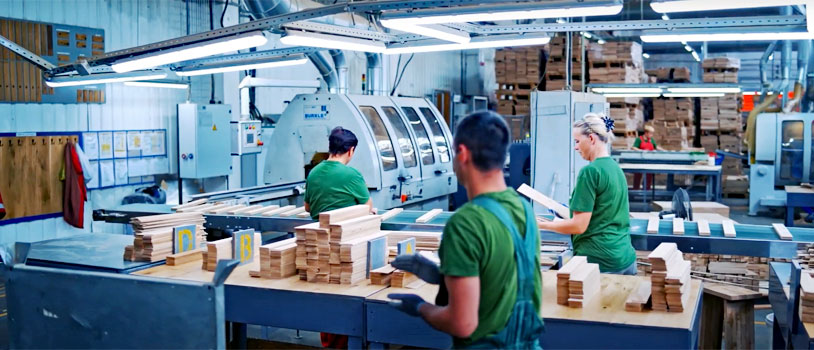
Post
MANUFACTURA CIRCULAR: LAS REGLAS DEL CíRCULO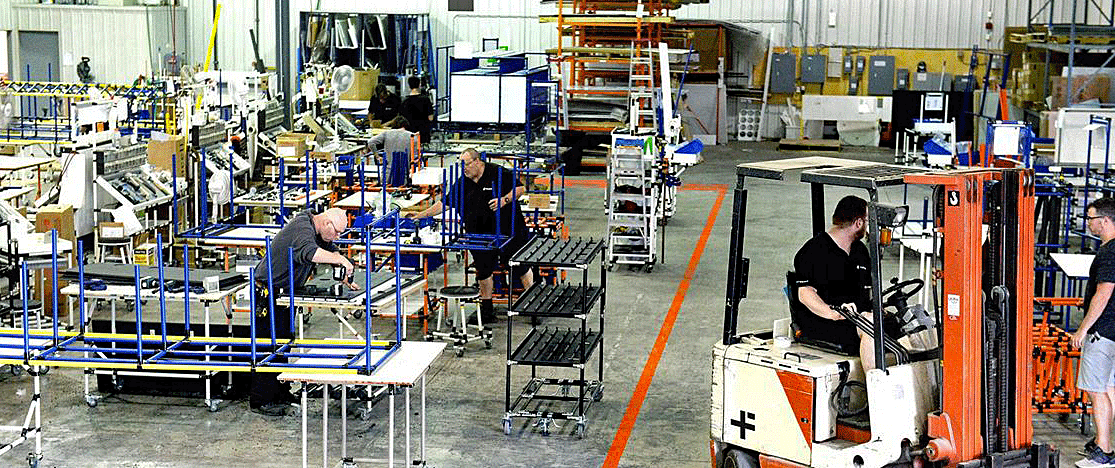
Post
FLUJO DE MATERIALES : UN ELEMENTO CLAVE EN LA FABRICACIóN CIRCULAR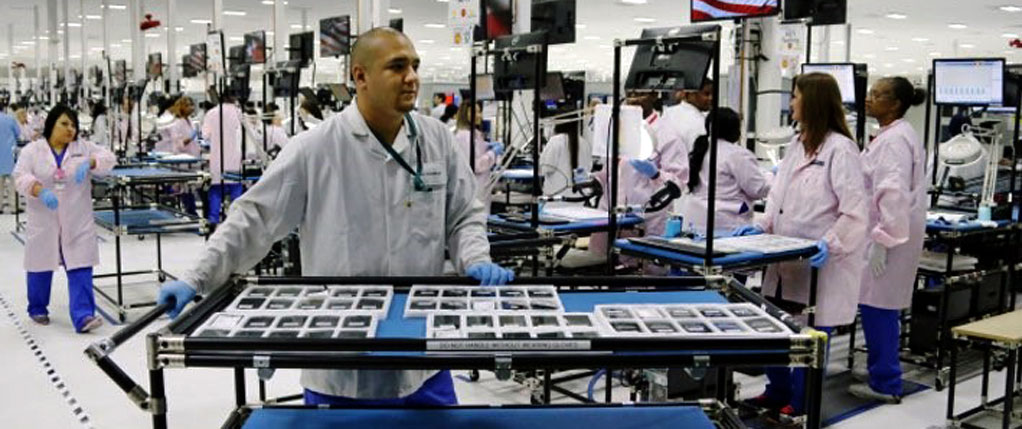
Case Study
SISTEMA DE TUBOS Y UNIONES PARA FABRICANTES DE EQUIPOS MéDICOSSafran Landing Systems, líder mundial en sistemas de aterrizaje y frenado de aeronaves, había comenzado a trabajar para duplicar el tamaño de su planta de Mirabel (Que.) en 2014. Como defensores acérrimos del principio de “Lean Manufacturing”, los directivos de Safran querían aprovechar la ampliación para encontrar una forma de reducir los costes de sus sistemas de almacenamiento. Siga leyendo para ver cómo pudieron reducir el coste en más de un 40% gracias a un sistema modular de tuberías y juntas.
