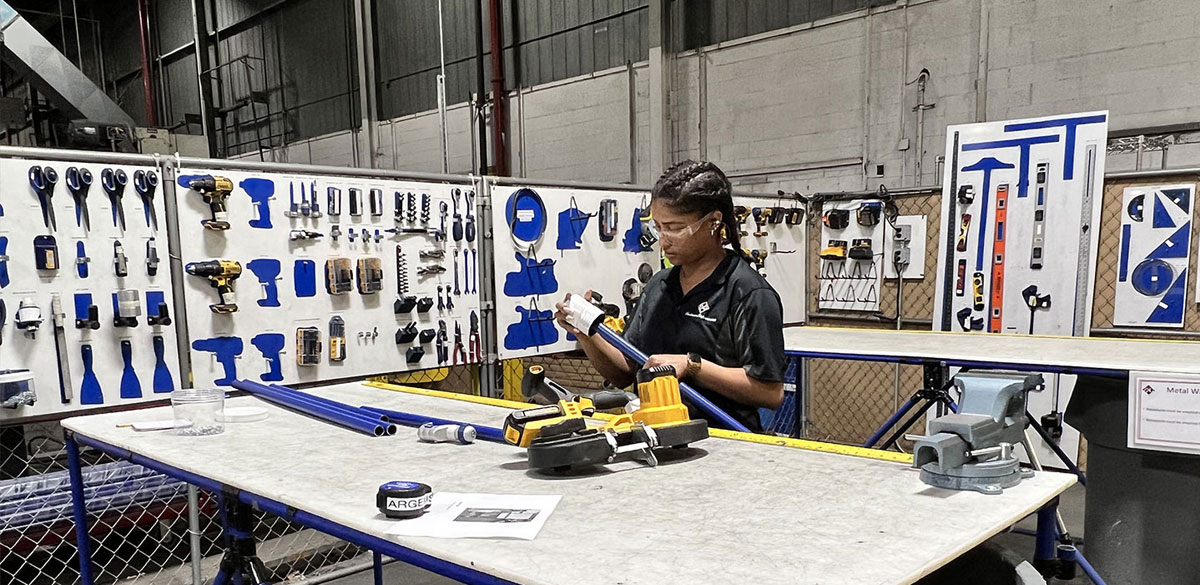
Post
CÓMO ESTABLECER Y MANTENER UNA CULTURA DE MEJORA CONTINUA
Post
CóMO TRATAR LOS RESIDUOS DEL MOVIMIENTO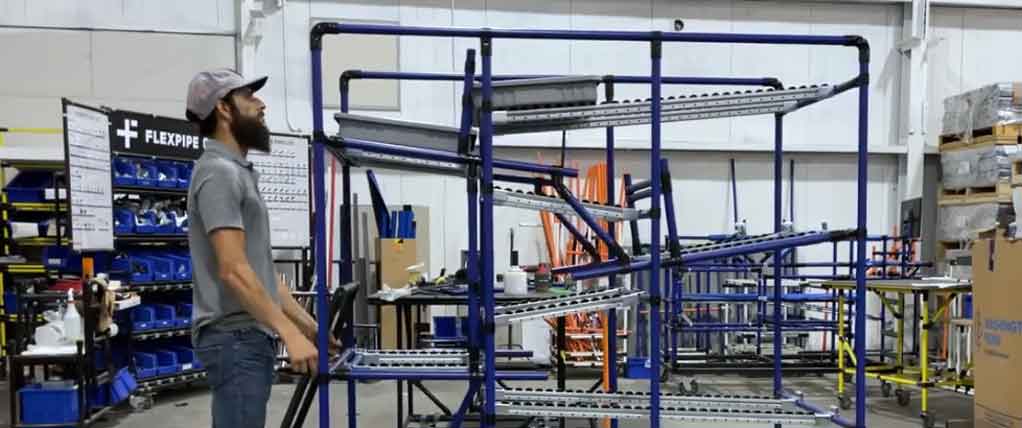
Post
CUATRO BENEFICIOS DEL KARAKURI EN LAS OPERACIONES LEANMIndependientemente de la empresa -o del sector-, los altos directivos de las empresas manufactureras necesitan tomar decisiones basadas en hechos fríos, duros e irrefutables. Necesitan números. Necesitan datos. Necesitan asegurarse de que su decisión de avanzar tiene una alta probabilidad de éxito.
