Descubra las ventajas de la manufactura esbelta en las industrias del cartón ondulado y del embalaje
Las industrias del embalaje y del cartón corrugado deben esforzarse más para satisfacer la creciente demanda del sector empresarial, en particular, debido al importante aumento del comercio electrónico. Vea cómo Leslie Pickering convierte este problema en una oportunidad en las instalaciones de fabricación de cartón corrugado.
Las industrias del embalaje y del cartón corrugado deben trabajar más para satisfacer la creciente demanda del sector. El importante aumento del comercio electrónico y de los servicios de entrega de comidas está obligando a los actores a replantearse su forma de trabajar. Una entrevista con Leslie Pickering, consultora y copropietaria de Quadrant5, detalla las mejoras en el método de trabajo y en los procesos necesarios para aumentar la productividad de los fabricantes de la industria del papel y el cartón.
El enfoque de Leslie se centra en los beneficios de la manufactura esbelta. Presenta algunos de los principales desperdicios en la manufactura esbelta, 12 éxitos lean tras la implementación del sistema propuesto, el paradigma relacionado con la resistencia al cambio, así como el sistema de manejo que fomenta la creatividad de los empleados.
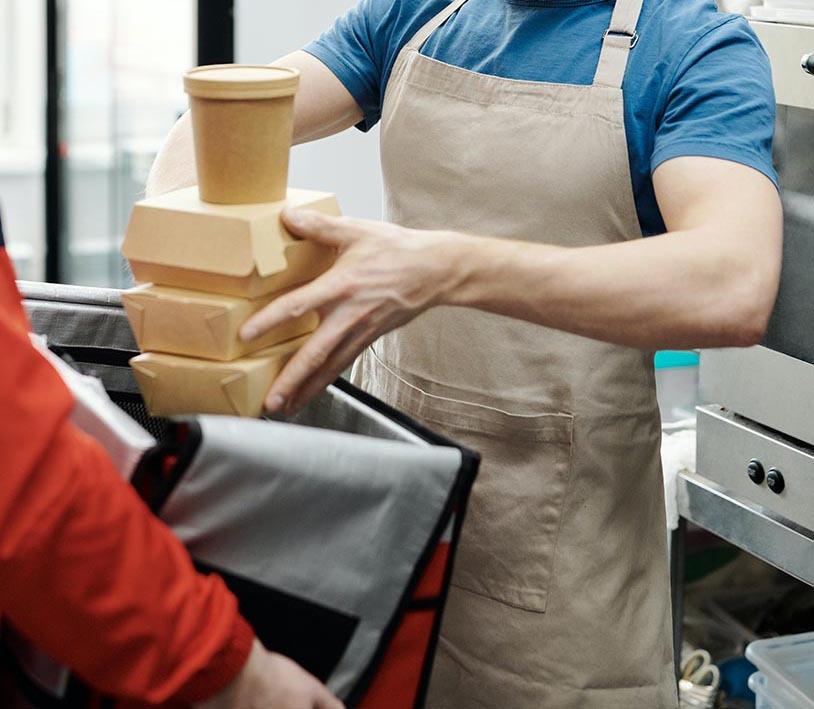
Este artículo tratará los siguientes temas:
-Las 5 tendencias que están cambiando la industria
-¿Por qué esforzarse tanto para convertirse en Lean?
-Los 12 logros de una industria lean tras una gran jornada trabajo
-La resistencia al cambio es inevitable
-El sistema de manipulación de materiales forma parte de la manufactura esbelta
Acerca de Leslie Pickering
Leslie A. Pickering es la copropietaria de Quadrant5, una consultora ubicada en San Francisco, especializada en la transformación Lean. Leslie aporta más de 40 años de experiencia en mejora de procesos internacionales, fabricación y operaciones. Es un reconocido especialista en el Sistema de Producción Toyota (TPS) que ha implementado con éxito metodologías de transformación dentro de las industrias de envasado, bebidas, grandes almacenes, plásticos y automoción.