Las capacidades de la compañía abarcan todo el ciclo de vida de los productos de aterrizaje y frenado, desde el diseño y la fabricación hasta el soporte, la reparación y la revisión. Más de 7.000 miembros del personal trabajan en las instalaciones de Safran Landing Systems en Europa, América del Norte y Asia.
Al ser socio de 30 de los principales fabricantes de aviones comerciales, militares, de negocios y regionales, Safran interviene en más de 25.000 aeronaves en total, que realizan más de 40.000 aterrizajes por día. No hace falta decir que la empresa desempeña un papel importante a la hora de garantizar que los pasajeros lleguen a su destino de forma segura.
La expansión catalizó para que la dirección realizara cambios significativos, sobre todo en lo que respecta a la productividad de los empleados. Para ello, se analizó la forma en que los empleados utilizaban las herramientas y los equipos en sus puestos de trabajo para llevar a cabo sus respectivas tareas.
Un elemento a reconsiderar era el almacenamiento de piezas y herramientas en grandes armarios y cajones metálicos. Además de ser costoso, este tipo de almacenamiento resultó ser un reto para los recién llegados que tenían problemas para encontrar las piezas necesarias para realizar tareas específicas.
El equipo de Lean Sigma, que lideraba el programa de mejora continua, comenzó a buscar una nueva alternativa para prescindir de los armarios metálicos. El equipo pronto descubrió a Flexpipe, un desarrollador de sistemas modulares de tuberías y juntas diseñados para entornos industriales y de fabricación. Flexpipe permitió a los empleados diseñar yconstruir sus estructuras de almacenamiento, carros de equipamiento, estanterías de manipulación y mucho más. Los armarios metálicos existentes se sustituyeron pronto por estanterías modulares para almacenar las piezas, mientras que los tableros de sombra se introdujeron para almacenar las herramientas.
El sistema Flexpipe se integró sólo en una pequeña parte de la planta de forma experimental para ver cómo se adaptaban los maquinistas al cambio. ¿El resultado? Un éxito abrumador. La adaptabilidad y flexibilidad del equipo fueron un claro ganador. Los maquinistas se engancharon y muchos de ellos solicitaron estaciones de trabajo de fabricación ajustada Flexpipe.
Desde la introducción de Flexpipe durante la ampliación de la planta, se han creado más de 600 estructuras para unos 200 trabajadores de fabricación de la instalación. En la actualidad, aproximadamente el 80% de los departamentos de la planta utilizan Flexpipe de alguna manera, y se espera que esta cifra aumente en los próximos años. Esto dice mucho sobre el valor añadido del sistema modular de tuberías y juntas en Safran.
Flexpipe no sólo permite a los trabajadores de la planta de Mirabel operar mejor y de forma más eficiente; las estructuras también reducen el coste en más de un 40% en comparación con los armarios metálicos. Además, el equipo de Lean Sigma de la planta de Mirabel puede proporcionar dichas estructuras bajo demanda.
Por último, dadas las importantes ventajas de los sistemas modulares, el equipo directivo de Safran creó un taller in situ en sus instalaciones de Mirabel para almacenar permanentemente el inventario de Flexpipe. De este modo, se pueden construir varias estructuras en un plazo breve. Muchos empleados también participan en la creación de sus estructuras Flexpipe, lo que permite obtener estructuras muy personalizadas que pueden aumentar aún más el rendimiento.