Los altos directivos necesitan esta información crítica para tomar una decisión de ir o no ir sobre los gastos de capital, la contratación, la expansión, las reparaciones de máquinas y equipos, o, más acertadamente, para llevar a cabo proyectos de mejora continua.
Obtenga más información sobre los tres principios fundamentales necesarios para convencer a los altos directivos de que lleven a cabo iniciativas de mejora continua y sobre cómo las estructuras de Flexpipe son fundamentales para lograr ese objetivo, con la opinión de Leslie Pickering y Mark Zeilinger de Quadrant 5.
En los entornos de fabricación, los residuos pueden adoptar muchas formas. Puede incluir paradas de trabajo, errores humanos, piezas desalineadas o fuera de tolerancia, piezas mal ensambladas, tiempos de inactividad de las máquinas, tareas redundantes, tareas repetitivas o cualquier acción o proceso que inhiba el flujo natural de trabajo.
A veces, reducir los residuos en la fabricación puede ser tan sencillo como reducir los tiempos de tránsito para mover las piezas en proceso entre las células. Puede incluir la renovación de una estación de trabajo para que el proceso de montaje sea más fluido y el operario de la estación de trabajo tenga un acceso más fácil a los materiales y las herramientas.
Independientemente del enfoque que se adopte, estos cambios parecen inicialmente pequeños. Sin embargo, cuando se repiten en todas las células de trabajo, estos pequeños cambios se suman rápidamente hasta que se reducen los costes, se mejora la calidad y se producen más productos acabados. Desgraciadamente, como estos pequeños pasos parecen tan intrascendentes, los altos directivos tienen dificultades para ver los beneficios de la adopción de los conceptos lean.
Como afirma Leslie, “los altos directivos son realmente buenos en el desarrollo de visiones globales -en las que pueden ver el juego final o el objetivo final-, pero a menudo no adoptan un proceso secuencial sobre cómo se alcanzan esos objetivos, qué pasos hay que dar secuencialmente para llegar a ellos. Tu trabajo en la mejora continua es explicar los pasos para alcanzar ese objetivo”.
En última instancia, la adopción de iniciativas de mejora continua puede resumirse en tres pasos fundamentales. Leslie afirma: “1. Esto es lo que está ocurriendo actualmente. 2. Esto es lo que intentamos hacer, y 3. Estos serán los beneficios de la implantación de lean”. Entonces, ¿significa eso que basta con verbalizar estas cuestiones a la alta dirección para que acepten rápidamente emprender iniciativas lean? No, no es así.
Estos tres pasos no son más que directrices. Debe reunir los datos concretos que los altos directivos necesitan para implantar Lean. Su objetivo es recopilar los datos y definir las métricas que ayudarán a los altos directivos a medir el retorno de la inversión (ROI) para la puesta en marcha de la mejora continua en toda la planta de producción.
Todas las operaciones o tareas de trabajo implicadas en la fabricación de un producto tienen un tiempo de ciclo. Reducir los tiempos de ciclo significa que se fabrican más productos a un coste menor. La pregunta que los directivos quieren que se les responda es si el ahorro que supone la implantación de lean es mayor que el coste de la misma.
En nuestro ejemplo, utilizamos un diagrama de ciclo básico (abajo) que muestra los pasos para fabricar un producto. Nuestro diagrama de ciclo básico define cada proceso de trabajo o paso de fabricación que interviene en la fabricación de un producto ficticio.
Para simplificar, supondremos que cada uno de estos “pasos” representa una única celda de trabajo. Cada celda tiene un tiempo de ciclo específico para una operación de trabajo determinada, es decir, el tiempo que tarda un operario en completar una tarea.
Cada celda tiene también un volumen de producción: el volumen de piezas semiacabadas que la celda completa antes de que esas piezas pasen a la siguiente cadena del proceso.
El objetivo de este ejercicio es recopilar datos sobre cómo las iniciativas Lean pueden 1) reducir los tiempos de ciclo, 2) aumentar el rendimiento, 3) reducir los costes de fabricación y 4) acortar el plazo de entrega de los productos acabados a los clientes.
Al final del ejercicio, dispondrá de los datos necesarios para mostrar a la alta dirección lo que estaba ocurriendo, lo que ha cambiado y por qué, y cómo la realización de cambios similares en todas las células dará como resultado una reducción de los tiempos de ciclo, un aumento de la producción y una reducción de los costes, o, parafraseando a Leslie, “los beneficios de la implantación de lean”.
