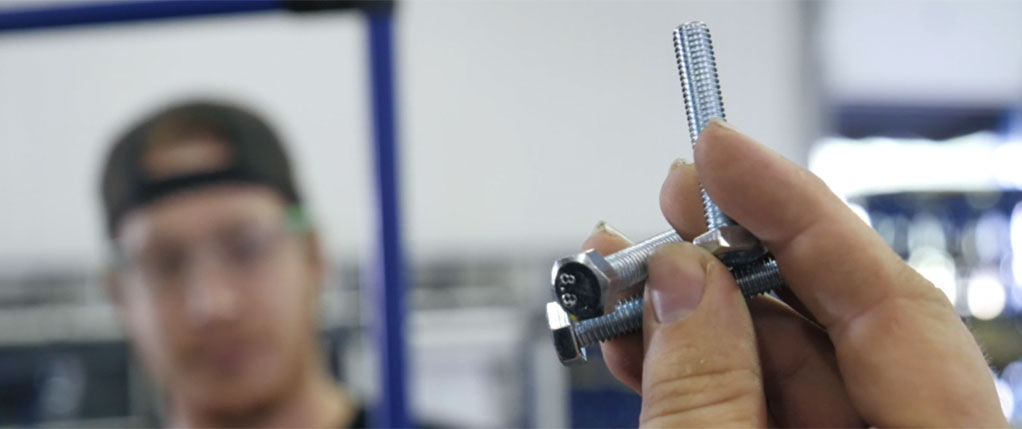
Post
CUáL ES EL PAPEL DEL WATERSPIDER EN UNA ESTRUCTURA DE FABRICACIóN AJUSTADA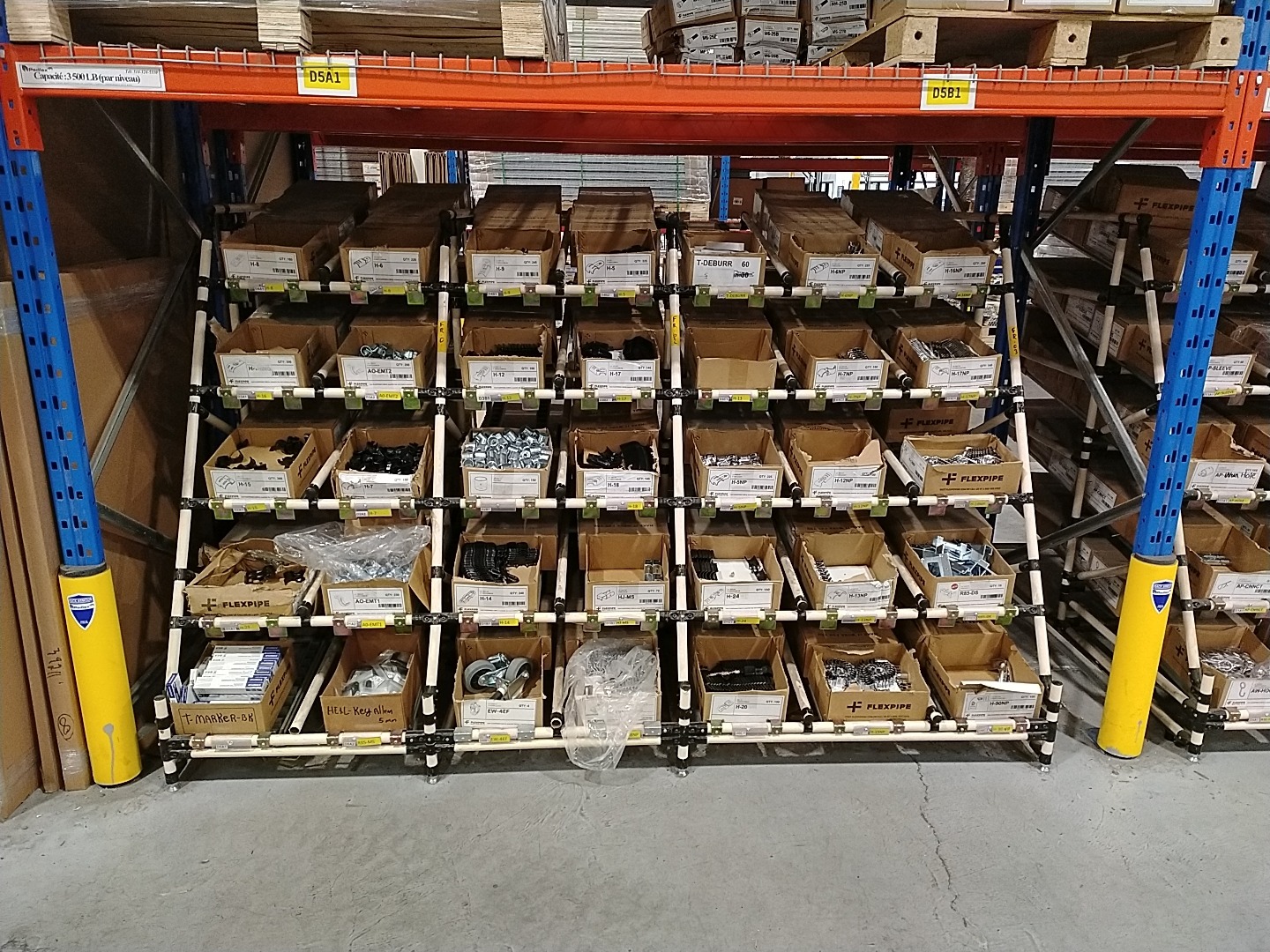
Post
POKA-YOKE: UNA FORMA SENCILLA Y COMPROBADA DE EVITAR ERRORES EN LA FABRICACIóN
Case Study
UN IMPORTANTE FABRICANTE DE CARTÓN CORRUGADO SE ADAPTA CON FLEXPIPEEl mundo de la manufactura esbelta debe mucho a Sakichi Toyoda, a su hijo Sakichi Toyoda y a un ingeniero japonés muy respetado llamado Taiichi Ohno. Juntos crearon el Sistema de Producción Toyota (TPS) e introdujeron varios principios empresariales sencillos, pero muy eficaces, que siguen dando resultados y mejorando la eficiencia de la fabricación hasta el día de hoy.
Uno de estos principios es el de las 5S, una metodología de mejora continua ampliamente reconocida como uno de los pilares de la manufactura esbelta. Las 5S fueron la punta de lanza de la iniciativa “justo a tiempo” (JIT), un proceso de gestión de la cadena de suministro y de fabricación esbelta que minimiza los residuos y maximiza la eficiencia.
5S es un acrónimo de cinco palabras japonesas: seiri, seiton, seisō, seiketsu y shitsuke. Cuando se traducen, se convierten en los pilares de un proceso repetible que simplifica la estructura, la organización y la limpieza del lugar de trabajo.
En inglés, 5S significa “Sort”, “Set in Order”, “Shine”, “Standardize” y “Sustain”.
