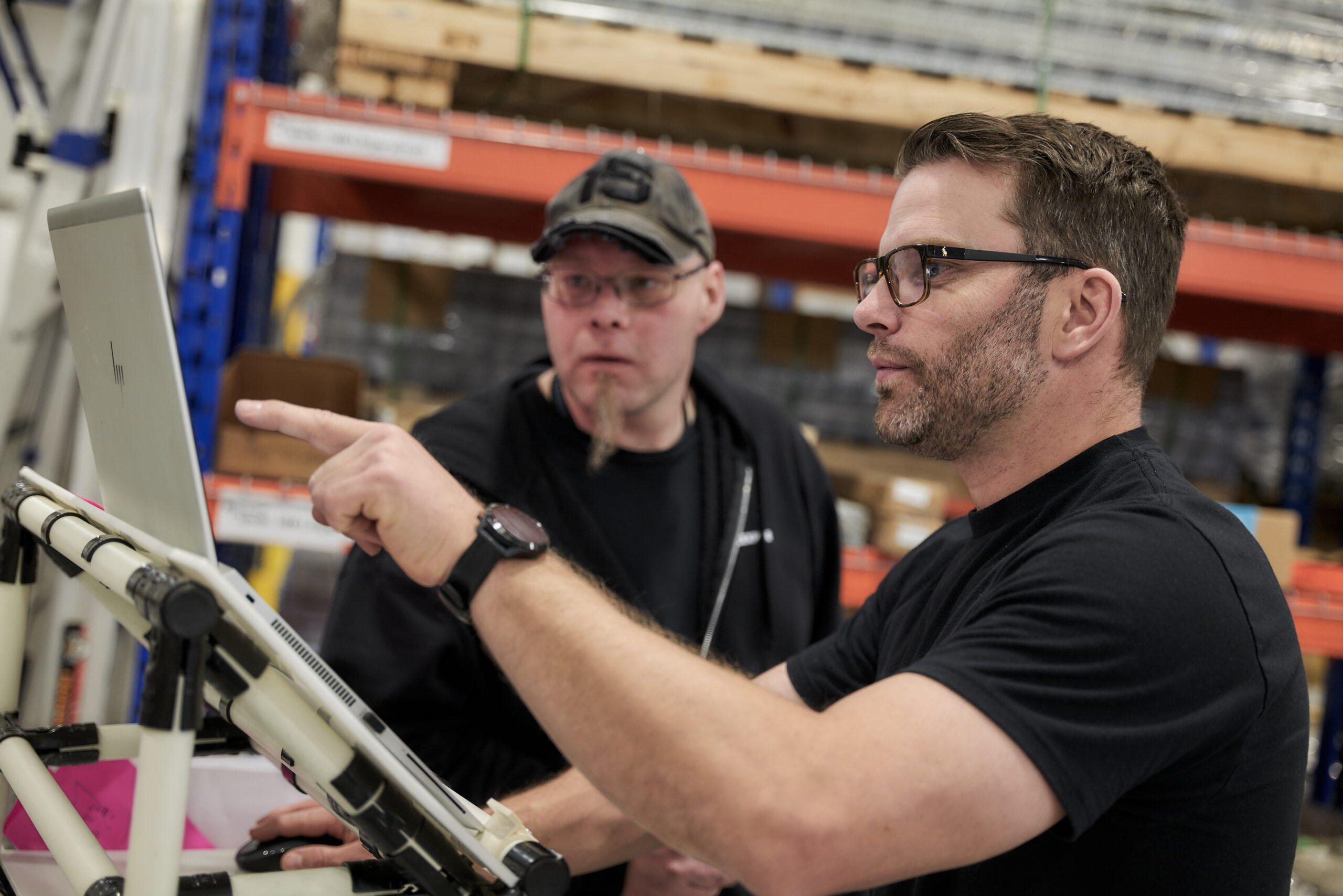
Post
7-STEP GEMBA WALK TO REDUCE MANUFACTURING WASTE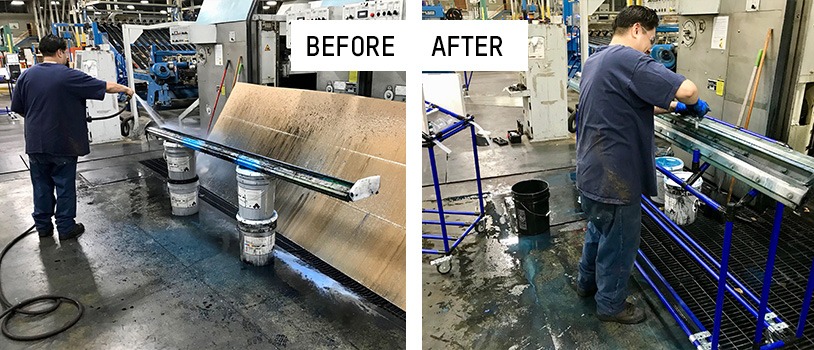
Post
KAIZEN EVENT: EVERYTHING YOU NEED TO KNOW TO GET STARTED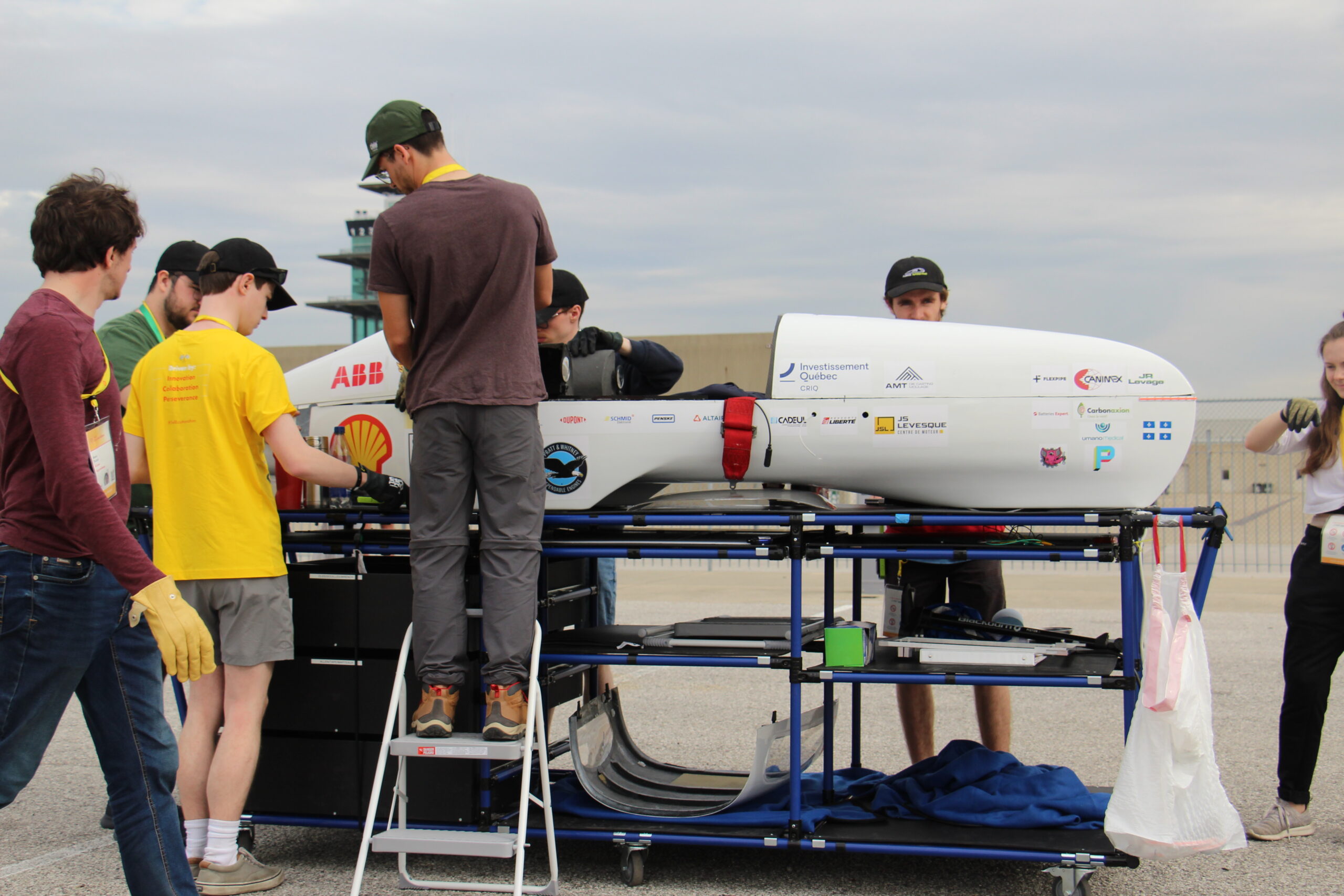
Post
A TAILOR-MADE MULTIFUNCTION CART FOR A STUDENT ENGINEERING COMPETITIONFlexpipe embarks on a digital lean transformation, implementing just-in-time and “5-zero” principles to enhance operational efficiency and manufacturing sustainability.
Cumbersome bureaucratic procedures are now a thing of the past for Flexpipe. Initiating a digital shift in 2019 regarding the digitization of all administrative documents, the company has now moved on to digitizing assembly drawings, marking a new chapter for Flexpipe, combining innovation, profitability, and manufacturing sustainability.
The company’s digital lean, distributing electronic tablets to assemblers for reading assembly drawings, particularly reflects its commitment to zero paper, a pillar of “just-in-time.” By eliminating bureaucratic waste and printing costs totaling over $30,000 annually, the company takes a proactive approach to reducing lead times and enhancing productivity.
The integration of tablet computers underwent rigorous processes, involving key players and focusing on employee training and support to ensure a smooth transition to the new work tools. This approach aligns with the “zero defects” and “zero breakdowns” philosophy, aiming to detect anomalies early and maintain production process continuity.
Flexpipe’s growth and innovation showcase its ability to pursue operational excellence while integrating just-in-time principles. Lean methodologies create a significant competitive advantage, leading to doubled sales while maintaining the same workforce.
The company’s commitment extends to achieving “zero delay” in operations, optimizing every manufacturing stage to reduce downtime and meet customer deadlines. This approach relies on meticulous production flow management, supported by seamless communication and effective digital tool utilization.
Today’s “paperless” objective necessitates a comprehensive process overhaul, encouraging the adoption of new, paperless methods. Rather than banning printing for paper enthusiasts, the emphasis is on transitioning to digital documents, eliminating previously associated superfluous steps. This concept remains relevant across all sectors, emphasizing the need to comprehend its principles and limitations. Achieving the “5 zeros” demands continual improvement commitment, evolving gradually rather than abruptly.