Aunque los operadores cobren por un turno de 8 horas, no trabajan un total de 8 horas. Hay que tener en cuenta dos descansos de 15 minutos por la mañana y por la tarde y luego el almuerzo. En nuestro ejemplo, supondremos que se trata de un almuerzo de una hora. Eso deja 6,5 horas de tiempo de trabajo real disponible.
Ahora bien, nadie puede trabajar al 100% de eficiencia. La gente va al baño, le llaman o le interrumpen por razones válidas. Vamos a suponer que el operario trabaja con un 85% de eficiencia. Esto significa que el tiempo de trabajo es de 5 horas y 35 minutos.
Ahora utilizaremos esas 5 horas y 35 minutos para calcular el rendimiento de la celda de trabajo.
Todo proceso lean tiene un comienzo, y supondremos que ese comienzo incluye que usted se centre en una evaluación inicial de una sola celda de trabajo. Empiece por evaluar los tiempos de ciclo de cada tarea en la celda de trabajo elegida.
Asegúrese de que el operador o empleado de la celda entiende que su objetivo es ayudar a facilitar su trabajo.
Haz que se sientan parte del proceso y estarán más que dispuestos a mostrarte algunos de los problemas con los que se encuentran.
Asegúrate de que entienden que este ejercicio no consiste en cronometrarlos, sino en captar las causas de los paros laborales.
Marca de la Q5: “Siempre tocamos el elemento humano. ¿Cómo se consigue que la gente se comprometa? Ahí es donde se producen las mejoras. Nadie conoce mejor ese equipo o maquinaria que el propio operario. Por tanto, se necesita realmente su aportación”. El enfoque consiste en crear “una isla de excelencia”, algo que la gente pueda señalar como ejemplo. Así que hay que dar a la gente un reconocimiento: una palmadita en la espalda y hacer que se sientan parte del proceso de mejora continua”.
Operación | Work Cell #1 | ||||
Unidad de medida | Duración del ciclo en minutos convertida en segundos | ||||
Producto | Widget X | ||||
Minutos de preparación | Conversión de minutos a segundos | Número de operaciones de trabajo | Duración del ciclo | Conversión de minutos a segundos | Comentarios / Notas |
30 | 1800 | 1 | 7,00 | 420,00 | Falta de material (el operador tuvo que buscar el material) |
2 | 8,00 | 480,00 | Faltan instrucciones de montaje (El operador tuvo que buscar las instrucciones) | ||
3 | 25,00 | 1500,00 | Hoja de sierra rota / No hay reemplazo (el operador tuvo que dejar la celda de trabajo e ir a las tiendas para conseguir una hoja de reemplazo) | ||
4 | 5,00 | 300,00 | No hay problemas – tarea de trabajo limpia | ||
5 | 5,00 | 300,00 | No hay problemas – tarea de trabajo limpia | ||
6 | 8,50 | 510,00 | Faltan instrucciones de montaje (El operador tuvo que buscar las instrucciones) | ||
7 | 9,00 | 540,00 | Falta de herramienta (la falta de colocación de la herramienta provocó el retraso) | ||
8 | 5,00 | 300,00 | No hay problemas – tarea de trabajo limpia | ||
9 | 5,00 | 300,00 | No hay problemas – tarea de trabajo limpia | ||
10 | 15,00 | 900,00 | Falta de herramienta (la falta de colocación de la herramienta provocó el retraso) | ||
Promedios | 9,25 | 393,90 | |||
Asegúrese de que el operador o empleado de la celda entiende que su objetivo es ayudar a facilitar su trabajo.
Haz que se sientan parte del proceso y estarán más que dispuestos a mostrarte algunos de los problemas con los que se encuentran.
Asegúrate de que entienden que este ejercicio no consiste en cronometrarlos, sino en captar las causas de los paros laborales.
Marca de la Q5: “Siempre tocamos el elemento humano. ¿Cómo se consigue que la gente se comprometa? Ahí es donde se producen las mejoras. Nadie conoce mejor ese equipo o maquinaria que el propio operario. Por tanto, se necesita realmente su aportación”. El enfoque consiste en crear “una isla de excelencia”, algo que la gente pueda señalar como ejemplo. Así que hay que dar a la gente un reconocimiento: una palmadita en la espalda y hacer que se sientan parte del proceso de mejora continua”.