Las 5S consisten, en definitiva, en adoptar comportamientos y prácticas repetitivas para estandarizar el entorno de trabajo de una empresa. Las 5S son el primer paso importante para garantizar la repetibilidad de los procesos de trabajo; la definición de directrices para la gestión, la estructura, la organización y la limpieza del lugar de trabajo ayuda a eliminar las paradas, las interrupciones, los desperdicios y los retrasos que consumen tiempo. El resultado son unos resultados más predecibles y una
mayor calidad.
A primera vista, las 5S parecen ser un simple conjunto de reglas que se aplican y siguen fácilmente. Sin embargo, si se da un paso más, queda claro que las 5S sólo tienen éxito cuando las empresas mantienen su compromiso con el proceso.
No se trata de un ejercicio único. No es una solución de tipo “set-it-and-forget-it”. Las 5S requieren una plantilla comprometida con la disciplina de seguir el proceso a diario. Debe formar parte de la cultura de la empresa para que el hábito de seguir los pasos de las 5S se arraigue en la plantilla. A continuación se presenta un desglose de las 5S junto con algunas preguntas y cuestiones a tener en cuenta para cada paso.
Clasificar todos los materiales, herramientas y artículos diversos dentro de una celda o espacio de trabajo. Identificar los materiales y objetos necesarios para completar las tareas de trabajo. Descartar, retirar o apartar cualquier elemento o material no esencial. Asegúrese de que en la célula de trabajo sólo queden las cosas necesarias para realizar las tareas.