Proporcionando una visión general de la industria del cartón ondulado y del embalaje, Leslie afirma con elocuencia: “Amazon y las ventas por Internet están cambiando el mercado. Estamos haciendo más cajas que nunca, ¡y hay que hacerlo rápido! Internet ha traído una nueva limitación de tiempo”
Las 5 tendencias que están cambiando la industria
En 2016, los envíos de la industria del cartón ondulado aumentaron un 2,1%. Además, según el informe de Simether Pira, el comercio electrónico ayudará a que el sector crezca en torno al 3,7% anual y se espera que alcance los 300.000 millones en 2023. Hay 5 tendencias predominantes en el mercado de los envases de cartón corrugado:
- comercio electrónico con un crecimiento estimado del 20% anual para los próximos 3 años.
- plataformas de caja a la carta impulsadas por el comercio electrónico como Amazon.
- sostenibilidad, especialmente en lo que respecta a los productos de cartón ondulado.
- envases listos para la venta al por menor como los servicios de kits de comida.
- avances en la impresión digital.
Foto: Los operadores tienen ahora su programación en la consola principal HP 17000, eliminando la necesidad de un sistema de programación en papel. Al mantener el entorno digital actualizado, más onduladores pueden fabricar envases sin herramientas.
¿Consolidación adicional?
Actualmente hay 2.000 empresas activas en la industria del cartón corrugado en EE.UU., que emplea a más de 141.000 personas. Los cuatro mayores fabricantes tienen una cuota del 33,1% de la industria, liderada por WestRock. Aunque la industria de la caja de cartón ondulado se ha ido consolidando desde 2016, pasando de 690 plantas a 465 plantas onduladoras, según Fibre Box Association, Leslie Pickering espera más y más consolidación en los próximos cinco años dentro del mercado.
Espero más y más consolidación en los próximos años.Leslie Pickering – Copropietaria de Quadrant5
Un nuevo actor importante en los Estados Unidos
Según el Sr. Pickering, el mercado cambiará aún más el potencial con la llegada de un actor importante de Europa, BS Smith. “Vienen con las mejores prácticas y obligarán al sector a mejorar” DS Smith se encuentra entre los seis principales proveedores de Europa junto a Georgia-Pacific, International Paper, Mondi, Smurfit Kappa y WestRock.
DS Smith ya se introdujo en el mercado estadounidense en 2017 al comprar el 80% de Interstate Resources y sus 24 centros de producción. Continúa: “Los corrugadores tendrán que mejorar sus operaciones con DS Smith de por medio. Compran bien el papel, fabrican muy bien y tienen una nueva disposición y nuevas tecnologías.”
También he visitado 2 plantas de DS Smith en Reino Unido y puedo confirmar que son muy eficientes.Pierre Audet – Presidente de Proden – A troquelador plano y rotativocon sede en Montreal, Toronto y México.
¿Por qué esforzarse tanto para convertirse en Lean?
La presencia de la manufactura esbelta en la industria de un vistazo
Toyota Production System (TPS) introdujo los principios de la manufactura esbelta en América, y se ha extendido ampliamente entre los fabricantes de automóviles desde los años 90 -y ahora sus proveedores. Leslie, que ha trabajado con múltiples industrias, pero sobre todo con onduladoras, sostiene que la industria del envase y embalaje y del cartón corrugado lleva una década de retraso con respecto a otros sectores, como el de la automoción.
Los corrugadores gastan millones en la adquisición de máquinas, pero tienden a minimizar el impacto de los equipos de manipulación, la formación y la distribución. Estos elementos tienen un efecto significativo en la productividad de las máquinas! Muchos fabricantes del sector se centran en la fabricación de cajas, no en los procesos de fabricación de las mismas. Esta es la diferencia entre un entorno industrial y un entorno visual. Con los procesos adecuados y con personas comprometidas con ellos, la calidad es automática.
La atención se centra demasiado en la fabricación de cajas, y no lo suficiente en los procesos de fabricación de cajas.
Hay varias razones por las que las empresas inician la integración de Lean:
- El inminente cierre de sus operaciones cotidianas.
- La dirección piensa que está dejando dinero sobre la mesa y quiere ser más eficiente reduciendo los costes.
- Un traslado a una nueva instalación o a punto de implantar un nuevo equipo importante..
- Trabajar en cuestiones importantes como el exceso de efectivo inmovilizado en el inventario, los largos plazos de entrega o la calidad.