Va a crear su propia “isla de excelencia” utilizando estos tiempos de ciclo iniciales dentro de la celda para mostrar los problemas a los que se enfrenta el operador a diario. También capturará los motivos de los retrasos o las interrupciones del trabajo.
En nuestro ejemplo, los tiempos de ciclo sin problemas se realizan en cinco minutos o 300 segundos. Lo hemos convertido a segundos porque incluso los cambios más pequeños que ahorran un par de segundos pueden tener un impacto dramático.
Ahora, el tiempo de ciclo de 5 minutos puede no ser el tiempo de ciclo optimizado, pero para este ejemplo, es el mejor tiempo de ciclo que esta celda produce.
Sin embargo, el tiempo de ciclo promedio en la parte inferior está sesgado por las operaciones (1,2,3,6,7, y 10) que encontraron paradas de trabajo. Esto significa que estas paradas de trabajo empujaron el tiempo de ciclo promedio a 9 minutos, 25 segundos, o 555 segundos.
No hay una regla rígida sobre el número de tiempos de ciclo que debe registrar. En nuestro ejemplo anterior, hemos registrado diez tiempos de ciclo. Hemos convertido esos tiempos de minutos a segundos para simplificar el cálculo de cuánto produce la célula de trabajo.
La siguiente tabla resume los datos que has recogido de la célula de trabajo. Ahora, es más que probable que ya sepa lo que produce una célula de trabajo determinada. También puede saber cuáles son los tiempos de ciclo. Muchas soluciones de software MRP y ERP proporcionan datos sobre los tiempos de ciclo.
Sin embargo, ningún software puede mostrarle cómo reducir los tiempos de ciclo. Sólo puede informar de ellos. Sólo puede proporcionar números. Hay que ver por sí mismo las causas de las paradas de trabajo. Sólo entonces podrá poner en marcha estrategias para reducir esos tiempos de ciclo y aumentar el rendimiento.
Operación | Duración media del ciclo en minutos | Duración media del ciclo en segundos | Número total de segundos (5 horas 5 minutos) | Rendimiento de la célula de trabajo | ||
Work Cell #1 | 9,25 | 555,00 | 18300 | 33 | ||
Ahora tiene datos en una celda de trabajo que define la primera afirmación de Leslie: “Esto es lo que está ocurriendo actualmente”. Tiene una lista de los retrasos más comunes que encuentra el operario en la célula de trabajo. Usted conoce las causas de los tiempos de ciclo más altos y puede promulgar estrategias para eliminar esas causas.
Uno de sus cambios incluyó la fabricación de un estante de almacenamiento de herramientas Flexpipe modular y escalable. A continuación, colocó este estante inmediatamente fuera de la célula de trabajo, por lo que el operario ya no tiene que caminar hasta el inventario para conseguir hojas de sierra de repuesto.
Otro cambio fue la creación de una estación de trabajo Flexpipe en la que todas las herramientas y los consumibles están fácilmente localizados. Ha combinado esta nueva estación de trabajo con un estante de flujo modular para que los consumibles y materiales de repuesto estén siempre disponibles.
Por último, ha creado un centro de trabajo modular de Flexpipe donde el operario puede acceder fácilmente a las instrucciones de montaje.
Estantería de almacenamiento: Piezas de máquinas (cuchillas) | Estación de trabajo modular | Estantería de flujo modular | Centro de trabajo modular con instrucciones |
![]() | ![]() | ![]() | ![]() |
Después de realizar estos cambios, se vuelve a visitar la célula de trabajo y se toma un nuevo conjunto de tiempos de ciclo.
Aunque todavía hay operaciones que sufren algunos retrasos, el beneficio general es que se han conseguido más operaciones que cumplen el tiempo de ciclo deseado.