Adopte un enfoque ergonómico para organizar los elementos que quedan. Asegúrese de que los artículos estén correctamente identificados para que los operarios o técnicos puedan acceder a ellos de forma segura, eficiente y rápida. Cada material, herramienta, instrucción de trabajo o consumible debe tener una ubicación designada y estar adecuadamente etiquetado y fácilmente accesible.
Los tableros de sombra facilitan la creación de contornos de piezas y el uso de soportes de colocación para que todo encaje exactamente donde debe hacerlo.
Asegúrese de que el espacio de trabajo esté limpio, bien mantenido, organizado y libre de obstáculos. Una limpieza al final del día o del turno es absolutamente necesaria. Esto puede implicar barrer o fregar el suelo, limpiar las herramientas y las superficies de los bancos de trabajo, o asegurarse de que el equipo y la maquinaria se mantienen y limpian adecuadamente.
Una cuna Flexpipe es una forma perfecta de estandarizar un lugar de trabajo. Hace que el lugar de trabajo sea más atractivo visualmente y reduce la pérdida de tiempo en la búsqueda de piezas, materiales
y consumibles.
Acaba con el tribalismo creando normas 5S en toda la empresa para la gestión del lugar de trabajo. Cree una lista de comprobación diaria para los empleados y programe talleres para que todos los empleados y directivos conozcan las mejores prácticas de las 5S. El objetivo es duplicar el éxito para que las 5S se conviertan en una rutina para los empleados.
Las 5S son un proceso interminable. Cuando se adopta adecuadamente, se convierte en parte de la cultura de la empresa. Las auditorías periódicas de las 5S y las reuniones de las 5S permiten a los empleados y a la dirección evaluar los progresos o revisar los incumplimientos. El refuerzo constante de las directrices de las 5S garantizará que se arraiguen en la plantilla.
El objetivo de las 5S en los entornos de fabricación esbelta es aportar estabilidad y organización a los entornos de trabajo. En este sentido, las 5S son un elemento fundamental de la manufactura esbelta. Simplifica la organización
del lugar de trabajo mediante la creación de directrices sencillas de utilizar que ayudan a reducir el impacto de los residuos
en la fabricación.
Las 5S fueron un secreto muy bien guardado por Toyota hasta finales de los 80 y principios de los 90. El crecimiento de Toyota -y el auge económico de los años 80- estimuló el interés mundial por los procesos de Toyota. Las industrias occidentales conocieron los entresijos del Sistema de Producción Toyota y pronto empezaron a adoptar las prácticas de las 5S para hacer frente a lo que el Sistema de Producción Toyota definía como ocho formas de desperdicio.
Las empresas suelen producir más de lo que necesitan, o más de lo que demandan actualmente. Estas empresas creen que es mejor tener máquinas y equipos en funcionamiento que tenerlos inactivos. Por desgracia, fabricar más de lo necesario aumenta los costes de producción y almacenamiento. Puede dar lugar a errores de producción, interrumpir el flujo de trabajo y aumentar los tiempos de entrega (TAT).
El exceso de inventario aumenta los costes de financiación y provoca la obsolescencia de piezas y materiales, daños, existencias muertas y mayores costes de manipulación y almacenamiento. Las empresas que tienen demasiado inventario no se benefician de las economías de escala cuando el inventario se daña debido a la excesiva manipulación y almacenamiento.
Los movimientos excesivos e innecesarios aumentan la duración del ciclo y reducen el rendimiento de la producción. Esto puede incluir que los empleados tengan que recorrer
largas distancias para conseguir piezas, herramientas y materiales, hasta algo tan simple como hacer que se agachen, levanten, estiren o alcancen con demasiada frecuencia.
Los puestos de trabajo ergonómicos hacen hincapié en el mínimo movimiento para que el trabajo sea fluido y el operario no se esfuerce en exceso con movimientos innecesarios.
Los procesos de trabajo deficientes, los cuellos de botella, los procedimientos ineficaces, las aprobaciones excesivas y el flujo de trabajo enrevesado hacen perder tiempo de producción. Las tareas redundantes y repetitivas añaden tiempo innecesario y aumentan los costes sin añadir valor.
Un flujo de trabajo mal estructurado hace que la maquinaria y los equipos estén inactivos. Cuando las operaciones de trabajo no están cronometradas, la maquinaria, los equipos y los empleados de producción esperan por el material y las piezas semiacabadas o en proceso. Con el tiempo se produce una sobreproducción y se crea un inventario excesivo.