Las empresas bien gestionadas que son buenas en la fabricación y tienen unas ventas satisfactorias pueden tener unos márgenes que oscilan entre el 8,5 y el 11%, y aún así piensan que se están dejando un 3% o un 4% sobre la mesa. Necesitan mejorar los procesos y, en general, la eficiencia para conseguir los puntos porcentuales extra. La gente se centra en hacer cajas, pero no lo suficiente en los procesos, y esa es la transición que deben acometer. Otros corrugadores son muy buenos en ventas, tienen un gran equipo de ventas pero no son tan fuertes en la planta de producción; necesitan trabajar en esto para mejorar los márgenes.
Color Resolutions International, que suministra tinta a varios fabricantes de envases, comenzó su andadura lean en 2002. El presidente y director general de la empresa, George Sickinger, explica: “Nos embarcamos en la construcción de una nueva instalación y queríamos incorporar la manufactura esbelta en la nueva instalación. Teníamos una oportunidad ideal para implementar el proceso desde el diseño del edificio hasta el proceso de fabricación; era lo correcto para invertir.”
La alta dirección en el proceso de integración Lean
Leslie y su equipo suelen empezar con una auditoría que revelará dónde se necesitan mejoras. Una vez que se inicia el viaje lean, es crucial una reunión inicial presidida por el presidente para comunicar por qué la misión es tan importante. Todas las empresas que han pasado por una transformación de este tipo le dirán que el propietario del proyecto y la alta dirección deben hacer suyo el proyecto para que tenga éxito.
InteliCoat Technologies, proveedor de papel recubierto, películas y sustratos especiales para tecnologías de la imagen, integró la manufactura esbelta en noviembre de 2007. Una subvención de casi 400.000 dólares concedida por el estado de Massachusetts ayudó a financiar la integración. Su anterior presidente, Meyer Weiss, explica: “Nuestro director general ha liderado este esfuerzo; sin liderazgo en la cúpula, los beneficios de Lean no pueden aprovecharse plenamente”
.
A la hora de determinar el área en la que implantar la manufactura esbelta, en todos los casos, debería empezar siempre por una isla de excelencia. Podría, por ejemplo, centrar sus esfuerzos en la máquina, que requiere la inversión más importante o que tiene la mayor visibilidad porque todo el mundo pasa por delante de ella.
La implantación de una planta piloto suele llevarse a cabo en empresas con múltiples plantas. Una vez terminada la implantación en la primera ubicación, se puede comenzar en las otras plantas donde los miembros del equipo del comité de mejora continua pueden formar a los empleados de las otras plantas.
8 desperdicios de fabricación
El Sistema de Producción Toyota estableció 7 desperdicios de fabricación que no añaden valor al cliente. Estos desperdicios de fabricación son:
- Transporte innecesario,
- Exceso de inventario,
- Movimiento innecesario,
- Esperar
- Sobreproducción
- Over-processing
- Defectos
Sin embargo, creemos que es esencial añadir un octavo residuo: el despilfarro del potencial humano. Más adelante en el artículo encontrarás más información sobre este octavo despilfarro propuesto.
La gestión eficiente de los suministros, junto con la reducción del exceso de inventario, es una ventaja significativa en la industria del envasado. La materia prima no sólo ocupa mucho espacio, sino que también requiere una importante inversión de capital. En un escenario ideal, se compraría la cantidad adecuada de materia prima para los pedidos. Sin embargo, existe un miedo generalizado a quedarse sin materia prima; por lo tanto, se compra más para evitar quedarse sin ella para los próximos trabajos. Un cambio de paradigma sería muy beneficioso, según Leslie.
El movimiento innecesario en la gestión de materiales es el despilfarro más importante del sector, según Leslie. Cuando los operarios caminan alrededor de su máquina sin ninguna razón válida, la abandonan para hacer el papeleo o para comprobar si el material está listo para la siguiente tirada, no sólo están haciendo caminatas y movimientos innecesarios, sino que no dejan la calidad para nadie. Esto es especialmente problemático cuando se trabaja con máquinas antiguas.
