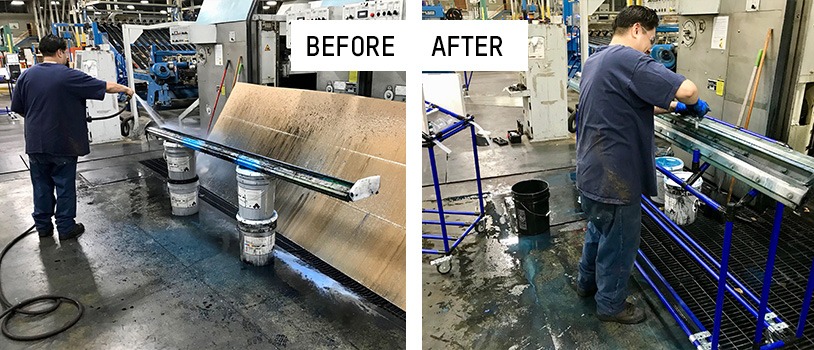
Post
KAIZEN EVENT: EVERYTHING YOU NEED TO KNOW TO GET STARTED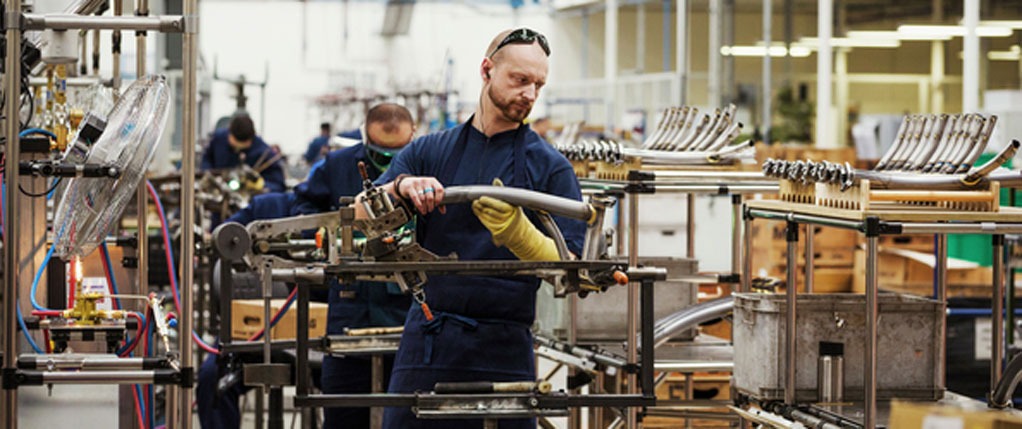
Post
10 TIPS TO REDUCE CHANGE RESISTANCE WHEN INTRODUCING LEAN MANUFACTURING
Post
10 THINGS TO KNOW ABOUT MOONSHINE SHOPSKaizen is a continuous improvement methodology incorporating multiple practical applications like 5S, value-stream mapping, fishbone diagrams, spaghetti diagrams, Pareto charts, control charts, and the Shewhart PDCA (Plan, Do, Check, Act) cycle. However, at its core, Kaizen is ultimately about fostering an environment where employees and management are motivated to improve where they work, how they work, and how work flows from one step to the next.
Make enough small improvements, and your company will achieve substantial returns like stronger product quality, improved workflow, reduced waste, and increased efficiency. While this might all sound theoretical, there are real-world Kaizen examples where companies have transformed workspaces and achieved incredible results – and the tool they use is Flexpipe.
Throughout its lifetime, your manufacturing business will most likely experience periods of rapid growth, followed by brief lulls before growing/expanding again. That continuous change requires an efficient workspace solution that can adjust and change as needed. This is exactly what the Flexpipe solution allows.
Given that the very nature of Kaizen is continuous improvement – coupled with the fact that manufacturing is never static or stationary – a modular, low-cost, scalable solution is needed that allows your employees to design, assemble, and change workspaces/workstations as needed.
These workspaces can’t be welded. They can’t be fixed structures and they can’t be haphazardly made with suspect materials like wood. These workspaces must be flexible, scalable, and comprised of durable, high-strength materials.
The Flexpipe’s steel tube and joint system is like an erector set. It is a modular and scalable workspace solution that allows you to design, assemble, change, modify, and adjust workspaces. This increased flexibility is the perfect solution for lean manufacturing/Kaizen environments and their continuous improvement efforts.
There are multiple real-world examples of how companies/manufacturers have used Flexpipe to workspaces into extremely efficient, safer, and more functional workspaces. These new Flexpipe workspaces provide employees with increased flexibility, and ideal space, and eliminate wasted movements so often associated with poorly conceived and poorly designed workspaces.
In the example above, a large cabinet manufacturer – that had adopted lean manufacturing – decided it needed to improve its workspaces by doing away with its welded, heavy, and hard-to-navigate workbenches and workstations. By using the Flexpipe modular and scalable solution, this manufacturer created a much safer, more ergonomically friendly workspace which helped to reduce trips, falls, and stumbles.
