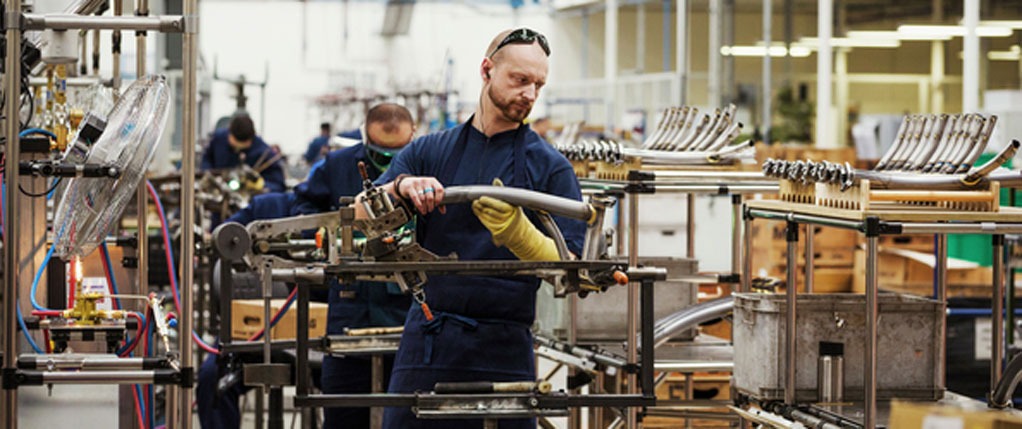
Post
10 TIPS TO REDUCE CHANGE RESISTANCE WHEN INTRODUCING LEAN MANUFACTURING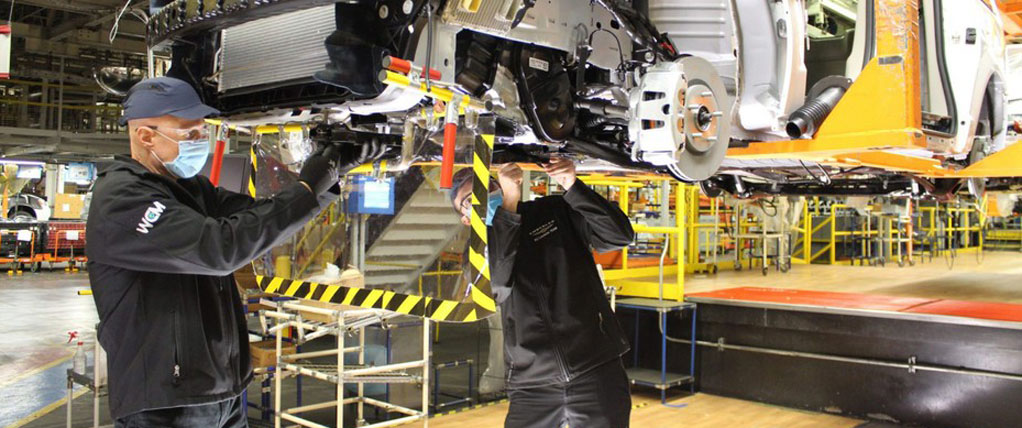
Post
BORROWING LEAN MANUFACTURING CONCEPTS FROM THE AUTOMOTIVE INDUSTRY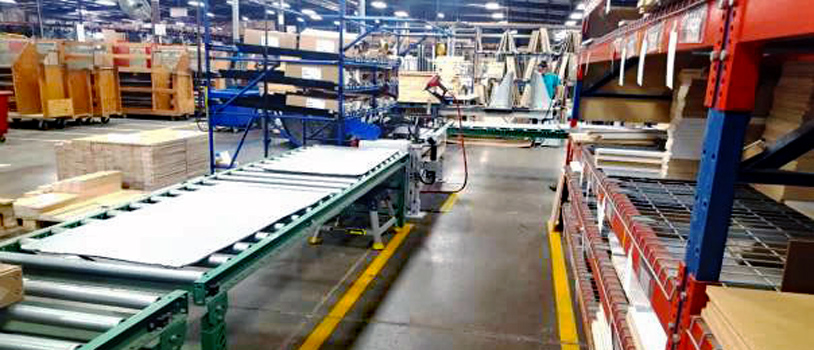
Case Study
HOW KAIZEN INITIATIVES IMPROVED BATCH-TO-BATCH PROCESSES AT AMERICAN WOODMARKImplementing lean is a journey in itself. No company goes from 0 to 60 in record time when implementing lean principles. They learn, get better, learn some more and then improve some more. Each step of that journey is made easier when senior management is entirely on board and, in some cases, driving the lean journey..