La sobreproducción es una práctica común en la industria. Para la mayoría de los pedidos se aplica la regla de “+/- 10%”. Por ejemplo, un pedido de 6.000 cajas podría acabar de 5.400 a 6.600 cajas. “Si lo piensas, esto es algo terrible: se cobra de más a los clientes para conseguir lo que quieren”, explica Leslie. Este 10% se factura al cliente, pero a veces es un punto de negociación.
Esperar el siguiente pedido o material como papel, herramientas, tinta o papeleo es otra gran pérdida. Los empleados u operarios que están en modo “espera” representan una enorme pérdida de tiempo y no generan ningún valor añadido para el cliente. El tiempo es precioso en una línea de producción: si hay que cambiar una pieza, una máquina que necesita una pequeña reparación, unas instrucciones mal explicadas para el siguiente trabajo o una herramienta que falta y que debería estar al alcance de la mano, todo ello roba unos minutos preciosos.
Los 12 logros de una industria lean tras una gran jornada trabajo
- Se utiliza un sistema pull para el sistema de producción
El sistema pull está implantado en todo el proceso de producción. Hay visuales claros en toda la planta para mostrar el progreso de la producción. Los niveles de producción se ajustan periódicamente para reflejar los pedidos de los clientes. Las reglas de Kanban están establecidas y se respetan. Además, la cantidad de Kanban por contenedor es mínima.
#kanban #heijunka #flexiblemanpower #definedroles
Foto: La implantación de un sistema Kanban permite la gestión del inventario, incluso del papel de impresión de la estación de trabajo.
- Trabajo estandarizado en todas las celdas de trabajo
- El tiempo de cambio está limitado a 10 minutos
- El flujo de una pieza está en marcha en toda la planta
- El Poka-yoke ayuda a facilitar el trabajo y mejora la calidad
- Control visual para ayudar a los jefes de equipo
- Un programa de 5S sostenible
- La gestión del inventario se realiza visualmente
- Existe un programa kaizen en toda la empresa
- Los programas de formación están por delante de los de la competencia
- Un programa de mantenimiento preventivo reduce el tiempo de inactividad
- Es un lugar de trabajo sin accidentes
El trabajo está bien equilibrado, sin tiempo de espera durante cada ciclo. Las instrucciones de trabajo tienen como objetivo la producción por ciclos y por horas; se hace un seguimiento de las mismas y todos los empleados están familiarizados con ellas. Las instrucciones de trabajo se siguen en toda la planta y se revisan y actualizan periódicamente. En general, el trabajo estándar es sencillo y hace que el trabajo sea más accesible para trabajadores como otros operarios, supervisores e incluso conductores de carretillas elevadoras.
#trabajoequilibrado #trabajoestándarizado #tiempo de trabajo #ciclotiempo #célula de trabajo
Foto: Una empleada entrando en su celda de trabajo en el BOBST 616 FFG Seguirá un guión claro en lugar de instrucciones estandarizadas.
El equipo de cambio debe incluir a los operarios, y el proceso de cambio debe realizarse lo más rápidamente posible (idealmente, en menos de 10 minutos). El proceso está estandarizado en toda la planta. Existe una célula de demostración y se realizan frecuentemente eventos kaizen para mejorar el tiempo de cambio. Existe una buena relación entre el tiempo de cambio y la producción. La asignación de máquinas es tan clara como el programa de producción. La preparación y las actividades fuera de línea se maximizan sin detener la maquinaria. Los troqueles, las herramientas y otros equipos están codificados por colores.
#5s #preparación #trabajoestandarizado #cambio
Foto: Se han preparado 3 carros para los próximos tres trabajos. Cada carro contiene todo lo que se necesita para 1 solo trabajo, lo que consecuentemente reduce el tiempo de inactividad.
Todos los procesos son claros: los productos, los componentes y la materia prima pasan de un proceso al siguiente de una en una (flujo de una pieza). El material entra y sale de la celda de trabajo por una ruta de transporte programada. Cada proceso está claramente vinculado al siguiente, y es fácil seguir el flujo de materiales. En última instancia, los procesos secundarios (pintura, subcontratación, etc.) están vinculados a toda la planta.
#flujo de materiales #procesos #cambiador #flujo de una pieza
Foto: Una sala Obeya (sala grande en japonés) está en construcción en Royal Containers, en Brampton, Ontario. Pregunte a los sectores automovilístico y aeroespacial cuáles son las mejores herramientas para expulsar los costes de su operación, y la respuesta será las salas Obeya.