This new Flexpipe workspace allowed the manufacturer to increase their 5S score from 64 percent to 75 percent, representing a 17 percent improvement. They were also able to reduce the average distance traveled by employees within the workspace – for each unit assembled – from 180 feet to 18 feet, representing an astonishing 90 percent waste reduction. The operator no longer had to walk around the welded bench or bend over the side to get critical parts.
Another example of how a welded workbench and permanent shadow board did not allow the manufacturer to make any layout changes without incurring a substantial amount of wasted time and labor. This example comes from a corrugated packaging company that experienced high amounts of wasted time due to misplaced tools, consumables, and spare parts.
By adopting 5S principles – and using Flexpipe’s steel tubes and joints – the company was able to create a mobile-capable workspace where every tool, consumable, and spare part had a proper place. A simple solution of incorporating Flexpipe casters in the design of this workstation eliminates all the wasted time and labor required to move the workbench. Whereas two people were needed before – one is needed now and without any strain involved.
The example above comes from a manufacturer of retail refrigerated merchandisers. At this manufacturing location, efficiency was seen as a critical requirement. Unfortunately, their workspaces were large, heavy structures that didn’t fully adopt the essentials of 5S. Parts and consumables went missing, work instructions and BOM were misplaced, and operators often retained critical tools that could be used by co-workers – as evidenced by the two hand-held cordless drills on the workbench.
By using Flexpipe, this manufacturer designed a 5S workspace that was cleaner, more compact, easier to see, and had proper placement locations for parts, consumables (fasteners), and tools. Visibility increased substantially and critical parts and consumables were no longer stashed away in underutilized, hidden drawers. This represented huge savings in movement and time as employees always followed 5S end-of-day practices by putting everything away in its proper place.
If you are a current practitioner of Kaizen and lean manufacturing – or are thinking of pursuing these continuous improvement methods – having a customized Kaizen Workshop ready and able to cut, assemble, and adjust your Flexpipe workspaces and workstation structures is an absolute must.
Here are some examples of Flexpipe structures that Flexpipe and our customers use inside their Kaizen Workshops. Each of these structures has been built using Flexpipe’s steel tubes and joints.
Cutting pipe generally takes the longest when assembling your Flexpipe workspaces and workstation structures. As such, a well-designed and well-laid-out “pipe” cutting station is essential. It streamlines the cutting process and makes it easier for a single operator to lay out, measure, and cut the steel pipes.
This pipe-cutting station above has two designated overhead storage areas to hold pipes so that the operator doesn’t have to leave the cutting station. The operator simply removes the pipes from one of the storage areas on either side of the miter saw. A shop vacuum is positioned beside this saw station so that the operator can ensure a clean and debris-free area at the end of their shift – which is a critical part of 5S.
Mobile pipe-kitting carts are a great way to organize all your pipes in various lengths. These mobile carts are ideal for supplying new pipes for your pipe-cutting saw station, storing pipe that’s been cut but can still be used, or bringing new pipe to a workspace or workstation that needs minor adjustments.
A height-adjustable and mobile worktable gives your assembly team an ergonomic space where they can prepare and assemble pipe structures until those structures are ready to be placed on the floor. This height-adjustable worktable has Flexpipe’s casters so it can easily be maneuvered to different locations on your shop floor.
A height-adjustable worktable is an ideal solution when assembling larger workstations or other large Flexpipe structures. The table can be adjusted up or down, depending on what’s needed. For example, a larger or taller structure can be lowered so that it’s easier to work on.
Another Kaizen solution is the assembly tool shadow board platform above. This platform uses Flexpipe’s Kaizen Foam – a simple foam solution where employees can trace their tools onto the foam and then cut out that trace to ensure the tool is secured. The Kaizen Foam acts as a Poka-Yoke in that only the right-sized parts will fit in the foam cutouts.
A mobile PC station with a large flatscreen is especially useful when building your Flexpipe workspace or workstation and relying upon digital assembly drawings. It can also be used by production employees for any complex integrated assemblies. Simply display the drawing on your screen near the assembly area for reference. Some customers, replace the PC with a simple display board with the printed assembly drawings on the board.
The small, mobile support cart above has storage locations for consumables and fasteners both on the main level and underneath level. In addition, an angled shadow board using Flexpipe’s Kaizen foam makes sure that tools are properly placed in the right area. This mobile support cart can quickly be moved into a given area to support employees when assembling or changing workspaces.
It’s critical to have a designated assembly area for all your Flexpipe parts and that those parts be stored in that area. The Flexpipe Crib includes a mobile rack for consumable and part storage and a mobile cutting cart. A good rule of thumb is to store all the highest moving parts at waist height for easy and immediate retrieval.
Empowering your employees to be their best in a Kaizen environment so they reduce waste and make improvements requires giving them the tools they need to succeed. Those tools must be easy-to-use, simple, and straightforward and allow your employees to make a real difference.
Flexpipe is that all-important tool for workspace optimization and efficiency.
To learn how Flexpipe can help your manufacturing facility adopt Kaizen and lean manufacturing solutions that reduce the costs of each of your workspaces, contact us now.