Regardless of your industry, some employees may be reluctant to change, while others may embrace it. For those who resist change, it’s often a question of personal comfort; we’ve always done it this way, so why change? However, with consistent training, constant feedback, daily upgrades, and commitment, you will achieve significant lean improvements using Flexpipe.
Flexpipe is a tool, but the employees drive the improvements
Here are just a few examples of lean improvements using Flexpipe products.
Source: MetCabinet About Us
Several cabinet makers using Flexpipe can decrease over-production while dramatically reducing the square footage of their shop floor. This reduction in floor space saves the company money while making it easier to manage materials, quarantine defective products, collect scrap or refuse, and move semi-finished and finished goods between lean work cells.
We often come across Cabinet makers who have fully adopted batch production. Trying to make different types of products simultaneously, along with redundant work processes and poor material flow, often leads to WIP cabinets, drawers, trims, and sides strewn about the shop floor. We see this quite often. The solution to this issue is provided below
This Flexpipe cart in the finishing department is used for cabinet frames, end panels, backs, shelves, etc. Each subcomponent and material is neatly placed in its appropriate slot, making it easy for operators to access a given piece when needed.
Companies invest a lot of money in automating their machinery and equipment. Unfortunately, these same companies often ignore the lean structures and material handling solutions critical to maintaining running equipment. They simply don’t invest enough time, energy, or money to ensure that their material handling structures are optimized.
Even the newest automation falls short if the structures around them aren’t properly organized. Not convinced? Take some time to investigate and measure your cutting machine’s productivity and efficiency. You’re likely to find there is far more downtime than you expected. Very often this is due to inefficient changeovers.
A Flexpipe cart on the Homag Edgebander machine at Superior Cabinet. It applies matching edge tape of various colors to the sides of the melamine to match the finish on the top and bottom.Source: Superior Cabinet.
You will never sustain a lean culture if you don’t engage, train, and spend on your employees. The woodworking industry has so many talented, hard-working, resourceful, and creative people. Unfortunately, there are often underutilized. This unused worker creativity is by far the biggest waste in the industry.
Several companies have highly-skilled and experienced employees who have decades of experience. While experience is important, it can sometimes lead to an unwillingness to adopt change. Again, the mindset becomes, “Why change anything when it has been working for 25 years?’’. Here are some guidelines to make sure all employees are speaking the same language.
Rack design by Michael Kachur – Continuous Improvement Manager and certified Lean Champion at Superior Cabinets in Saskatoon, Canada.
Within the woodworking industry, it’s common to devote money and resources to storage, trimming or cutting departments while the packaging department is left with too few resources or focus.
Assembly is a labor-intensive activity where small incremental changes can have a large impact. Most importantly, these changes don’t involve changing the layout of the shop floor.
Creating a custom-made lean work cell or workstation reduces unnecessary movement and excessive walking. When lean work cells are positioned near one another, it reduces transit time for work-in-process parts. 5S and ergonomics are critical requirements for these new lean work cells.
Wood can still be used for cart surfaces or siding. However, your stations and carts should be made from Flexpipe – which is easy to adjust or modify. Flexpipe and wood are similar in price but Flexpipe is far more durable, versatile, and much stronger compared to wood. More importantly, it won’t rot or warp due to humidity and moisture.
Wood cart Feist Cabinets & Woodworks
You can save up to 50% with Flexpipe tubes and joints compared to aluminum material handling systems. Aluminum has the required precision for machines, equipment, and robotic integrations, but it’s far too costly for carts, racks, or workbenches. Another issue with aluminum is the tendency to have water stains over time. Flexpipe is easier for workers to use, far less expensive ($8 per 8 feet of pipe), is available in multiple colors, and will never stain.
Steel is a universal material with multiple applications. However, creating material handling equipment with steel requires welders and painters. Changing existing welded structures is even more costly and time-consuming.
With Flexpipe, there’s no need for welders or painters. There’s no need to spend an inordinate amount of time trying to modify an already welded structure. Anyone with a little creativity can cut or assemble pipe and joints in a fraction of the time and costs compared to welded structures.
You can quickly put in place improvements and change your Flexpipe structures every day as ideas and suggestions come forth. No need to scrap old, welded structures. No need to re-weld existing structures. The changes you make to a Flexpipe structure in the afternoon can have you up and running in the morning.
Flexpipe is widely-recognized among North American manufacturers as a modular, scalable, easy-to-use, and inexpensive material handling solution. The company’s free design extension for SketchUp allows manufacturers to custom-design and build their own tube and joint material handling structures. Customers rely upon Flexpipe’s team for its design acumen, speed of response, and the company’s cost-effective solutions.
If you would like to see how Flexpipe can help you adopt lean concepts while reducing your costs of material handling, then contact us now.