Las largas distancias entre las células de trabajo aumentan los tiempos de tránsito de las piezas en proceso y semiacabadas.
Cualquier transporte o movimiento excesivo de personas, equipos, piezas, herramientas y maquinaria añade tiempo y aumenta los residuos.
Los defectos del producto aumentan los costes y afectan a la calidad. La mayoría de los defectos deben ser reelaborados o reparados, lo que añade un tiempo innecesario.
Los defectos pueden producirse por procesos de trabajo repetitivos, material defectuoso, formación deficiente, herramientas inadecuadas, manipulación o transporte excesivos o instrucciones de trabajo mal definidas.
Los empleados que trabajan en silos roban a otros empleados conocimientos y experiencia esenciales. No aprovechar al máximo la capacidad, el talento y la perspicacia de un empleado conduce a la complacencia, la indiferencia y la rotación de personal.
Los directivos deben involucrar a los empleados y hacerles partícipes del proceso de mejora continua.
Uno de los aspectos más impresionantes de las 5S es lo poco que cuesta ponerlas en marcha. No hay que justificar ni aprobar gastos de capital significativos. No hay que comprar equipos o maquinaria y apenas se necesitan consultores externos.
Lo que se necesita es la voluntad de la dirección y de los empleados de invertir tiempo y esfuerzo para que las 5S sean un éxito. Una empresa puede ponerse en marcha con las 5S sin necesidad de gastar mucho dinero. Todo lo que se necesita son las siguientes colas visuales.
La seguridad de los empleados es cada vez más importante en los entornos de fabricación actuales. Por eso algunos abogan por la “seguridad” como sexto criterio. Los sistemas 6S se centran en definir claramente los riesgos de seguridad y en minimizar los peligros y obstáculos. Las células de trabajo deben diseñarse teniendo en cuenta la ergonomía.
Los empleados deben tener unos movimientos mínimos para realizar las tareas de trabajo sin esforzarse demasiado. El objetivo es mitigar el impacto o la incidencia de las lesiones para evitar los elevados costes del absentismo laboral. Las empresas ven ahora el absentismo como un factor de coste perjudicial. El objetivo es reducir este despilfarro garantizando que la seguridad de los trabajadores sea una prioridad.
Identificar los residuos puede parecer algo desalentador. ¿Por dónde empezar exactamente? Afortunadamente, las 5S son una metodología de mejora continua. El objetivo es trabajar en ella continuamente. Es una tarea sin fecha de finalización. No hay un calendario. Es un bucle de retroalimentación continua en el que cada mejora se utiliza para aprender y crecer.
Hay varias formas de identificar los residuos. Los diagramas de espaguetis trazan el movimiento de las piezas, las personas, los materiales y las piezas en proceso en su taller. Estos diagramas pueden identificar rápidamente el movimiento excesivo y los flujos de trabajo desiguales.
Otro método consiste en utilizar el Mapeo del Flujo de Valor (VSM). Esta herramienta de manufactura esbelta de gran eficacia permite a las empresas definir la cantidad actual de residuos en sus procesos, desde el cliente hasta la producción y el envío.
Sin embargo, por muy impresionantes que sean estas herramientas, nada es comparable a ver el trabajo realizado en tiempo real. Sus empleados tienen todas las claves para mejorar los procesos.
Ellos saben dónde están los cuellos de botella.
Saben qué causa la pérdida de tiempo y dónde están los residuos.
Aprovechar su experiencia, sus conocimientos y su capacidad para resolver problemas ayudará a mejorar la eficiencia y la productividad.
Las 5S son sólo una herramienta, pero sus empleados son fundamentales para que funcionen.
Como innovador en sistemas de manejo modular, Flexpipe ha desarrollado una gran base de clientes en toda América del Norte. Flexpipe no solo es menos costoso (30% menos) que sus competidores, sino que también ofrece múltiples servicios enfocados en el cliente para ayudarlos a integrar fácilmente sistemas de tuberías y uniones en sus sistemas de fabricación.
Estos servicios incluyen visitas y evaluaciones dentro de la planta, ensamble personalizado, excelente soporte post venta y la exclusiva extensión gratuita Flexpipe Creator para respaldar los diseños de sistemas de manejo de materiales hechos de materiales modulares.