l’espace disponible sur le plancher. Vous devrez définir les dimensions physiques des équipements et des machines et visualiser comment ils seront disposés dans l’atelier.
Une fois les zones de votre plancher occupées par les machines et l’équipement définies, il devient facile de déterminer le nombre de systèmes de manutention dont vous aurez besoin. Pour vous aider dans la conception de ces systèmes, Flexpipe a créé l’Extension Flexpipe Creator, un logiciel innovant qui vous permet de simplifier vos conceptions.
Votre plancher devrait désormais être simulé avec l’emplacement de l’équipement, des machines, des structures debout, des cellules de travail et des systèmes de manutention. Une dernière étape proactive consiste à simuler les temps de transit entre chacun de ces éléments pour s’assurer qu’il y ait suffisamment d’espace pour que les employés puissent déplacer des pièces et que les distances parcourues ne soient pas trop importantes.
Très présent en Amérique du Nord, Flexpipe est un chef de file de l’industrie des systèmes de tubes et de connecteurs. Reconnu depuis longtemps comme une entreprise innovatrice, Flexpipe met de l’avant des solutions modulaires tubulaires abordables (30 % moins chères), avec une approche orientée client, un service à la clientèle impeccable et un soutien après-vente inégalé.