Los distintos equipos disponen de dispositivos Poka-yoke, por lo que es imposible puentearlos. El Poka-yoke es sencillo, robusto, fiable y rentable. Se someten a controles y pruebas periódicas, y están etiquetados, codificados por colores y mapeados.
#pokayoke #jidoka #eficacia
Foto: Poka-yoke – El cliente deja en las trampas correctas el utillaje para asegurar que vuelve a la máquina de forma correcta.
Se entiende claramente en qué consisten las situaciones normales y anormales. Existe un sistema de señalización (luz/alarma) que es entendido por los operarios y el equipo directivo. Cuando se produce una situación anormal, existen procedimientos y el jefe del equipo responde rápidamente. Por ejemplo, en el control de calidad, es fácil detectar una situación anormal con un indicador visual (que se muestra en la imagen siguiente). Si no se instala ningún indicador visual sobre la parte superior de las cargas, se trata de una situación anormal y hay que actuar.
#andonsystem #teamleader #signal #abnormalsituation
Foto: El indicador visual de la caja inspeccionada sobre la carga de la Bobst 618 FFG muestra que la calidad es fuerte en Acme Corrugated.
Hay un lugar para todo, y todo está en su lugar con el programa 5S. Todos los empleados entienden el principio y sus beneficios. La aplicación de las 5S es evidente en toda la planta y la oficina. Las 5S son sostenidas por los miembros individuales del equipo mediante la gestión visual de las herramientas y la programación de la rutina.
#5s #clasificar #ponerenorden #brillar #estandarizar #sostener
Foto: La estación de cola POUT (Point Of Use Tooling) para FFG proporciona las herramientas correctas que los miembros del equipo necesitan cuando las necesitan, en las cantidades correctas y en el lugar correcto. Al erradicar las cajas de herramientas se ve inmediatamente si falta una herramienta, cosa que no se puede hacer si están escondidas en cajas de herramientas.
Se establecen e identifican todas las ubicaciones del inventario. Las estanterías y los contenedores están etiquetados, y el principio “Primero en entrar – Primero en salir” (FIFO) está establecido y se mantiene. Los niveles de inventario (mínimo/máximo) se ajustan regularmente para tener en cuenta las fluctuaciones de uso. Se utilizan controles visuales para evitar la mezcla de piezas y el desbordamiento.
#fifo #minmax #contenedores
Foto: Estantería de gestión de tinta First in first out (FIFO) para reducir el stock de la impresora digital HP.
La cultura de la empresa reconoce los beneficios del kaizen y la dirección apoya al equipo dedicado a sus actividades e iniciativas. Las actividades kaizen se programan, se rastrean y se vinculan a las metas y objetivos de la empresa.
#kaizen #sugerencias #iniciativas #kaizenteam
Foto: Royal Container en Toronto está llevando a cabo un evento kaizen en la moonshine shop.
Hay un programa de formación formal para las nuevas contrataciones, y los miembros del equipo están formados para ser polivalentes. Existe un programa de desarrollo/carrera profesional para los miembros del equipo. Se publica el estado de la formación de todos y se programan regularmente cursos de actualización.
#multiskilled #trainingprogram #kaizentraining
Foto: Aquí está Tom entrenando el trabajo estandarizado para un nuevo empleado. El trabajo estandarizado cuando se ejecuta el cambio de trabajo hace que la formación sea mucho más fácil y cuesta menos.
Se asigna tiempo para el mantenimiento preventivo total (TPM) en toda la planta. El operario que participa en el mantenimiento diario es una parte integral del proceso. Existe un programa de calibración de herramientas para garantizar la precisión de los equipos. El tiempo de inactividad se rastrea y analiza. Se determinan las causas raíz de los problemas y se incorporan contramedidas al mantenimiento preventivo.
#tpm #rootcauses #preventivemaintenance #downtime
Foto: El mantenimiento preventivo tiene lugar en una BOBST MARTINS
Hay un programa de seguridad escrito que conocen todos los miembros del equipo y que se aplica colectivamente. El coordinador de seguridad participa en la auditoría diaria. Se recopilan los accidentes: se adoptan y analizan las contramedidas. La dirección y los visitantes se adhieren al programa de seguridad.