Operación | Work Cell #1 | ||||
Unidad de medida | Duración del ciclo en minutos convertida en segundos | ||||
Producto | Widget X | ||||
Minutos de preparación | Conversión de minutos a segundos | Número de operaciones de trabajo | Duración del ciclo | Conversión de minutos a segundos | Comentarios / Notas |
30 | 1800 | 1 | 5,00 | 300,00 | No hay problemas – tarea de trabajo limpia |
2 | 7,00 | 420,00 | Pieza desalineada – pequeño ajuste | ||
3 | 5,00 | 300,00 | No hay problemas – tarea de trabajo limpia | ||
4 | 5,00 | 300,00 | No hay problemas – tarea de trabajo limpia | ||
5 | 5,00 | 300,00 | No hay problemas – tarea de trabajo limpia | ||
6 | 7,35 | 441,00 | Herramienta de repuesto necesaria – fácil de encontrar – pequeño retraso | ||
7 | 7,30 | 438,00 | Herramienta de repuesto necesaria – fácil de encontrar – pequeño retraso | ||
8 | 5,00 | 300,00 | No hay problemas – tarea de trabajo limpia | ||
9 | 5,00 | 300,00 | No hay problemas – tarea de trabajo limpia | ||
10 | 14,00 | 840,00 | Hoja de sierra rota – La hoja de sierra de reemplazo en el estante de flujo de materiales inmediatamente fuera de la célula de trabajo minimizó el tiempo de reemplazo. | ||
Averages | 6,57 | 393,90 | |||
Un nuevo puesto de trabajo facilitó al operador la localización de las herramientas de recambio.
La colocación de un estante de almacenamiento para las hojas de sierra de repuesto redujo inmediatamente el tiempo que el operario tardaba en sustituir la hoja.
En lugar de un tiempo de ciclo de 25 minutos o un “retraso”, el operario se limitó a localizar la cuchilla de repuesto y a realizar un cambio que sólo le llevó 14 minutos. Finalmente, su tiempo de ciclo medio se redujo a 6 minutos y 57 segundos.
Los tiempos de ciclo más bajos significan que la célula de trabajo aumentó su rendimiento en un 41%, de 33 a 46 unidades.
Operación | Duración media del ciclo en minutos | Duración media del ciclo en segundos | Número total de segundos (5 horas 5 minutos) | Rendimiento de la célula de trabajo | ||
Work Cell #1 | 6,57 | 393,90 | 18300 | 46 | ||
Aumentar el rendimiento en una celda de trabajo no consigue nada si las demás celdas de trabajo no realizan cambios similares de mejora continua. Todo lo que está haciendo es crear un retraso para la siguiente celda del proceso.
Ha aumentado el rendimiento de la celda, pero si no realiza cambios similares en las demás celdas de trabajo, todo es inútil. En este punto, ha reunido suficientes datos para mostrar cómo la realización de pequeños cambios incrementales puede tener un impacto dramático en el rendimiento de una celda de trabajo.
Los altos cargos no suelen tener más remedio que avanzar en iniciativas adicionales de mejora continua cuando se les presentan estos datos. Ahora es muy fácil para ellos ver cómo la repetición del proceso conducirá a mejoras y ahorros significativos.
Los costes de una estructura Flexpipe incluyen el coste de los materiales y el tiempo que tardan sus operarios en montar las estructuras. Ese coste inicial es mínimo si se compara con los beneficios constantes de la aplicación de los principios lean. Los beneficios del lean son para siempre.
Como afirma Mark: “Eso es lo que nos gusta de Flexpipe. Es muy fácil probar algo. No hay ningún inconveniente. Si cortamos un tubo demasiado corto, lo utilizaremos en otro sitio”.
En última instancia, la empresa lograría los siguientes beneficios si se llevaran a cabo iniciativas de mejora continua similares con el resto de las células.
Flexpipe es un proveedor, diseñador e integrador con sede en Montreal de sistemas modulares y escalables de tubos y juntas para la manipulación de materiales. El enfoque centrado en el cliente y el enfoque proactivo de la empresa permiten a los fabricantes realizar sus estructuras a una fracción del coste en comparación con los sistemas fijos de manipulación de materiales.
La extensión de diseño gratuita de la empresa para el programa SketchUp es fácil de usar y proporciona un diseño completo en 3D, un desglose de costes de material y una lista de materiales.
Si desea ver cómo Flexpipe puede ayudarle en su próximo proyecto de mejora continua, póngase en contacto con nosotros ahora.
El Sr. Pickering es licenciado en ingeniería mecánica y de producción. Aporta 35 años de experiencia en la mejora de procesos internacionales, fabricación y operaciones. Es un reconocido especialista en el Sistema de Producción Toyota y está muy bien considerado como experto en el campo de la fabricación ajustada.
El Sr. Zeilinger es licenciado en Ingeniería Mecánica. Aporta más de 30 años de experiencia en fabricación y operaciones. El Sr. Zeilinger es un reconocido especialista en el Sistema de Producción Toyota, que ha implantado con éxito metodologías de transformación en una amplia variedad de sectores, como el de los envases, la electrónica, la construcción, los plásticos, la alimentación, la automoción y el aeroespacial.