#safetyprogram #PPE #MSDS #accidentfree
Foto: Señalización clara del suelo del pasillo para evitar que los vehículos se acerquen a los operarios.
La resistencia al cambio es inevitable
Cualquier buen equipo directivo sabe que los empleados de su empresa son un elemento vital para alcanzar el éxito. Una integración de manufactura esbelta requiere que todos estén a bordo del proceso y trabajen juntos, para que llegue a buen puerto.
Todos los empleados apoyaron la idea de que la manufactura esbelta iba a ser una ventaja para todos los implicados, y entonces se impregnó de forma natural en la cultura de la empresa. El sindicato desempeñó un papel fundamental, afirma Meyer Weiss, donde “Para nuestros empleados del sindicato, en particular, está claro que la cultura esbelta está salvando puestos de trabajo y haciéndonos más competitivos. La dirección del sindicato ha acogido bien el Lean y se ha implicado plenamente en la promoción de los beneficios para los empleados y la empresa”. Continúa diciendo que “los empleados tienen que ver lo que les beneficia. Por ejemplo, facilitar el trabajo, facilitar la rotación de las vacaciones y, por último, salvar puestos de trabajo, etc.”
Leslie Pickering añade: “Hay que demostrar que no va a ser otro sabor del mes”.
InteliCoat, Heritage Paper, President Container o Royal Container son ejemplos de empresas que trajeron a varios consultores para ayudar a desarrollar los pasos de la implementación y formar a los empleados. Los expertos externos, como los consultores de Lean, desafiaron el statu quo y los paradigmas actuales.
Además del grupo consultor Q5, los empleados de Royal Containers han dado un paso adelante y han asumido la responsabilidad y la propiedad de la emocionante renovación. Un empleado de Royal desde hace mucho tiempo, Dan Rudnicki, ha liderado el equipo interno para garantizar el cumplimiento de los objetivos. Un gran socio consultor sabe cómo hacer el trabajo, y es muy práctico, no sólo crea grandes presentaciones de PowerPoint.
Kim Nelson, presidente de Royal Containers, ubicada en el sur de Ontario, comenzó su implementación lean inicial en 2019 que se completará a finales de año. La segunda integración lean comenzará después en su otra planta en la cercana Brampton.
Su objetivo es reducir los costes en las operaciones, mejorar la calidad con una mejor calibración y lograr un tiempo de entrega más rápido con la implementación de procesos racionalizados. “Nos embarcamos en un plan de IC para cambiar todo el entorno de la planta. Hasta ahora, estamos en el buen camino y nos encanta cada minuto”, dijo la Sra. Nelson.
El sistema de manipulación de materiales forma parte de un viaje de fabricación esbelta
Tradicionalmente, la industria ha utilizado estructuras de madera o soldadas. Ocasionalmente, el equipo de manipulación de materiales puede ser suministrado por la maquinaria (OEM), y se utilizará tal cual.
Estos carros de transferencia de troqueles para troqueles rotativos, troqueles planos y planchas de impresión han estado en el mercado y son ampliamente utilizados.
Son de acero resistente y se adaptan a los troqueles rotativos DRO, EVOL y a los troqueles planos Platen y Bobst.
La foto es de Wagner Die Supply, un fabricante de troqueles con varias sedes en Estados Unidos.
Las estructuras de acero funcionan por ahora, pero cuando los procesos acaben cambiando, ya no se adaptarán a la tarea en cuestión.
Si el equipo de manipulación de materiales no es suministrado por el OEM o no es adecuado, se pueden utilizar sistemas de tuberías y uniones para construir una solución alrededor de la máquina.
“Normalmente no compramos nada de Uline para carros o estanterías por 2 razones: primero, no hay ventaja competitiva: tu competencia puede comprarlo. Y en segundo lugar, nunca tiene el tamaño ideal para el trabajo, por lo que tienes que ajustarte a él en lugar de que la estructura se ajuste a ti y al trabajo”, explica Leslie. Llevamos 10 años utilizando tubos y uniones. Puedo cambiar una estructura de tuberías y uniones en 30 minutos. El problema por la mañana y la solución por la tarde”.”
Aproveche la creatividad de sus empleados con el sistema de tubos y uniones y evite el octavo desperdicio: la pérdida de las buenas ideas de los empleados.
Ejemplos de estructuras modulares de tubos y uniones
Aquí hay algunos ejemplos de estructuras modulares de tubo y unión en uso en una planta de fabricación de envases de cartón corrugado en Ontario.
Estación del operario: este tipo de estructura pone la ergonomía en primer plano y ayuda a reducir la fatiga corporal, especialmente cuando hace calor. Los procesos, los trabajos y los requisitos cambian con el tiempo. Por eso, cuando un nuevo trabajo requiere un nuevo folleto de instrucciones, por ejemplo, podemos modificar la estación para que el folleto sea fácil de localizar. Los sistemas modulares nos permiten realizar cambios rápidos a un bajo coste.
Un carro – un trabajo : En el podcast Aprenda cómo la manufactura esbelta ayuda a los corrugadores a adaptarse a los cambios en su industria con Leslie Pickering, Leslie explica la configuración ideal donde todo está en el carro para el trabajo. “Llevamos 20 años utilizando el concepto de 1 carro, 1 trabajo. Desde 10 metros de distancia, puedo ver si todo está ahí para el siguiente trabajo. El operario puede examinar el carro mientras la máquina está en marcha y luego hacer las preguntas adecuadas, como “¿por qué no está la tinta?”. Si el horario cambia y los carros para los próximos 3 trabajos están listos, normalmente el cambio se puede acomodar. El objetivo es reducir el tiempo de inactividad y que las máquinas funcionen más tiempo; ¡el coste de la máquina por minuto es importante!”
Tablas 5S: Las herramientas importantes suelen estar en las cajas de herramientas. Aunque los OEM suministran cajas de herramientas, es mejor tenerlas todas expuestas en un tablero 5S para ver si falta alguna herramienta, en lugar de que estén revueltas en una caja.
La gestión visual necesita 3 elementos:
- Etiqueta de identificación
- Color
- La sombra de la herramienta
Son fundamentales para que el sistema funcione de forma eficiente y sostenible en el tiempo, tanto en la oficina como en el área de producción. Muchos operarios no tienen a mano lo que necesitan. Un cambio de herramientas es como un cambio de neumáticos de un coche de carreras: Un turno debe tenerlo todo. Todas las mañanas haga una comprobación visual para ver si su equipo tiene todo lo que necesita.
Moonshine shop: Aquí es donde ocurre la magia; es donde las ideas presentadas por los operadores cobran vida. Ya sea a partir de un boceto o de un reto de IC (“Mejora Continua”), asegúrese de confirmar y comprender a fondo lo que quiere el operario y, a continuación, construya una estructura que satisfaga las necesidades expresadas en el boceto. Un taller de IC está pensado para capacitar a los trabajadores. En él, hay de todo para desarrollar soluciones a los problemas. Una solución rápida aplicada en el área de producción ayudará a fabricar cajas más rápido y más barato. Como bien dice Leslie, “¡Problemas por la mañana, solución por la tarde!”
¿Quién puede ensamblar? La mayoría de los operadores pueden hacerlo – es relativamente fácil. Los miembros del equipo de mejora continua también pueden ayudar.
Desea solicitar ideas a las personas directamente implicadas en las operaciones diarias. Recuerde que no todas las ideas generadas por el personal serán geniales, pero puede participar en el proceso y enseñarles los ingredientes de una gran idea.
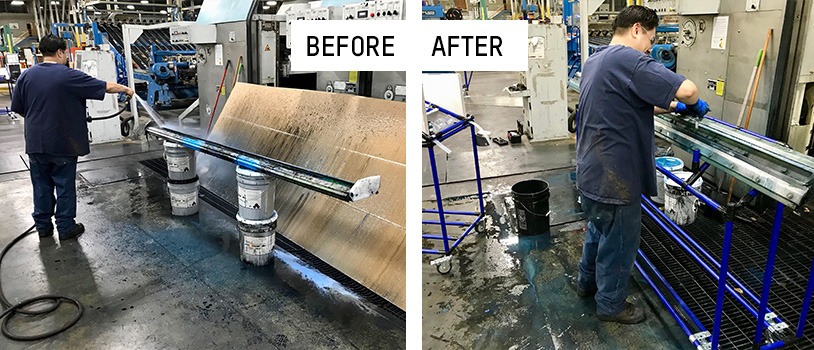
Foto: ¿Sigue limpiando las cámaras en los cubos de tinta? Nuestros carros de cuchillas para cámaras reducen el tiempo de TPM y el estrés del operario en el cuerpo, garantizando una forma mejor y más segura de realizar esta importante tarea.
Foto: Desplazamiento de la antigua mesa estándar industrial sustituyéndola por la nueva estación de trabajo móvil del equipo y la estación de control de tinta para una Bobst Martin 1228 FFG.
Foto: ¿Han llegado las herramientas para ese trabajo caliente? ¿No encuentra las herramientas? ¿Las herramientas se entregan en la puerta equivocada? Vea el antes y el después para hacer de la entrada/salida de herramientas un proceso.
La presentación de las herramientas especializadas de forma correcta es importante, especialmente cuando se presentan en un carro móvil. Así que se mueven a la posición óptima, reduciendo el desperdicio de movimiento. Los segundos que se ahorran aquí permiten muchas horas de tiempo de ejecución adicional gracias a las técnicas de cambio de trabajo de las cañas.
Significado del color rojo y verde de las paredes:
VERDE indica nueva herramienta para la instalación, aquí es entregado por el proveedor. Es el único lugar en el que el OEM puede depositar el nuevo instrumental además de ser el único lugar en el que alguien tiene que buscar la entrega del nuevo instrumental.
ROJO indica que la herramienta tiene un problema distinto al de necesitar una reparación o modificación. El establecimiento coloca las herramientas para reparar en la zona roja y coloca el papeleo correspondiente en una de las cuatro papeleras de la derecha, en función del proveedor que vaya a realizar el trabajo.
#mudas #reduceunnecessarymovements #reducewaiting #jobchangeover #5S #leanmanufacturing #pipeandjointsystem
El sistema más antiguo de la parte trasera hace que los carros de madera se almacenen de punta. Esto provoca un problema de seguridad y posibles lesiones a un miembro del equipo por astillas. Un sistema apilable le permite almacenar más carros en un espacio más pequeño, fácil de mover por el miembro del equipo que no necesita una carretilla elevadora y sin posibilidad de astillas.
#mudas #reduceunnecessarytransport #safetyfirst #stackable #leanmanufacturing #pipeandjointsystem
Carros de material móviles – Permiten varias ventajas operativas. Puede llevar el carro a la zona de reposición, llenarlo con cuatro bobinas y volver, suprimiendo la necesidad de dos viajes del operario (pérdida de movimiento). Se asegura de tener el material correcto porque el carro está diseñado para acomodar el artículo correcto en las cantidades correctas (gestión de inventario).
#mudas #reduceunnecessarymotion #reducewaiting #reduceexcessinventory #leanmanufacturing #pipeandjointsystem
Asegurarse de tener a la vista TODAS las herramientas manuales correctas permite ver inmediatamente si se necesita alguna de ellas. Reduce el desperdicio (de tiempo y movimiento) buscando elementos y elimina la necesidad de costosas cajas de herramientas.
#mudas #reducewaiting #reduceunnecessarymovements #5S #leanmanufacturing #pipeandjointsystem
Estaciones de limpieza – Asegurar que cada proceso tenga las herramientas importantes y apropiadas para la limpieza, reduce el tiempo de búsqueda de herramientas y asegura que el proceso tenga las herramientas correctas.
#cleaningstation #reducewaiting #mudas #5S #leanmanufacturing #pipeandjointsystem
Estaciones del operador – El correcto dimensionamiento de la encimera evita que se almacenen allí elementos adicionales. El uso de los colores amarillo y rojo para indicar la condición temprana y le da tiempo para hacer una contramedida antes de que se presente un problema. El uso de un enfoque de esqueleto también evita que las áreas se llenen de artículos no necesarios en el proceso.
#visualmanagement #reducewaiting #mudas #spaceoptimization #5S #leanmanufacturing #pipeandjointsystem